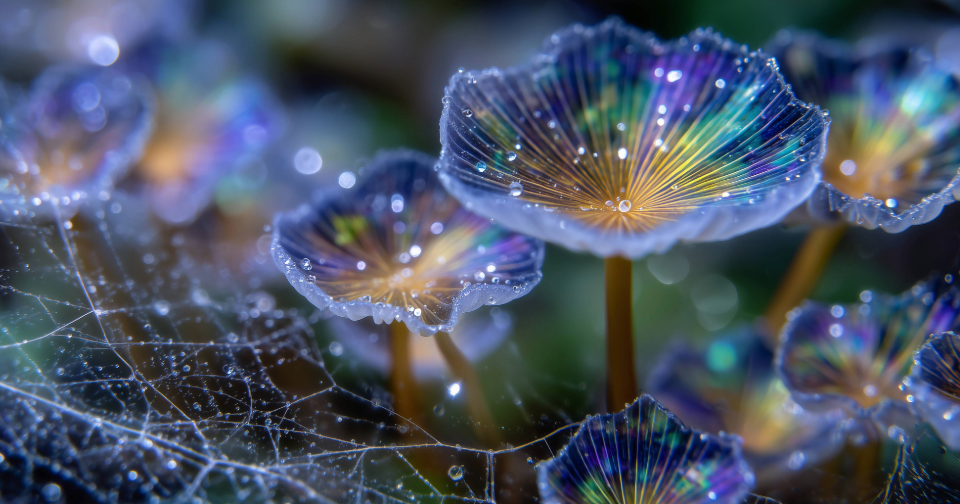
Industry has listened, and learned – plastics are becoming more and more environmentally sustainable.
Traditionally, use of the quintessentially English phrase ‘the three “R”s’ referred to the school-based learning objectives of reading, (w)riting and (a)rithmetic. Today, the phrase is equally relevant to – and perhaps even better for – key strategies associated with addressing the adverse environmental effects of plastics waste: reduce, reuse, recycle.
These strategies are becoming increasingly important, as the world grapples with climate change and global patterns of destructive or wasteful human activity. The recent COP26 Climate Conference (COP26) has highlighted the need for international cooperation in the efforts to look after our planet. But what does this mean in practice?
For the plastics industry, it will almost certainly involve a fourth ”R”: research.
Reducing the amount of plastic consumed by the human populace is a noble goal, but it will require a multi-faceted approach involving many sectors of society. For now, a more attainable target for the plastics industry is to drive efforts into reducing the environmental impact of plastics manufacture.
The international agreement made at COP26, for the first time at any COP, to address global reliance on fossil fuels is expected to incentivise the use of resources other than fossil fuels for many businesses, but particularly for the plastics industry since - according to a 2018 report - plastics production is associated with about 4-8% of the world’s annual oil and gas production.
Many plastics are chemically derived from fossil fuels. This presents a unique challenge: to find commercial solutions for either (i) alternative materials having the excellent and varied properties of plastics, or (ii) alternative sources for the plastics we already have.
Identifying, developing and commercialising materials with properties corresponding to the relevant plastic requires careful consideration of individual requirements. Traditional alternative materials such as glass and card may be used in some circumstances, but often there is a reason that the plastic is preferred. A forward-thinking approach for the plastics industry might therefore envisage the development of new, commercially viable, sources for the current plastics.
Much research is currently focussed on the development of biomass-based plastics - “bioplastics” – as substitutes for conventionally-prepared plastics.
Perhaps because it is the most widely used plastic in the world, polyethylene is a particular focus for development of an “eco-friendly” substitute. Sugarcane-derived ethanol is dehydrated to produce the “I’m Green” alternative marketed by Brazilian company Braskem. A residue of paper pulp production is used to produce naphtha as raw material, by the partnership of Dow and IPM Biofuels.
Some progress has also been made in the development of a “greener” polyethylene terephthalate (PET). Some well-known examples include Coca-Cola’s PlantBottle, and Innocent smoothie bottles. An obstacle for this specific polymer is the difficulty in achieving a commercially viable route to obtaining the terephthalic acid monomer from biomass sources. This means that the commercialised products are generally not 100% bioplastics.
According to a report from the European Patent Office (EPO), much patenting activity has centred around chemically modified natural polymers such as modified cellulose. This may be because cellulose is the most common biopolymer found in nature. For example, academics at the University of Göttingen report that introduction of a cinnamoyl group into cellulose can be used to form a new kind of bioplastic with the advantage that it can be used in a “green” moulding process.
Other approaches to substitute materials include for example the use of fungal fibres by companies such as Ecovative Design, whose technology grows the mycelia to produce a range of materials including plastic substitutes. Another example is the compostable, plastic-type materials developed from plant proteins by the University of Cambridge. These have a silk-like structure which imparts particularly high strength.
Evidently, bioplastics are a valuable approach to avoiding the use of fossil fuels in the manufacture of plastics. The push to reduce reliance on fossil fuels may be further incentivised by increased consumer inclination to make eco-friendly purchasing decisions. We therefore expect that this will continue to be a hot area for technological advance.
According to The SeaCleaners, about 50-60% of our plastic consumption is single-use plastic. It is perhaps not surprising, then, that recent EU legislation attempts to address this issue by banning certain kinds of single-use plastic products. That a legislative approach can be helpful in encouraging reuse of certain plastic items is evidenced by the substantial reduction of over 95% in the use of single-use plastic carrier bags in England following the introduction of a small charge.
Other governmental policies, such as those that make repair comparatively expensive or difficult, do not promote reuse: rather, they encourage consumers to buy new and throw away - rather than repair - the old. The EU is spearheading change in this area, by bringing in new ‘right to repair’ rules that should extend the lifespan of certain products.
Some companies are already facilitating reuse of their products. A straightforward approach is taken by Lego with their Lego Replay system (currently only available in the US and Canada), under which washed Lego bricks are prevented from going into landfill by instead being collected and donated to children’s charities for reuse.
For other kinds of product, more creativity is needed. For example, plastic-based articles such as disposable nappies or traditional sanitary wear face distinctive challenges associated with hygiene and consumer appeal. Nevertheless, efforts are being made to develop re-useable alternatives, such as washable nappies and re-useable sanitary wear, to minimise the influx of these essential items into landfill.
Combined with efforts to reduce the amount of microplastics arising through regular washing of the textile-based items, these could have a drastic effect on the reuse strategy.
In a 2019 report, the EU estimated that the rate of recycling of plastic packaging in the EU increased from 24% to 42% between 2005 and 2017. Accordingly, recycling is generally viewed as a key part of the global community’s strategy to reducing plastic waste.
The UK’s upcoming Plastic Packaging Tax - due to come into force in April 2022 - will, broadly, apply to plastic packaging having less than 30% recycled content. Nevertheless, we expect that innovation and technological development will be key to a successful recycling strategy.
The EPO’s recent study on plastics recycling and alternative plastics reports that Europe and the US each accounted for 30% of patenting activity worldwide in these technological areas between 2010 and 2019. In addition, they found that chemical and biological recycling methods are increasingly favoured areas for innovation, as compared to traditional mechanical recycling methods.
Chemical and biological recycling methods are reported to be advantageous over traditional mechanical recycling in various ways. For example, they minimise much of the time- and cost- inefficient processes of sorting and cleaning often required for mechanical recycling. They also address the problem of downcycling, which is the reduction of quality of plastics following recycling treatment and is commonly associated with traditional mechanical recycling procedures. In contrast to traditional mechanical recycling, chemical and enzymatic degradation processes can break down the polymers into their constituent components, so that a plastic made from chemically recycled plastic can be indistinguishable from a plastic made from fossil fuels. For example, Loop Industries have developed a depolymerisation technology for splitting PET plastic into its monomers. Another company, Carbios, uses an enzymatic process to obtain the monomeric components from PET.
One of the perceived disadvantages of chemical and biological recycling processes - as compared to mechanical recycling - is specificity. Many chemical and biological reactions act on specific chemical bonds and therefore different plastics require different treatments. One exception to this generalisation is pyrolysis, which involves the breakdown of chemical bonds using heat energy. Pyrolysis has been applied to various plastics including polyethylene and polypropylene. Even difficult-to-recycle materials like polystyrene and plastic aluminium laminate composites have been tackled by Agilyx and AmSty, and Enval, respectively.
Another issue to be considered is the environmental impact of the recycling process. For example, it is reported that decomposing plastics often release greenhouse gases such as methane when exposed to UV light. In addition, recycling mechanisms requiring high power input might simply shift the problem. Various of the above chemical and enzymatic strategies minimize such issues.
For many, the above three “R”s are not to be considered in isolation but should be considered together as part of a circular economy. A few routes are available to support this.
The EU uses a life-cycle assessment approach to calculate the environmental impact of a product from start to end – including any reuse and recyclability. The University of Portsmouth launched its Global Plastics Policy Centre at COP26, and it plans to set up an online platform – ready for use by Spring 2022 – to showcase and independently evaluate global plastic policy. Other waste-management strategies at the design level, such as bottle-cap tethering as set out in the EU Single-Use Plastics Directive, will also help contribute to finding a circular pathway.
Evidently, the research into devising a re-useable plastics product made using renewable energy sources and from renewable materials, which is also readily recyclable, is extremely complex. We look forward to the next generation of technological advances.
This blog was originally published in European Plastic Product Manufacturer.
Green IP Report 2021Our report examines the role of patents in making innovative ‘green’ technologies into a reality as well as how the patent landscape can be used to identify opportunities for partnering, collaboration and investment. |
Elizabeth is a member of our chemistry & materials patent team. She handles EP prosecution and opposition work before the EPO. She is experienced in handling worldwide portfolios. Elizabeth has a Masters degree from the University of Oxford (2007). Her PhD research focussed on the organisation of protein biomolecules for the preparation of higher-order inorganic materials and was carried out in the Centre for Organised Matter Chemistry at the University of Bristol.
Email: elizabeth.dale@mewburn.com
Our IP specialists work at all stage of the IP life cycle and provide strategic advice about patent, trade mark and registered designs, as well as any IP-related disputes and legal and commercial requirements.
Our peopleWe have an easily-accessible office in central London, as well as a number of regional offices throughout the UK and an office in Munich, Germany. We’d love to hear from you, so please get in touch.
Get in touch