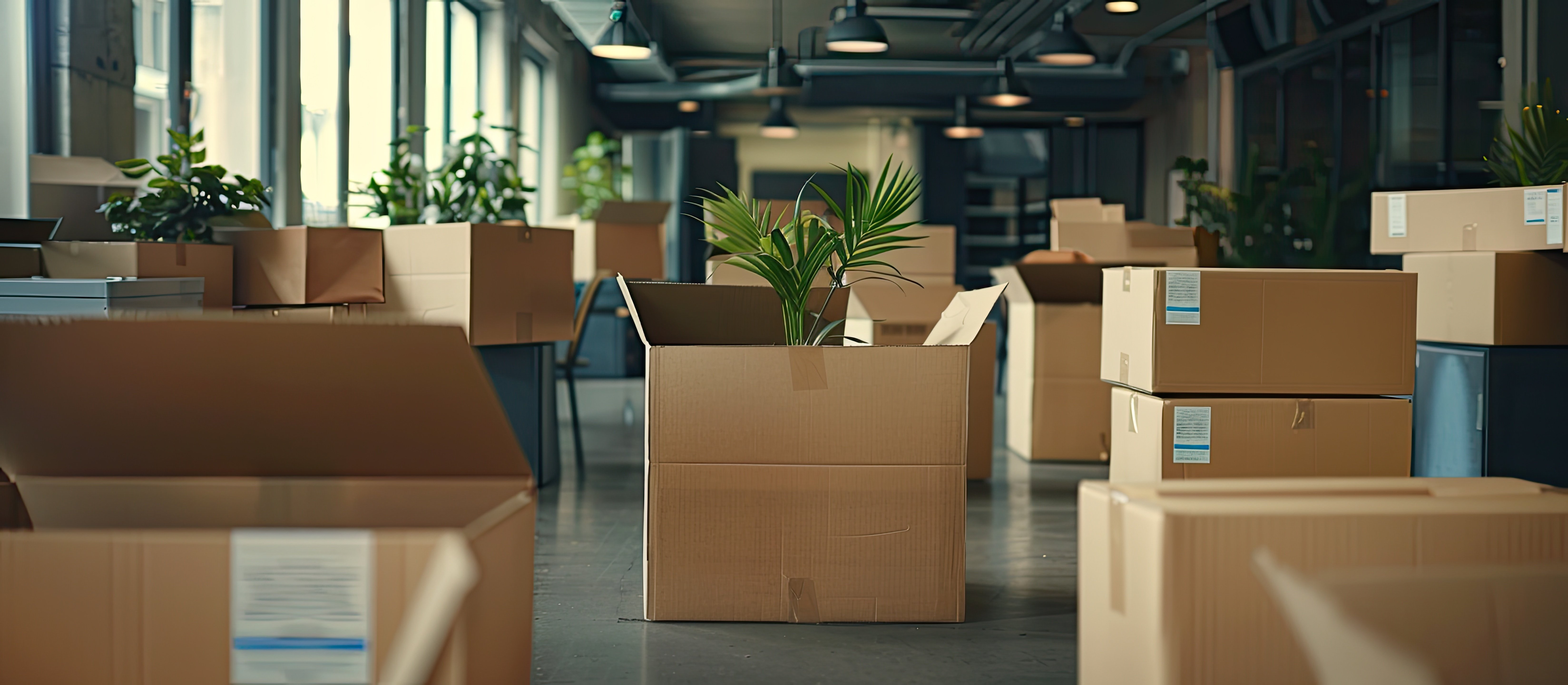
Theoretically, at least, graphene can be produced from any carbon source. While the pursuit of scalable manufacturing for this extraordinarily strong and conductive material continues, so too does the search for a production method that is also sustainable.
The desire for sustainable development is pushing researchers towards more environmentally friendly ways to produce carbon-based nanomaterials. This might be by altering the reagents used in existing synthetic approaches, reducing the quantities of expensive or environmentally damaging components needed, or even utilizing new carbon sources in innovative ways.
One approach recently announced by researchers from RMIT University in Australia and the National Institute of Technology, Warangal, India, has used eucalyptus bark extract in the synthesis of graphene sheets. RMIT lead researcher Distinguished Professor Suresh Bhargava believes that this method could reduce the cost of production from $USD100 per gram to just 50 cents per gram.
By replacing the usual reducing agents in the graphene oxide -> graphene reaction with a eucalyptus bark extract, graphene can seemingly be synthesized more cleanly and more cheaply.
According to the research, when tested in the application of a supercapacitor, the 'green' graphene matched the quality and performance characteristics of traditionally-produced graphene without using toxic reagents. Given the abundance of eucalyptus trees in Australia, this could be a green game-changer in the graphene world (although the koalas might have something to say about it!).
Australian trees do seem to attract graphene production research. In 2015 researchers grew graphene from the tea tree plant Melaleuca alternifolia, which is used to make essential oils in traditional medicine. According to this article in Physics World, “researchers demonstrated that they could fabricate large-area, nearly defect-free graphene films from tea tree oil in as little as a few seconds to a few minutes” using plasma-enhanced CVD.
Another recent paper from researchers at Mississippi State University proposes what it describes as a molecular cracking and welding (MCW) method to produce multi-layer graphene materials from biomass feedstock.
At Karlsruhe Institute of Technology (KIT), a team of researchers is using carbon dioxide as an inexpensive raw material to produce graphene. Clearly, successfully fixing carbon dioxide in this way would have significant implications for the environment given the action of carbon dioxide as a “greenhouse gas”.
By using a copper/palladium catalytic surface, the team reacts carbon dioxide with hydrogen (at up to 1000°C) to form graphene directly by a “simple one-step process”, according to the head of team, Professor Mario Ruben, from the Molekulare Materialien working group at the Institute of Nanotechnology (INT) and the Institute for Inorganic Chemistry (AOC) at KIT.
These techniques, using alternative carbon sources, show the wide range of avenues still available for exploration, making use of un- or under-utilized resources for an exciting new purpose.
However, sometimes moving forward is about building on the past. That is just what is going on at the University of Strasbourg now.
A team led by Paolo Samori at the University of Strasbourg has drawn inspiration from the ‘original’ graphene production technique, and from cosmetic hair waxing, to exfoliate a graphite surface and produce large quantities of exceptionally uniform product.
The researchers used Persian wax, a thick, sticky substance made with a mix of sugar, water and lemon juice. It can be applied to the skin without melting, left to dry, then quickly ripped off to remove hair. When spread on a three-roll mill, Persian wax renders the rollers adhesive. As graphite foil is fed through, the sticky surfaces can exfoliate graphene. This mimics the famous ‘ScotchTM tape’ approach used in the discovery by Professor Sir Andre Geim and Professor Sir Kostya Novoselov at the University of Manchester, UK in 2004.
According to this article in Chemistry World, Rahul Nair, professor of materials physics at the National Graphene Institute in Manchester, UK, was “amazed” by the success of Samori’s approach. “It was known that mechanically exfoliating graphite with ScotchTM tape makes the highest quality of graphene, but it was always thought that this wasn’t scalable for large-scale graphene production. Samori and his colleagues have changed this perception.”
More research and further optimisation of the process is required before it can be used at scale, but such an elegant and mild approach warrants close attention.
Whatever the approach taken, whether it’s new processes, new reagents, and new takes on old techniques, it’s clear that the next wave of graphene innovation will have a very green hue.
Matthew is a Partner and Patent Attorney at Mewburn Ellis. Working primarily in the chemical and materials science fields, he has significant experience of the intricacies of the EPO. Matthew advises and assists clients with all stages of drafting, prosecution, opposition and appeal before the EPO. Many of his clients are Japanese and Chinese businesses that are seeking European patent protection. These include multinational corporations in the fields of high-performance ceramics and carbon fibre technologies, as well as pharmaceutical and cosmetic companies. Matthew also works with several research institutions and university technology transfer departments across Europe.
Email: matthew.smith@mewburn.com
Our IP specialists work at all stage of the IP life cycle and provide strategic advice about patent, trade mark and registered designs, as well as any IP-related disputes and legal and commercial requirements.
Our peopleWe have an easily-accessible office in central London, as well as a number of regional offices throughout the UK and an office in Munich, Germany. We’d love to hear from you, so please get in touch.
Get in touch