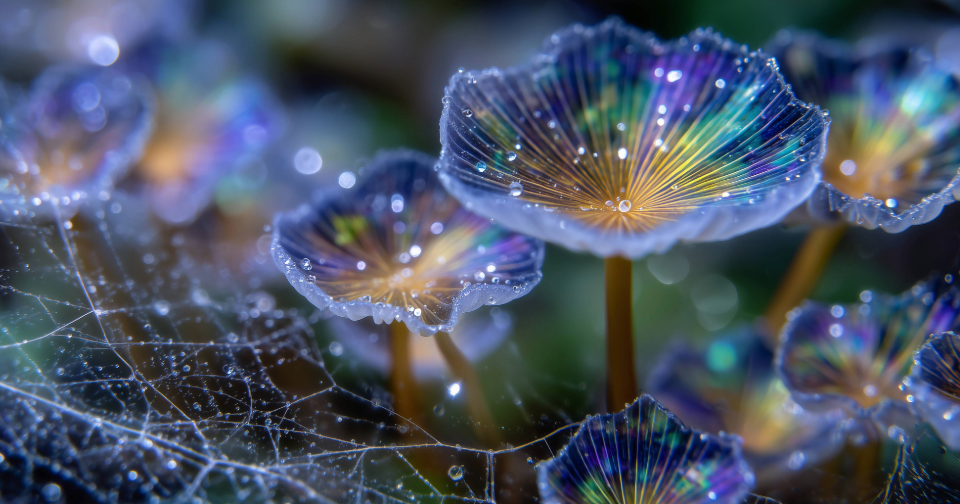
As demonstrated by the recent COP 26 UN Climate Change conference, the climate crisis is weighing ever more heavily on the minds of the world’s governments and individuals alike. As the world struggles to reduce its reliance of fossil fuels, battery technology promises to be a key tool for powering a greener future.
Renewable energy sources such as solar, wind and tidal power can provide us with a supply of clean energy. However, the availability of power from these sources can be intermittent. Some days the wind doesn’t blow and the sun doesn’t shine. Rechargeable battery technology allows power from renewable sources to be stored for use only when it is needed, smoothing the energy supply from renewables. Partly due to these benefits of stationary energy storage, Bloomberg New Energy Finance predicts that by the decade’s end the battery market will be worth $116 billion annually.
Notably, advances in battery technology whisper a future where our roads are no longer dominated by the roar of diesel or petrol engines but are instead filled with the sound of silence of electric cars. Electric cars are popular already, with global sales in electric cars having risen by 43% in 2020 to 3 million. Projections suggest that the number of electric cars will further increase rapidly within the next 20 years, so that there will be between 300 and 500 million electric cars on the roads by 2040.
However, with growing need for battery technology comes a growing requirement for the minerals needed to manufacture the batteries. The World Bank forecasts that global demand for battery materials will sky-rocket in the near future with lithium, graphite and nickel demand increasing by 965%, 383% and 108%, respectively, by 2050.
This raises the question of how raw materials for batteries will be sourced as demand for batteries grows. Unfortunately, the supply chains of some materials used in current battery technologies are linked to complicated environmental and sustainability issues.
Lithium-ion batteries include cathodes typically made of compounds of cobalt, nickel, manganese or several other metals, and anodes made of graphite. Nickel-manganese-cobalt (NMC) batteries are currently the market leaders.
Lithium and cobalt in particular present ethical and sustainability challenges associated with their extraction from natural deposits.
Lithium
About a third of the world’s lithium comes from the salt flats of Chile and Argentina. Extraction of lithium is produced by pumping brine to ground level and allowing it to evaporate in “evaporation ponds” to concentrate the lithium. This process requires the use of large amounts of water in an otherwise arid area. For instance, there are concerns that lithium mining in the Atacama desert, one of the driest places on earth, is making fresh water supplies less accessible to local indigenous populations, disrupting the habitats of the unique wildlife found in the area such as Andean flamingos and pushing out the Chilean agriculture sector.
Cobalt
The largest global supplier of cobalt is the Democratic Republic of Congo, accounting for approximately 60% of global supply. There are reports of significant human rights abuses associated with the cobalt mines in the Congo. Corruption also means that local communities currently see little financial payback from the extraction of cobalt from the landscape, a landscape which has also been damaged by sulphuric acid leaks from the cobalt mines.
To move towards a truly clean and sustainable future, battery manufacture needs to be distanced from problematic mining practices. One approach to this has been the development of alternative technology to substitute some of these metals for materials which can be more ethically sourced.
Researchers are investigating battery technologies which replace cobalt with iron or manganese (J. V. Laveda et al. Chem. Commun. 52, 9028–9031 (2016); R. Sharpe et al. J. Am. Chem. Soc. 142, 21799–21809; 2020). Tesla is working on cobalt-free battery technologies which focus more on nickel and lithium-iron-phosphate chemistries. Tesla has also reduced its use of cobalt in some of its car models already on the market. Batteries based on lithium-nickel-cobalt-aluminium chemistries reduce the amount of cobalt needed in a battery by about 60%.
Lithium-sulfur batteries are also being developed. Unlike cobalt, sulfur is a cheap material which is readily available as a by-product of the oil industry. Li-S batteries may also be able to store more energy than lithium ion batteries, reducing the weight of the resulting battery. However, current Li-S chemistry-based batteries still require further development before they will be suitable for use commercially. Li-S batteries suffer life-span issues due to chemical deposits that can degrade the lithium anode after only a limited number of charge cycles.
Creative ideas to ensure the sustainable sourcing of lithium and cobalt are also being investigated.
In the UK and Germany, pilot projects are underway where lithium is sourced sustainably by filtering it from hot brine beneath granite rock.
Volvo is using blockchain to track its cobalt supply for its electric cars. It is often hard to track the particular mines from which cobalt supplied to an end company comes. Using similar technology to that already used in the diamond industry, blockchain is being used to provide more certainty that the cobalt is not derived from sources associated with child labour and worker violations.
Ultimately, harnessing the metals and minerals already available in battery waste is a key way to move away from reliance on raw materials from mining. Batteries can be repurposed. After 8-10 years most car batteries retain about 80% of their capacity, allowing these batteries to be used for stationary storage packs for solar panels. Battery materials can also be recycled. Tesla has committed to recycling batteries from its customers’ cars. Its own research and development at its Gigafactory in Nevada has also led to a commitment to recover lithium, cobalt, aluminium, copper and steel from the batteries to use in new battery production in a “closed-loop system”.
We are relying on battery technology to move our planet towards a greener, carbon neutral future. However, if batteries are to be truly as green as we herald them to be, we need to find environmentally and socially sustainable ways to supply the materials we need for battery production. For battery technology to be truly sustainable, battery materials need to be recycled or reused wherever possible.
Genevieve is a patent attorney in our chemistry team. She has a degree in Chemistry with research abroad (Msci) from Imperial College London. Her PhD is in Chemistry from University College London. Her doctoral research focused on the development of DNA origami nanopores for use in biosensing devices.
Email: genevieve.pugh@mewburn.com
Our IP specialists work at all stage of the IP life cycle and provide strategic advice about patent, trade mark and registered designs, as well as any IP-related disputes and legal and commercial requirements.
Our peopleWe have an easily-accessible office in central London, as well as a number of regional offices throughout the UK and an office in Munich, Germany. We’d love to hear from you, so please get in touch.
Get in touch