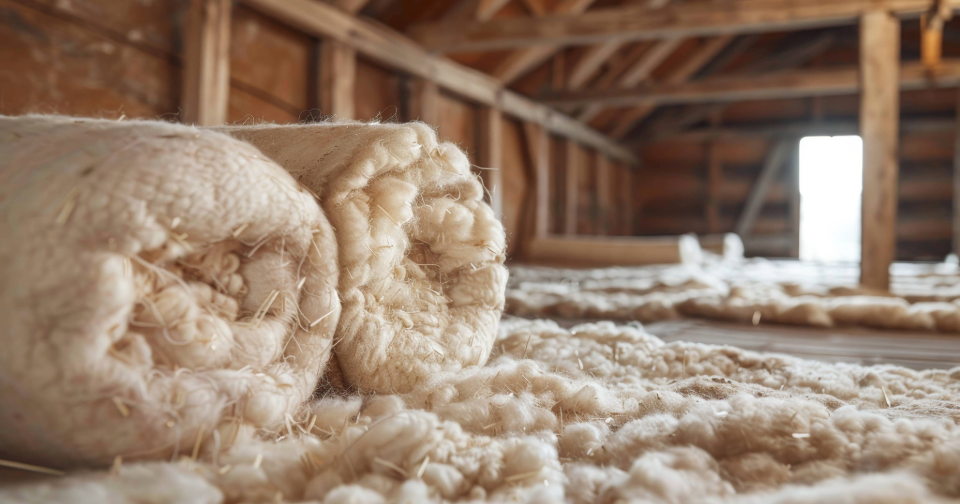
There is growing awareness and alarm at the impact humans are having on the planet. The 2022 COP26 meeting in Glasgow attracted global leaders, worldwide media and activists in their thousands. In order to meet our climate goals, we need to rapidly shift to a more circular economy and reduce our reliance on traditional single-use plastics. Technology and policy will play a key role in this transition.
The drive for a more sustainable plastic future will require many different approaches. These can be broadly categorised as reduce, reuse and recycle. Whilst it is acknowledged that consumers have a role to play, it is also clear more is required. Consumers can help drive change, but technology and policy, too, will be key pieces of the puzzle.
The legislative situation differs from region to region, and from country to country.
In the U.K., the situation is a bit complicated. Waste processing is dealt with separately by each constituent country of the U.K. (the so-called “devolved governments”), overlaid with U.K.-wide regulation derived from EU Directives. The good news is that all the devolved governments are taking similar steps to reduce plastic waste.
In England, one of the first legislative steps toward reducing single-use plastics was a small charge payable on single-use plastic shopping bags in 2015, a scheme subsequently rolled out in other U.K. countries. This was followed in 2020 with a ban on the sale of plastic straws, stirrers and plastic-stemmed cotton buds in England.
The U.K. government recently passed legislation which will impose a U.K.-wide tax on plastic packaging that contains less than 30% recycled plastic from April 2022. The aim is to increase demand for recycled plastics which in turn stimulates increased levels of recycling and collection of plastic waste.
In November 2021, the long-awaited Environment Bill became law in the U.K. This bill includes a raft of measures aimed at guiding the U.K. to a more circular economy. Some examples include encouraging recycling through deposit return schemes, the use of more reusable materials, and ensuring manufacturers pay the full costs of managing and recycling their packaging waste.
From a consumer perspective, the Environment Bill also sets out plans for more consistent recycling collections between areas of the U.K. and clearer labelling of products with details of their recyclability. The overall aim is to reduce the confusion caused by current recycling systems and enable households to recycle more.
Even before the Environment Bill was passed, U.K. stakeholders in the private sector were taking action to reduce plastic waste. The U.K. Plastics Pact (signed, voluntarily, by parties representing 85% of the plastic packaging industry in the U.K.) sets out a number of targets for 2025, including the elimination of problematic or unnecessary single-use plastic packaging through redesign, innovation or alternative delivery models. Pact members will stimulate innovation and new business models and help build a stronger recycling system in the U.K.
In the EU, the European Green Deal outlines a growth strategy which at its core aims to reduce greenhouse gas emissions and increase sustainability. One of the action groups is the Circular Plastics Alliance, which aims to boost the EU market for recycled plastics to 10 million tonnes by 2025.
In terms of legislation, the EU Single-Use Plastics (SUP) Directive 2019/904 contains a suite of broader restrictions on single-use plastic items within the EU. The directive was transposed into national laws in member states and applies as of 03 July 2021, although many of the measures are to be phased in gradually.
The current legislative efforts are admirable, and it is encouraging to see that broader industry is pushing for more.
However, legislation is necessarily limited in scope and slow in the making. Rather than riding the wave of legislation, nimble and adaptable innovators are playing a crucial role in helping to create new opportunities for sustainability improvements.
There are a number of types of technology that are aiming to improve the sustainability of plastics, including improved and new methods of recycling plastics; new, more sustainable, plastics; and new materials.
Recycling can be broadly categorised as “plastic-to-product” (often called “mechanical” recycling) and “plastic-to-feedstock” (for example, chemical or biological recycling).
Mechanical recycling is the type of recycling commonly used in existing waste processing systems. Mechanical recycling effectively results in downcycling of the plastic to a lower value or lower grade product. In an ideal recycling model, the material that is being recycled is recycled to produce the same product again and again.
Erema has developed new mechanical recycling processes which effectively reduce downcycling. Its patented “Counter Current” technology allows more types of plastic waste to be converted into high-quality pellets ready for industrial reuse as new products, with greater efficiency.
Traditional mechanical recycling often cannot deal with the complex, composite packaging employed in many products such as toothpaste tubes. To address the issue of composite packaging, various innovators are redesigning packaging. In this vein, Colgate Palmolive has launched an all-plastics toothpaste tube which is said to be recyclable via existing HDPE recycling streams.
Chemical recycling refers to a diverse field of recycling and can provide a variety of outputs from conversion of plastics to oils or into their constituent monomers.
One area of innovation in chemical recycling involves the use of heat energy to split chemical bonds, such as pyrolysis (heating in the absence of oxygen). The heat process affects many kinds of chemical bonds, so this approach has the potential to be widely applicable in terms of types of plastics that can be recycled.
Enval’s patented pyrolysis process uses a bed of carbon to absorb microwaves and rapidly pyrolyse plastic waste into a range of hydrocarbons which are condensed into oils. Importantly, the process is compatible with composite packaging – for example, mixed aluminium-plastic packaging can be processed to recover the valuable aluminium since the aluminium is not affected by the temperatures (around 600°C) and can be separated from the gaseous hydrocarbons produced.
Another tricky-to-recycle material, polystyrene, is the focus of efforts by Agilyx and AmSty. They have announced effective results in recycling polystyrene by a pyrolysis process.
Chemical recycling can also be used to break polymers down into their constituent monomers, which has the advantage of allowing the polymer to be rebuilt again.
Arkema, with MMAtwo, has developed a depolymerization process to thermally depolymerise PMMA (polymethylmethacrylate).
A team at the Lawrence Berkeley National Laboratory in California has designed an entirely new type of plastic, PDK (polydiketoenamine), which the inventors claim can be broken down into monomers under acidic conditions and reused, allowing for repeated recycling.
There are also exciting innovations in biotechnology-based recycling methods using microbes or enzymes to break down plastics into their constituent monomers.
Carbios’ recent innovation involves heating the polymer to improve access to the target esters in combination with a modified depolymerase enzyme that can resist denaturing and aggregation. The resulting process is carried out at 75°C with 0.3 wt.% enzyme and is said to yield at least 90% PET depolymerisation in just 10 hours.
Another major focus for innovators has been sourcing more sustainable starting materials for plastic production to replace the fossil fuel-derived starting materials traditionally used.
“Bioplastics” broadly refers to plastic products produced from primarily biological sources such as plants. Currently, the biggest market for bioplastics is “drop-in” bioplastics such as bioPET and bioPE.
Suntory and Anellotech recently announced a 100% bio PET prototype drink bottle. The bio PET is produced from bio-based monoethylene glycol, which is well known and uses Anellotech’s innovative biocatalytic process to convert woodchips into paraxylene. Paraxylene is transformed by oxidation into the other building block of PET, terephthalic acid, which has traditionally been difficult to source in a sustainable manner. Suntory aims to replace all of its drink bottles globally with 100% sustainable PET by 2030.
Entirely new types of plastics are also widely considered to be a key component of reducing dependence on traditional plastics.
A range of such new materials in the form of biodegradable bioplastics are currently available, including starch blends, PBAT (polybutylene adipate terephthalate) and polylactic acid. The biodegradability and increased sustainability of the starting materials means biodegradable bioplastics could have significant green credentials. Some potential issues of these materials are the extent to which they can be biodegraded (or composted) and the origin of their starting materials.
A recent report from the Food and Agriculture Organisation of the United Nations (FAO) recommended the replacement of conventional polymers with biodegradable, bio-based polymers in agricultural settings.
On balance, it seems that biodegradable bioplastics will have a role to play in a more sustainable plastics future.
PBAT accounts for around a quarter of the bioplastics on the market, but one of its constituent parts, terephthalic acid (TPA), is obtained from fossil fuel sources. Biome Bioplastics, working in collaboration with the University of Nottingham, aims to replace the TPA building with pyridinedicarboxylic acid (PDCA) derived from renewable resources.
Also interesting is BASF’s ecovio, a blend of BASF’s Ecoflex (PBAT) and renewable PLA. This material is said to display the same properties as conventional non-biodegradable plastics, is partially manufactured from renewable resources and is fully compostable in both industrial and home compositing settings.
Polymateria aims to adapt “traditional” non-biodegradable plastics into a biodegradable form by mixing calcium carbonate and transition metal additives with polyethylene and polypropylene. The company claims that its mixture leads to the breakdown without the production of microplastics – a key concern with biodegradation.
Another hot area involves the use of carbon capture technology in the manufacture of polymers. Econic Technologies has developed a process for turning waste CO2 gas into polyols, which can then be used to produce polyurethanes. Scientists at Kyoto University have also developed a system for capturing CO2 for use in the production of polyurethane using new metal-organic framework (MOF) comprising zinc ions.
There are, of course, many alternative materials that aim to replace plastics.
Ecovative Design has developed a series of materials employing mycelium, the root structure of mushrooms, including foams (MycoFlexTM) and rigid biocomposites (MycoCompositeTM). Ecovative’s packaging material has a claimed strength-to-weight ratio comparable to many plastic-based products and is fully degradable in 45 to 180 days.
Skipping Rocks Lab has developed food and drink packaging “Notpla” made from seaweed and plants that is designed to be eaten or home compostable. Notpla will biodegrade under home compositing conditions within weeks and is made from seaweed that can grow up to 1m per day, doesn’t need to be watered and doesn’t take up agricultural land.
There are many ways that we can – and are – tackling the problem of providing a more sustainable, circular plastics economy. There is more to be done, particularly in developing policy, practices and the legal framework surrounding the life cycle of plastics. However, it is clear that technology is rapidly being developed to provide more sustainable materials and more recyclable plastics.
This blog was originally published in the January/February 2022 edition of Sustainable Plastics. Read the original article.
Eleanor is a Partner and Patent Attorney at Mewburn Ellis. She is also our Sustainability Champion and is responsible for leading the firm’s environmental strategy and our sustainability collaboration group, ensuring this remains an important focus for the firm. Eleanor is passionate about the role technology can play in a more sustainable future and enjoys working in close partnership to use her expertise to advance the commercial goals of her clients in this important area with a particular focus on sustainable chemical and material inventions.
Email: eleanor.maciver@mewburn.com
Our IP specialists work at all stage of the IP life cycle and provide strategic advice about patent, trade mark and registered designs, as well as any IP-related disputes and legal and commercial requirements.
Our peopleWe have an easily-accessible office in central London, as well as a number of regional offices throughout the UK and an office in Munich, Germany. We’d love to hear from you, so please get in touch.
Get in touch