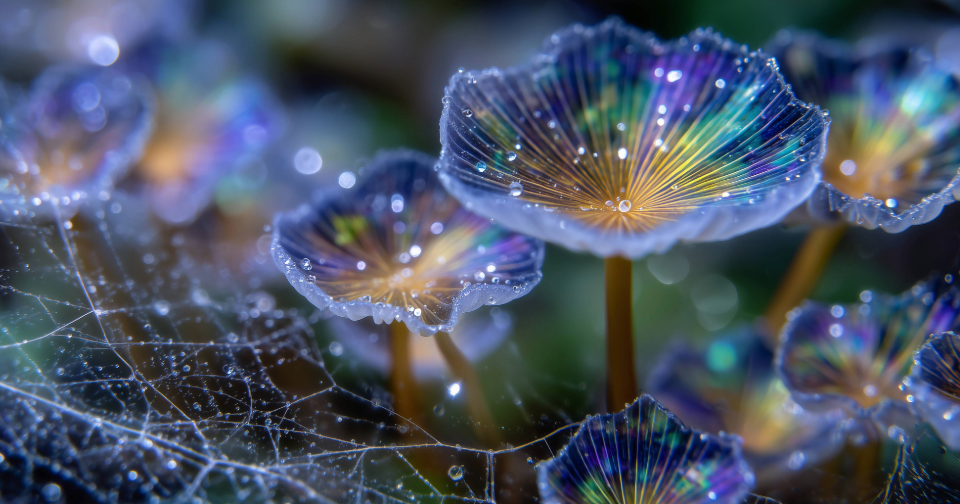
Inspired by muscles and activated by light, this lifelike and autonomous material could have enormous potential. Caitlin Mackesy Davies speaks to Professor Samuel Stupp.
Forward: features are independent pieces written for Mewburn Ellis discussing and celebrating the best of innovation and exploration from the scientific and entrepreneurial worlds.
Researchers at Northwestern University, Illinois, have created a new type of ‘robotic soft matter’ – a material which ‘imitates living creatures’ and which could have important applications in advanced medicine and tackling environmental challenges.
‘Our objective,’ explains Professor Samuel Stupp, who led the experimental studies, ‘was to design materials that could exhibit locomotion in a highly controlled way at a specific speed and that are able to perform simple tasks that we would expect a living creature to do. For example, to pick up an object and transport it to a selected location and release it. Another way to explain it is that these materials have autonomous functions.’
The film-thin material that Stupp and his team have created is made of nanoscale peptide assemblies, which have been linked to polymer networks designed to be chemically responsive to blue light. When the material is exposed to the light, the network shifts from attracting water (hydrophilic) to repelling it (hydrophobic). As water is expelled from it, the material contracts. When the light is turned off, water re-enters the material, which then expands.
This graphic shows how the material bends and crawls when hit with blue light
By precisely managing the way the material is exposed to light, it is possible to control its motion. It can be instructed to bend in different directions or to ‘crawl’ along a particular path. Different stimuli could even be used in the future, such as heat, pH or redox reactions, according to the report in Nature Materials. However, Stupp explains, ‘light is particularly attractive given its non-invasive nature and the possibility to localise the stimulus.’
“By precisely managing the way the material is exposed to light, it is possible to control its motion.”
The speed of the material’s response has been refined with 3D printing, which helps to align the nanoscale fibres that make up the molecular assemblies. Because the response is created when water is expelled from those fibres (or ‘pipes’), the more closely aligned they are, the better the process will work.
The research team was inspired by muscle contractions in the human body, which rely on a similar process. And Stupp, who heads up Northwestern’s Center for Bio-Inspired Energy Science, explains that this work is a reflection of ‘a commitment that I made in my career years ago. I think bio-inspired science is an extremely fruitful direction… [It] is very practical from the standpoint of achieving a deeper understanding of the things around us and also developing highly functional systems that humans can use for their benefit.’
The team believes that the application possibilities are endless, with biomedical applications being particularly important.
The first chemistries the team tackled were hydrogels, which led it to consider underwater uses. For example, Stupp says, robot-like particles of different sizes could be engineered to perform a function in the water-compatible environment of living tissues, perhaps removing a blood clot in a brain or delivering a drug or cells to a specific location. These particles could also be integrated into biosensors, perhaps being activated in order to extract something that needs measuring from the skin.
Alternatively, they could help with cleaning water, which Stupp acknowledges is ‘an important objective in our future’. He can definitely imagine, for example, engineering these materials to pick up pollutants such as toxic metals or to remove microorganisms.
With tweaks to the design, the materials also have the potential to be terrestrial rather than aquatic. And Professor Stupp has other ambitious plans. What’s next, he told Forward, ‘is to be able to develop a “brain” inside these materials’.
‘We have to make this material a lot smarter,’ he continues. ‘That requires more complexity in the structure, but it means it could eventually understand the environment it’s in and decide what needs to be done – for example, whether to shrink or to move, and to react without being directed by external force.’
Professor Stupp hopes that those excited by the team’s findings will be driven to think about the lifelike behaviour they would like to emulate with soft robotics, and then work backwards and design it. ‘The technical community involved in academia and industry is obviously creative,’ he says. ‘So I hope people will be inspired by the paper and maybe even come up with better things than we did.’
Soft robotics offer a fascinating future
Paul Dunne, a partner in the chemistry team at Mewburn Ellis Bristol comments:
"To most people, the word ‘robot’ conjures up visions of intricately machined metal components linked together with a tangle of electronics and hydraulics by clever engineers. However, the efforts of polymer chemists and biotechnologists in the emerging field of ‘soft robotics’ could start to shift this vision towards something far softer, squishier and closer to nature. The material developed by Professor Stupp and his team is a great example of progress in the field, with a hidden high-tech combination of components allowing the production of robots that give the appearance of something closer to man than to machine. It will be fascinating to see the steps these materials take next."
Access the full research in Nature Materials.
Written by Caitlin Mackesy Davies.
Image credit: Mark E. Seniw/Simpson Querrey Institute/Northwestern University
Paul is a Partner and Patent Attorney at Mewburn Ellis. His work is spread broadly across patent preparation, prosecution, and opposition work. Paul regularly handles opposition and appeal hearings at the EPO, where he has an excellent track record of obtaining successful outcomes for clients. He handles the coordination of third party observations against 3rd party patent applications in both Europe and the US. Paul also has particular experience, and a personal and professional interest, in the field of “green” polymer materials.
Email: paul.dunne@mewburn.com
Our IP specialists work at all stage of the IP life cycle and provide strategic advice about patent, trade mark and registered designs, as well as any IP-related disputes and legal and commercial requirements.
Our peopleWe have an easily-accessible office in central London, as well as a number of regional offices throughout the UK and an office in Munich, Germany. We’d love to hear from you, so please get in touch.
Get in touch