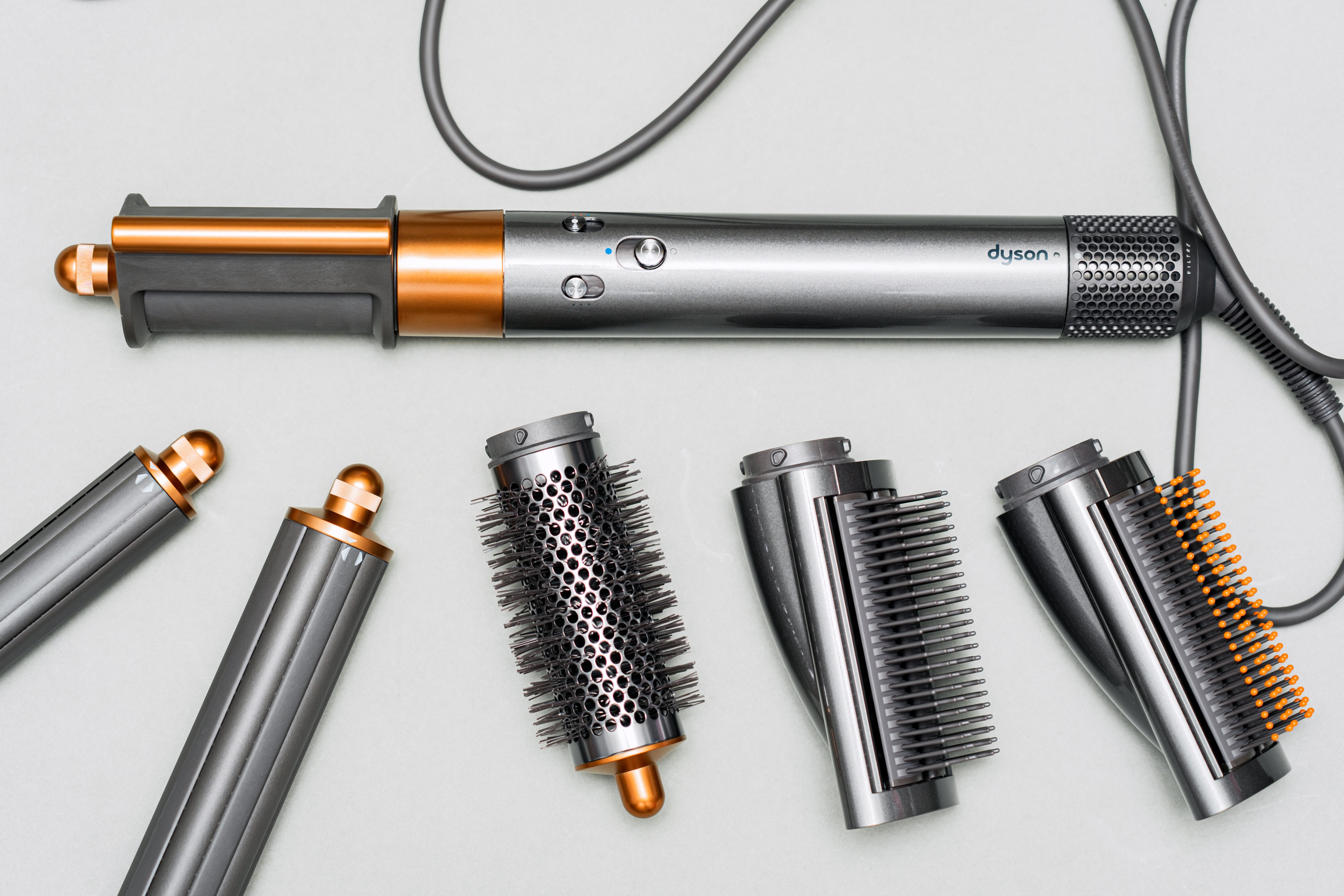
In 2019 the International Energy Agency (IEA) estimated that the energy available worldwide from offshore wind equated to 11 times the world’s expected energy demand in 2040. Even if only a portion of this potential energy is ultimately utilised, offshore wind has potential to make a serious contribution in meeting the world’s energy sustainably.
That potential is reflected in both investment in the offshore wind industry (which is expected to surge over the next decade) and innovation in the field – the number of patent applications filed for offshore wind technologies per year has quadrupled since 2015.
As things stand, most offshore wind installations are in shallow waters close to the shore. That is not, however, where most of the enormous quantities of untapped energy lie. Instead, it is locations far from shore in deeper water (more than 60 m deep) that offer the most potential. Why, then, are wind turbines for the most part not currently being installed in these deeper waters? The big problem lies in how offshore wind turbines are structurally supported. In shallower water, wind turbines can employ a fixed foundation, so as to be rigidly fixed to the seabed by a structure, such as a monopile, gravity-based or jacket foundation. That is not economically feasible in deeper waters, at least partly due to the size and strength of the structure required in such waters.
The solution is to remove the structure altogether by floating a wind turbine rather than rigidly anchoring it to the seabed. Fortunately, the industry is not starting from scratch. For decades, the oil and gas industry has used floating platforms (referred to as floating production systems) where fixed platforms aren’t feasible. Spar-buoys, semi-submersible platforms and tension leg platforms are all examples of technology that has been borrowed from the oil and gas industry.
However, it is not simply a case of mounting a wind turbine to an oil and gas platform. Wind turbines need to be spaced apart, so in practice each turbine needs its own platform – it would be far too expensive to use a platform of the nature used in oil and gas on a per turbine basis. Likewise, it is imperative to the efficient operation of a wind turbine that it is as stable as possible. A wind turbine’s efficiency is highly dependent on it pointing in the right direction.
Fortunately, these problems and others are now being addressed by the wind energy industry.
Stiesdal (along with partners) have, for example, developed an “industrialised” platform referred to as the TetraSpar. The TetraSpar uses interconnected steel tubes forming a tetrahedron-shaped platform, with a triangular keel suspended below the platform for stability. The exciting part of this project is that the platform can be manufactured using low-cost materials by way of industrialised processes at existing facilities and can then be assembled without the need for welding. Mass manufacture like this is critical to the success of floating wind turbines given that a single wind farm can contain well in excess of a hundred wind turbines.
For this reason, Principle Power has designed its platform (the WindFloat) to be used with any existing wind turbine. It does so by ensuring the platform on which the wind turbine is supported is as stable as possible (so that it is, in practice, no different to a fixed platform). To provide this stability, the WindFloat is designed to move fluid (as ballast) to one of three different columns on which the platform floats in response to any rotation of the wind turbine tower. Stability is further improved by providing damping plates (plates with holes in them) fitted at the bottom of each of the three columns.
Stability can also be improved by control of the wind turbine itself. Equinor’s solution involves altering the pitch of the blades of a wind turbine (i.e. how much of each blades faces the wind). Controlling blade pitch is normal, even in onshore applications, to maintain a given rotor speed (for example, to prevent damage when wind speeds exceed a given level). Equinor, however, proposes additionally adjusting blade pitch to dampen movement of the turbine tower resulting from the inherent instability of a floating foundation – essentially using blade pitch to vary the amount of force the wind applies to the turbine in order to counteract movement.
One benefit of preventing such movement is that it reduces stresses on the wind turbine structure. Such stresses are only going to become more of an issue as wind turbines get larger and larger in pursuit of extracting as much energy as possible from a single turbine (GE’s Haliade X, for example, has a tower height of 135 metres). Larger structures necessitate more structural support, which manifests as an increase in weight. This can have a significant impact on the ability to transport and then assemble a wind turbine. The strength issue is exacerbated by the long slender shape of a wind turbine tower, which makes it particularly susceptible to bending in response to any movement. This raises the question of whether the “tower” format of a wind turbine still makes sense on a floating platform, where movement is inevitable.
According to X1 Wind, the answer to this question is that it does not. Instead of a single tower, the X1 Wind platform positions the rotor on top of three-legged support to form a pyramid-like structure, providing a more efficient, lower weight, load-bearing structure. Interestingly, the rotor of the turbine is positioned downwind of the supporting structure, rather than upwind as is the case with a traditional tower). This has two benefits: firstly it allows weathervaning, where the platform self-aligns with the wind direction by floating about a single mooring point; and secondly it means that the wind causes the blades of the turbine to bend away from the structure to avoid “tower strike” – an issue that is becoming increasing problematic as blade length increases.
While self-aligning with the wind is a desirable feature, it is only necessary because wind turbines are so heavily reliant on facing the wind direction. SeaTwirl's design avoids this issue altogether because it is a vertical turbine – the blades spin about a vertical, rather than horizontal, axis of rotation – and a vertical turbine always points in the right direction. Not only does a vertical turbine operate regardless of wind direction, it also has the benefit that particularly heavy components of the turbine (such as the generator) can be positioned at its base, closer to the surface of the sea, so as to provide a more stable arrangement.
SeaTwirl’s design may seem somewhat unconventional but in terms of unconventionality it has nothing on the system proposed by Wind Catching Systems. Rather than a signal rotor per platform, the Windcatcher includes about a hundred (albeit much smaller) turbines arranged in an array on a single floating structure. The rationale is that large single turbines are limited by the speed at which they can safely rotate – an array of smaller turbines which can rotate at faster speeds is better suited to fully utilising the higher wind speeds experienced in offshore locations.
Evidently, there is huge variation in the technology being explored within the field of offshore floating wind turbines. It presently remains unclear which of these technologies is going to take a foothold in the floating wind turbine market. What is clear though, is that offshore floating wind is coming, and it is almost certainly going to transform the wind energy market by providing access to huge, so far untapped, wind resources around the world.
Ben is a Partner and Patent Attorney at Mewburn Ellis. Ben is experienced in patent drafting, prosecution and Freedom to Operate within the mechanical engineering, medical device and consumer products sectors. He also deals with filing and infringement issues relating to registered and unregistered designs.
Email: ben.boyd@mewburn.com
Our IP specialists work at all stage of the IP life cycle and provide strategic advice about patent, trade mark and registered designs, as well as any IP-related disputes and legal and commercial requirements.
Our peopleWe have an easily-accessible office in central London, as well as a number of regional offices throughout the UK and an office in Munich, Germany. We’d love to hear from you, so please get in touch.
Get in touch