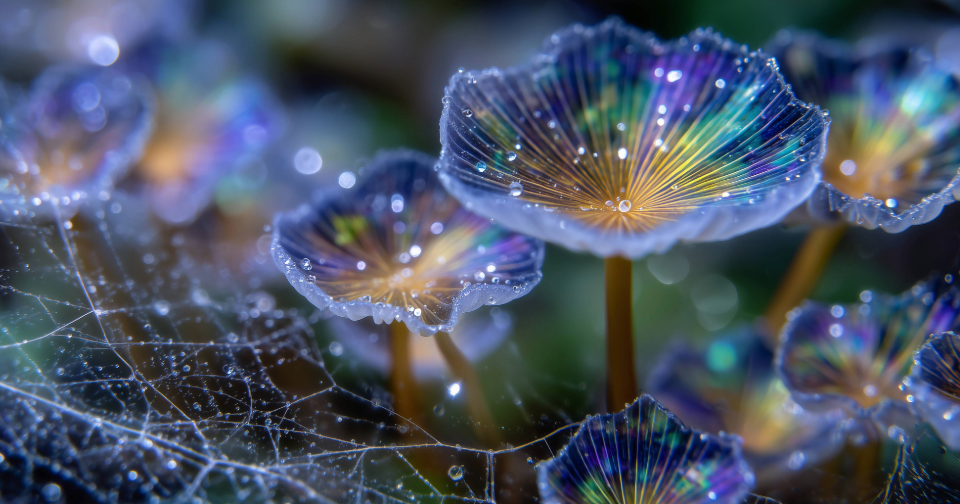
Forward asks Martin Lamb, chairman of pioneering recycler Enval, about the potential of pyrolysis, the challenges of tech commercialisation and how laminate packaging can help close the recycling loop.
Forward: features are independent pieces written for Mewburn Ellis discussing and celebrating the best of innovation and exploration from the scientific and entrepreneurial worlds.
Mewburn Ellis Forward: Can you briefly describe how Enval’s recycling process works? How does it address the problem of plastic waste?
Martin Lamb: We’ve developed a unique solution for recycling low-density, plastic packaging waste even where the plastic is combined with metals and other materials. For example, with our process, we can recycle plastic aluminium laminates by splitting them into reusable aluminium and high-value oil.
Packaging is shredded at the beginning of the process
We do this through a pyrolysis process, which involves the decomposition of organic material by applying heat. It’s microwave-driven, so we use industrial-scale microwaves to heat the plastic in the absence of oxygen on a bed of carbon powder, which is an efficient absorber of microwaves and heats up rapidly. Under these conditions and at temperatures of up to 600°C, the plastic forms a range of hydrocarbons, some of which are gases at room temperature and some of which are liquid, but at the reaction temperature they’re all gases.
Next, we remove the gases from the reactor and cool them down. We condense the liquid ones to create oil, which we are working to supply to petrochemical companies for processing into new plastic. Now that plastic with recycled content is in high demand, this pyrolysis oil with provenance traceable back to waste plastic is a valuable commodity. The remaining gases are used to run the generator that powers the process, so it’s self-sustaining once it’s up to operating temperature.
Pyrolysis oil is a valuable commodity
In the case of flexible packaging that contains metals – we are routinely recycling laminates that incorporate aluminium as a foil, between 5% and 35% aluminium by weight – the metal “floats” on the surface of the carbon bed and eventually falls out under gravity. We separate out that metal and cast it into ingots that can then be reused and recycled infinitely. Typically, an Enval plant running on laminates produces between 200 and 400 tonnes of aluminium a year.
Mewburn Ellis Forward: Why focus on laminate packaging? Where does this waste stream fit into the wider recycling ecosystem?
We started by focusing on plastic aluminium laminates because about 180,000 tonnes of these materials are used in the UK each year, about 10 times that in Europe and about three times the European market worldwide. So you’re talking more than five million tonnes a year worldwide. Of that, around 10% to 12% is aluminium, so that represents a fairly large amount of aluminium that’s going either into landfill or incineration or that isn’t being recovered. And aluminium, of course, is a very carbon-intensive material.
“More than five million tonnes of these target materials are used worldwide each year. That represents a fairly large amount of aluminium that’s going either into landfill or incineration or that isn’t being recovered”
We already recycle a lot of industrial waste, such as the skeleton waste from making milk bottle tops – those little disks that are sealed on under the lid of the milk. Those circles are printed out of rectangular sheets, so if you do the geometry you end up with something like 20% wastage just in cutting those circles out, even if you maximise the number of circles. Yet this material is very high in aluminium content.
Personally, I’ve found getting involved in this a real eye-opener. Take toothpaste tubes: we did some analysis and found that something like three to four billion toothpaste tubes are produced every year and 20% of them go in the bin before they’ve even seen toothpaste – perhaps because they haven’t been printed right or don’t seal properly. And because the material is so cheap and is seen to have so little value, nobody cares; it just goes in the bin.
In fact, if you look at plastics generally, the problematic plastics are the very lightweight ones – known as ‘flexibles’ and including films and carrier bags – which aren’t seen to have any significant value in terms of the reuse or recycling market. Because of this and the ‘war on plastics’ that is being waged in the media we have broadened our focus and, in view of the premium on pyrolysis oils for conversion back into plastic, have turned our attention to all flexibles and not just aluminium-containing laminates.
Mewburn Ellis Forward: How has Enval grown? What challenges have you faced along the way and how have you overcome them?
Martin Lamb: It has been a long and at times painful journey since we started in 2006. Technologically, the main challenges have been around scaling the process up to full commercial scale. For example, the core of the equipment is essentially a very large and powerful microwave oven. Our very first unit was a domestic microwave, and the process included Dr Carlos Ludlow-Palafox, our founder, using tweezers to drop bits of plastic and laminate onto hot carbon. From there, we have been through three scale-up iterations over the years: from an industrial catering oven to a pilot plant that could process 30 to 50 kilos an hour, and now we’re up to 300 to 350 kilos an hour.
As the volume of the unit grew, we struggled with temperature and high power management. We had lots of sleepless nights and made lots of modifications, but luckily we knew where we needed to get to. The key has been the absolute bloody-minded perseverance of our team, who have stuck at the task even in the darkest days. We’ve also had the support of our very patient shareholders and investors, who continued to back us during this period.
The other main challenge has been the industry in which we operate. The waste sector operates on tiny margins, and as a consequence it is focused on large economies of scale. It is also highly conservative and risk-averse. Whereas in other industries an innovation might be explored and potentially embraced early on, when we had our first pilot plant operating we were told to come back when we had a full-scale unit. When we got the full-scale unit running in 2017, we were told to check back when we had five or 10 of them in operation.
“While we initially wanted to be a developer of solutions for the waste industry, we have concluded that the only route to building the sort of business we aspire to be is to build and operate plants”
So, while we initially wanted to be a developer of solutions for the waste industry, we have concluded that the only route to building the sort of business we aspire to be is to do it ourselves, and to build and operate plants. Clearly, this brings with it other challenges – not least the need to secure significant capital in an industry which has historically been viewed less than favourably by the investment community.
Mewburn Ellis Forward: To what extent were you having to create your own market?
That’s exactly the situation we found ourselves in. Frustratingly, our initial target material, plastic and aluminium laminates, were much more significant in quantity (by weight) than coffee cups, drinking straws and so on but were largely being ignored by environmental lobbyists and concerned consumers. This was predominantly because the laminated material is not used in a single form and is less readily identifiable by the public.
On top of this, there was a widely held view that there was no point in trying to recycle lightweight packaging waste and that it should simply be diverted to incineration to generate energy from waste. It was a very hard sell, and although we got lots of interest, nobody really wanted to jump.
Mewburn Ellis Forward: Has that situation changed?
Yes, largely thanks to the Blue Planet II effect, which almost overnight turned plastic packaging into public enemy number one – that ‘war on plastics’ that I mentioned before – and set alarm bells ringing in boardrooms across the petrochemical and plastics industries. Suddenly, the need to get recycled content into plastic packaging triggered widespread interest in chemical recycling. As one of the few players with an established pyrolysis plant, we have seen a sea change in the level of interest in our solution, from within the industry but also among brand owners and the investment community. The market has suddenly caught up with us.
Mewburn Ellis Forward: In what other ways has the recycling environment evolved since you started out?
The wider waste industry has finally cottoned on to the idea that waste needs to be treated locally. As a consequence, there is now a trend towards smaller, local recycling facilities. The closure of China’s borders to low-grade waste material for recycling has probably triggered some of this. This makes a small-scale, modular model like ours more attractive. We’re also starting to see a lot more interest from waste handlers, which tells us that they’re waking up to the idea that they’ve got to do something smarter and adopt new technologies.
However, it is also noticeable that new businesses are the ones developing the essential chemical recycling technologies, with the established players bringing the material capture, collection and segregation to the table. It will be interesting to see how this pans out in the future and what sort of merger and acquisition activity it drives.
Mewburn Ellis Forward: You’ve established a pre-paid mail-back packaging recycling scheme, the Laminates League, which is attracting interest from some major food concerns. Why was this initiative needed?
Martin Lamb: We realised that we needed third-party endorsement of our solution. That meant the brand owners using laminate packaging needed to show that it can genuinely be recycled. We wanted to defend the use of this kind of packaging and give brand owners credibility in terms of backing our technology.
What the public may not realise is that flexible packaging, even before it’s recycled, is actually environmentally superior to cans and plastic bottles. For one thing, it’s lighter, so the costs and environmental impacts involved in its manufacture, storage and transportation are essentially just those required for the product itself. It’s cheap and highly effective, it consumes fewer resources and, if it can’t be recycled, there’s less material to dispose of after the product is consumed. So, if it can be recycled profitably and in an environmentally beneficial fashion, what’s not to like?
We don’t believe that mail-back schemes like this are the long-term solution for recycling, but they are driving awareness of the recyclability of laminates and lightweight packaging. They’re also providing considerable data on the willingness and ability of the public to identify and segregate these packaging materials for recycling, which we hope to use to convince local authorities and waste handlers to engage with us and establish kerbside collection schemes. We also hope that this demand will justify further new Enval plants to treat more material (we’re currently constructing our second unit).
Mewburn Ellis Forward: Ultimately, recycling is a complex problem. What gives you confidence in this project and the potential for chemical recycling to move the needle?
Martin Lamb: Finally, after 15 years, the various factors and stakeholders are becoming aligned. For one thing, there is considerable public appetite for a solution to plastic waste, and governments are trying to react to that. Given the morass of different plastics in the market and that go on to appear in the waste stream, a robust and tolerant recycling technology is essential, and we need to be able to develop new plastic packaging with recycled content. If governments can bring joined-up thinking and we can integrate capture, collection and segregation then chemical recycling like Enval’s fits that bill.
Elizabeth Dale, IP director and patent attorney at Mewburn Ellis comments:
"Intelligent recycling initiatives are undeniably key to reducing waste, especially for challenging materials like plastics. Pyrolysis oil, which can be produced through varied and tailored conditions, has multiple downstream applications and is an area of great innovation. Many companies working in this area are making conscientious efforts to minimise their environmental impact. Future developments are likely to be greatly assisted through collaboration and government-driven initiatives."
Elizabeth is a member of our chemistry & materials patent team. She handles EP prosecution and opposition work before the EPO. She is experienced in handling worldwide portfolios. Elizabeth has a Masters degree from the University of Oxford (2007). Her PhD research focussed on the organisation of protein biomolecules for the preparation of higher-order inorganic materials and was carried out in the Centre for Organised Matter Chemistry at the University of Bristol.
Email: elizabeth.dale@mewburn.com
Our IP specialists work at all stage of the IP life cycle and provide strategic advice about patent, trade mark and registered designs, as well as any IP-related disputes and legal and commercial requirements.
Our peopleWe have an easily-accessible office in central London, as well as a number of regional offices throughout the UK and an office in Munich, Germany. We’d love to hear from you, so please get in touch.
Get in touch