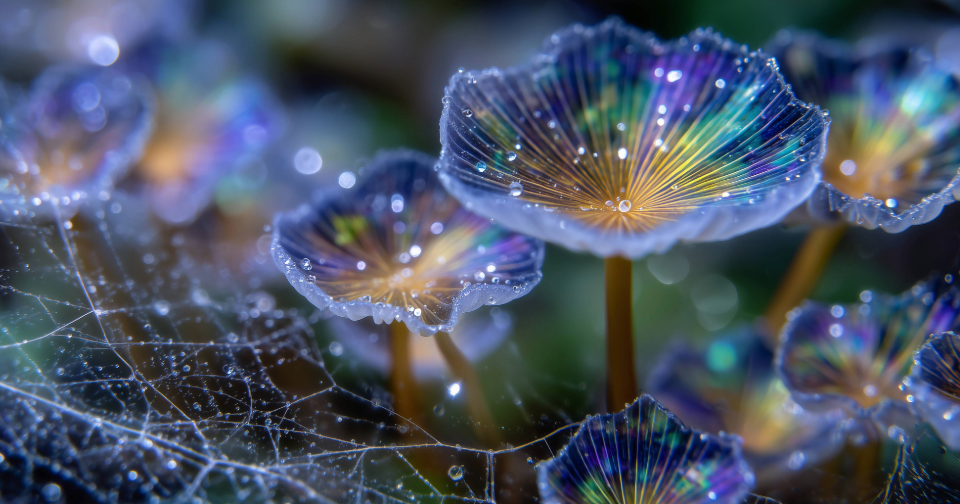
From the start of 2021 up to the date of writing this blog in November, an estimated 37 billion tons of carbon dioxide (CO2) have been emitted into the atmosphere. Alarmingly, that corresponds with over 4.7 tons for every person currently alive on the planet.
In order to reach targets for emission reductions by 2050, global emissions would have to decline by about 60 %. Industrialised countries would have to reduce their greenhouse gas emissions by about 80%.
More than half of the models cited in the Intergovernmental Panel on Climate Change’s Fifth Assessment Report require the use of carbon capture technology, to stay within the goal of 2 °C of warming compared with pre-industrial days. In general, this carbon capture technology aims to take CO2 out of the atmosphere and either store it underground or make it into something else.
One hot area for innovation involves the application of carbon capture technology to the manufacture of a range of polymers.
Using CO2 as a raw material for the production of plastics is the focus of the work of Christoph Gürtler and Walter Leitner at Covestro AG, who were recently nominated for a European inventor award.
Their work focuses on the production of polyurethanes – the aim being to replace components of this plastic with CO2. The process uses a zinc-based catalyst to link CO2 molecules with epoxide molecules to form a chain or polyol (called cardanol). The reaction of interest is shown in their recent patent.
There are three steps to the process described in this patent. In the first step, a bimetallic cyanide catalyst is added to a suspension medium that contains no H-functionalised groups and/or a H-functionalised starter compound. In the second step, a quantity of at least two epoxides is added to the mixture from step (1) along with carbon dioxide. In the final step, an epoxide and CO2 are continuously fed into the reactor, the epoxide in the final step may be the same or different from the epoxides in the second step. At least one of the epoxides in step 2 must have an epoxy functionality of at least 2 and in the event that the H-functionalised started is not introduced in step 1, is must be introduced in step 3.
The CO2 used in this process is derived from emissions from other chemical processes carried out in the Chemical Park in Leverkusen where their pilot scale reactor is situated.
Polyurethane produced from this process is being commercialised under the brand name Cardyon®, and is finding use in a diverse range of applications ranging from mattresses, building materials, textiles, components of detergent and in sports surfaces (e.g. astroturf).
Econic Technologies have also developed a process for turning waste CO2 gas into polyols, which can then be used to produce polyurethanes. According to their recent patent application, Econic’s process is carried out in the presence of a chain transfer agent and a bi-metallic catalyst. Econic claim that, uniquely, their catalysts can be used even under low CO2 pressures, meaning that it might be possible to recapture atmospheric CO2 even after it has been emitted into the atmosphere. They estimate that if 30% of all polyols were made from CO2 then this would be equivalent to planting four million trees.
Scientists at Kyoto University have also developed a system for capturing CO2 for use in the production of polyurethane. Their system consists of a new metal-organic framework (MOF) comprising zinc ions. This MOF has “propeller-like molecular structures”, which are able to rotate and trap CO2 molecules as they approach, effectively acting as a molecular sieve able to recognise CO2 by its shape and size and trap it in the MOF. This material is 10 times more efficient at capturing CO2 than previously developed MOFs and the catalytic efficiency remains high even after multiple reaction cycles. Once captured the CO2 can also be used to make polyurethane materials.
Recently, the polyester poly(glycolic acid) (PGA) has been garnering attention as a readily biodegradable polymer which can have its properties tuned for a variety of applications. Oxford based spin-off OxCCU technologies have developed a method for producing this versatile material from carbon monoxide and hydrogen. Carbon monoxide can be produced from CO2 through electrolysis or via the Boudouard reaction (the reaction of CO2 with carbon).
C4X is a Canadian/Chinese company, which aims to convert CO2 emitted from power stations, flues and exhausts into fuel and useful products. They are particularly focused on eliminating smog in Chinese cities.
Their core technology utilises an alkali solution to absorb and recover low concentrations of CO2 in the atmosphere. The CO2 is then compressed and purified to obtain the liquid form.
This liquified CO2 is then combined with ethylene oxide to produce ethylene carbonate. The ethylene carbonate can be used as a plasticizer in a range of plastics or can be converted into products such as methanol and ethylene.
Novomer have developed a process for the production of lactones from carbon monoxide. Lactones are the building blocks used to produce polylactones, which are biodegradable polymers which are becoming increasingly important in a range of manufacturing and industrial applications, in particular for used in medical applications where their biodegradability is key.
The process employed by Novomer makes use of a cobalt catalyst and a Lewis acid, which activates an epoxide causing it to undergo ring opening, migratory insertion of carbon monoxide then leads to formation of the lactone.
The lactones produced from this process can also be made into a range of other industrially important polymers such as acrylic acid, succinic anhydride, acrylamide and acrylonitrile.
Electrochemical reduction of CO2 can be used to convert CO2 into a range of useful organic feedstocks such as formic acid, carbon monoxide and ethylene. The reduction potentials for CO2 are moderate, making this an exciting area for innovation.
One company working in this area is Twelve which began life as a spin out from Stanford University. They have developed a method of electrochemically converting CO2 into plastics. According to a recent patent this technology is a platform technology which makes use of a new class of CO2-reducing catalysts inside a membrane electrode assembly to convert CO2 into a range of useful chemicals using water and electricity. Oxygen is the only biproduct of this system. These products include formic acid, ethylene and allyl alcohol, which can then be converted into plastics such as polyethylene. These plastics can be used in a variety of applications, such as in the foam component of trainers.
Twelve say that at scale their system is equivalent to having the reducing power of 40,000 trees in a suitcase – that’s a lot!
Another route towards harnessing CO2 to make useful polymers involves utilising biology. Californian company Newlight Technology have focused on exploiting natural processes that occur every day in natural undersea microorganisms to produce chemicals called polyhydroxyalkanoates (PHA). PHA is a type of polyester, which can be used as a replacement for fibre and leather.
The key step for Newlight was finding microorganisms from the sea, which could convert greenhouse gases dissolved in saltwater into PHAs and then scaling this up. According to their recent patent application, this method makes use of methanotrophic microorganisms which have the potential to produce polyhydroxyalkonate, these microorganisms include Methylosinus, Methylocytis, Methylococcus, Methylobacterium and Pseudomonas, which are generally able to use methane or other hydrocarbons as an energy source. As described in that application, CO2 is fed into the medium during cultivation. The PHA can then be recovered from the fermentation system, by centrifuging the medium to obtain a solid pellet of the microorganisms Subsequently, the PHA is extracted from the pellet into a solvent to obtain a PHA-rich solvent and PHA-reduced biomass. After a number of further processing steps, the PHA-rich solvent is separated off and dried to isolate the PHA precipitate as a solid.
This material can then be used in a range of different applications.
Meanwhile back in the UK, the group of Antoine Buchard at the University of Bath have figured out a way to form polycarbonates from CO2 and sugars. These plastics are biodegradable and biocompatible meaning that they can be used in medical settings.
This technology involves using copper, aluminium, zinc or magnesium catalysts to link CO2 into a sugar molecule. Ring opening polymerisation can then be used to produce polycarbonates.
Although CO2 is generally regarded as an unwanted waste product being emitted into our atmosphere in ever increasing quantities and causing the climate to warm, the technologies we have reviewed demonstrate that CO2 can be a useful building block in the production of a range of polymers. Locking CO2 up in polymers not only helps to reduce the carbon footprint of polymer production, but also leads to the production of useful materials.
Green IP Report 2021Our report examines the role of patents in making innovative ‘green’ technologies into a reality as well as how the patent landscape can be used to identify opportunities for partnering, collaboration and investment. |
Thomas is an associate patent attorney with experience in drafting and prosecution of patent applications for a range of European and international clients in the fields of chemistry, biochemistry, pharmaceuticals and materials. He has also worked on FTOs and attended proceedings before the EPO. Thomas holds a Masters (MChem) and doctorate (DPhil) from the University of Oxford in which he specialised in biocatalysis.
Email: thomas.lonsdale@mewburn.com
Our IP specialists work at all stage of the IP life cycle and provide strategic advice about patent, trade mark and registered designs, as well as any IP-related disputes and legal and commercial requirements.
Our peopleWe have an easily-accessible office in central London, as well as a number of regional offices throughout the UK and an office in Munich, Germany. We’d love to hear from you, so please get in touch.
Get in touch