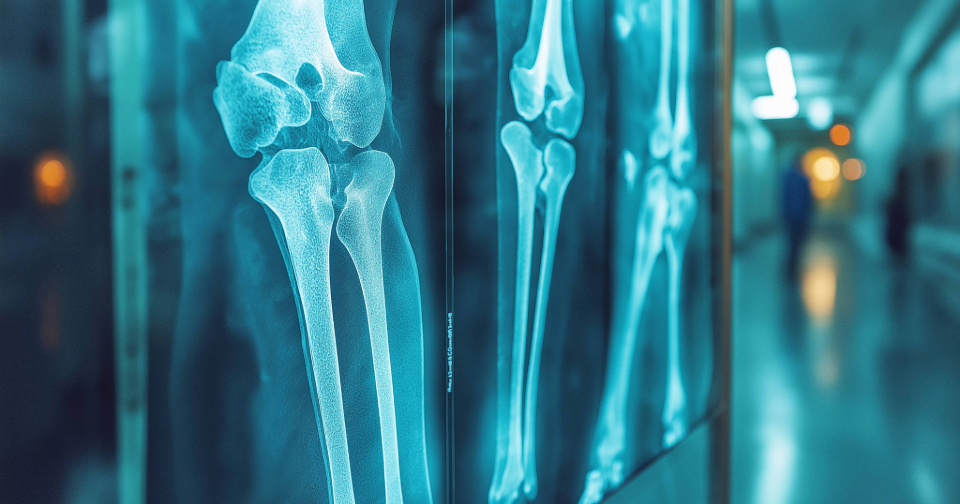
Beneath the surface of the world's oceans lies a vast and essential network of infrastructure that powers modern life.
According to the UK’s Ministry of Defence, it is estimated that 99% of global internet traffic goes through undersea cables, while in 2021 77% of all of the UK’s gas imports came from Norway through pipelines lying under the North Sea. Seabed infrastructure supports everything from streaming a video call to heating homes and fuelling industries. Damage to just a few cables or pipes on the seabed can have far-reaching consequences that can cut off a country from the rest of the world.
It is therefore unsurprising that the seabed is increasingly seen as a strategic frontier which needs to be protected, especially in light of the recent incidents in the Baltic sea, including most notably the rupture of the Nord Stream pipelines in September 2022.
In recognition of this, international bodies are stepping up their efforts to safeguard critical undersea infrastructure. In 2023, NATO established the Critical Undersea Infrastructure Network, holding its first official meeting in May of that year, while the European Commission followed suit by launching an initiative in early 2025 to improve the security and resilience of subsea cables across Europe.
Technological innovation is at the heart of these safeguarding efforts. Autonomous Underwater Vehicles (AUVs) and Remotely Operated Vehicles (ROVs) are now essential tools for the inspection, maintenance, and even defence of undersea infrastructure. These robotic systems provide a means to monitor and service infrastructure without placing human divers at risk, and they can operate continuously in harsh and deep-sea environments.
A recent leap forward in infrastructure inspection comes from Hydromea, a Swiss-based startup which developed the EXRAY wireless ROV.
Thanks to its 6 degrees of freedom and exceptional manoeuvrability, EXRAY is particularly effective in confined spaces where traditional ROVs cannot reach, making it perfect for tank and hull inspections.
A recent application of EXRAY aboard an FPSO (Floating Production Storage and Offloading) vessel’s ballast water tanks showcased its impressive potential. Typically, such inspections require scaffolding, rope access, and human entry into hazardous environments. However, by using the EXRAY system, Air Control Entech, a Scotland-based drone service company, was able to reduce inspection time by 50%, while also eliminating the need for human entry into confined spaces. The ROV delivered real-time HD video to the inspection team and was fully integrated with NAVIA™, Hydromea’s digital automatic data management system, eliminating the need to spend hours following the inspection, sorting out the media, and preparing a manual report.
This approach not only increased safety and efficiency but also significantly reduced vessel downtime and inspection costs.
Another recent advancement in subsea high-resolution mapping is Kraken Robotics' KATFISH™ - a towed vehicle that revolutionizes subsea infrastructure surveys. Designed for deep-water environments, the KATFISH™ vehicle uses advanced sonar technology to capture detailed images and data of the seabed.
KATFISH™ is equipped with high-resolution synthetic aperture sonar (SAS) and is specifically engineered for use in deep-water, challenging environments. The system provides highly detailed 3D imaging and precise measurements, which are crucial for detecting structural damage, monitoring corrosion, and identifying potential risks to subsea infrastructure.
As a high-speed towed vehicle, KATFISH™ operates at speeds up to 10 knots which greatly increases its Area Coverage Rates (ACR) when compared to slower moving ROVs or unstabilized towed sidescan sonar and AUVs. This allows the survey of large areas of seabed at reduced operating time and cost.
While advanced ROVs and AUVs like EXRAY and KATFISH offer exceptional performance in subsea operations, the development of such systems involve substantial cost and complexity. Frontier Robotics, based at the National Robotarium in Edinburgh, offers a compelling alternative: enhancing the capabilities of existing subsea vehicles through advanced, platform-agnostic software.
Frontier Robotics has developed a modular software system designed to be retrofitted onto a wide range of existing ROVs. This allows operators to transform conventional vehicles into autonomous, intelligent systems without the need for costly hardware overhauls. The system integrates advanced stereo camera systems with edge computing and enables real-time 3D mapping for semi- and fully autonomous navigation and seabed inspection.
A core feature of the platform is its use of Simultaneous Localization and Mapping (SLAM), allowing ROVs to generate accurate and comprehensive environmental maps of their surroundings by fusing camera images with ROV sensor data. Combined with on-edge computing, the software enables vehicles to detect and avoid obstacles, maintain precise positioning near complex subsea structures, and conduct high-resolution visual inspections — all without continuous surface control.
This software-driven approach positions Frontier Robotics at the forefront of a shift toward scalable, cost-effective subsea automation — bringing advanced autonomy to the broader market without the burden of new hardware investment.
The oceans may seem distant from everyday life, but the infrastructure that lies beneath them is among the most vital and vulnerable components of modern life.
The technological developments in autonomous underwater vehicles and the fusion of robotics and real-time data processing allow for more effective monitoring and maintenance of subsea infrastructure, offering resilience in the face of underwater threats.
Darena is a qualified UK and European Patent Attorney working as part of our engineering and ICT team. Darena has a Physics background with an MSci degree in Natural Sciences from Durham University. She conducted her Master’s project in the field of condensed matter physics, and researched the magnetic and Hall properties of selected RE:TM alloys and TM multilayers to simulate the performance of MRAM devices made of those materials.
Email: darena.slavova@mewburn.com
Our IP specialists work at all stage of the IP life cycle and provide strategic advice about patent, trade mark and registered designs, as well as any IP-related disputes and legal and commercial requirements.
Our peopleWe have an easily-accessible office in central London, as well as a number of regional offices throughout the UK and an office in Munich, Germany. We’d love to hear from you, so please get in touch.
Get in touch