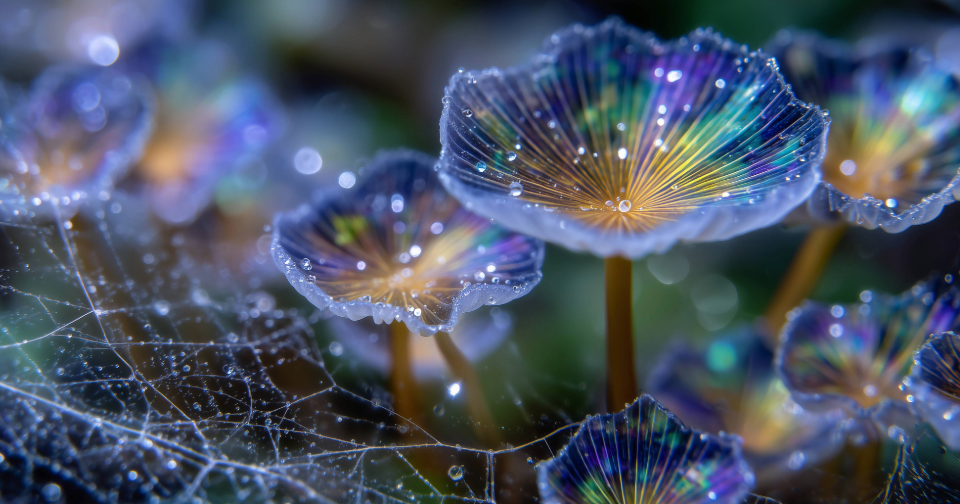
Polymer composites are finding use at an ever-increasing scale in an ever-increasing range of applications, from wind turbine blades to vehicle components and a whole host of things in between.
However, whilst lightweight composite materials can have distinct performance advantages compared to more traditional materials, disposal of these materials at the end of their lifetimes poses particular problems.
This is evident from the fact that an estimated 90% of fibre-reinforced polymer (FRP) composite waste goes to landfill in the United Kingdom (see CiM article Tackling the challenge of composites recycling), compared with around 68% for other plastics (see PlasticsEurope Report).
This problem will only escalate with time. For example, all decommissioned wind turbine blades in the US go to a handful of landfill sites, with an that an estimated 8000 composite-based wind turbine due to be taken down in the US in each of the next four years (see Bloomberg Green feature Wind Turbine Blades Can’t Be Recycled, So They’re Piling Up in Landfills). In the aviation industry, around 12,000 commercial aircraft are due to reach the end of their commercial lives in the next decade (see CiM article Tackling the challenge of composites recycling).
When it comes to recycling, the main focus of the general public and popular press lies with everyday items, such as plastic bottles and straws. Composites seem to attract little attention, in spite of the huge amount of plastic tied up in such materials. However, as society pushes more and more towards a circular economy, awareness of the issue will doubtless grow.
In view of this, there is a huge incentive for chemists to find innovative solutions to deal with the ever increasing amount of plastic composite waste.
Composite materials are made of at least two different constituent components, meaning that they benefit from a combination of the different properties of each of the individual components.
These materials are generally composed of a fibre (for example, carbon fibre or glass fibre) or particulate reinforcement and a matrix phase, which acts like a glue to bind everything together. Additional components (often referred to as fillers) can also be added to enhance the properties of the composite material, such as fire resistance or lightning strike protection.
The matrix component is usually a thermoset polymer such as epoxy, vinyl ester or polyester. Often these thermoset matrix materials are “cured” or hardened using a covalent cross-linking agent to covalently link between the strands of the polymer (see c&en article Chemistry may have solutions to our plastic trash problem).
Recycling these materials is challenging, as not only is it necessary to separate the reinforcement material from the matrix; but, also as the cross-linking reactions are essentially irreversible breaking these bonds to allow the material to be re-melted and re-shaped is not possible. Consequently, these materials cannot be recycled using conventional means of recycling “pure” plastics.
Despite these challenges a number of companies and research groups are working to develop methods of recycling composite materials.
Perhaps the simplest recycling strategy involves taking cured composites, scrap fibre and uncured prepregs (pre-impregnated composite fibres with a polymer matrix material already present), shredding them and combining them with additional matrix materials to produce materials used in less demanding applications such as in construction for the replacement of wood, metal or concrete (see Composites World article Composites recycling — no more excuses). One company active in this area is Global Fiberglass Solutions. Their patent EP2547509B1 describes a method of producing railway ties by shredding and grinding composite turbine blades, adding resin and catalyst if required and curing the combination of resin and ground composite material in a form or mould.
However, such processes necessarily result in “downgrading” of the original material, meaning that it is not possible to reform into the same starting material. To produce recycled composite materials for use in more demanding applications alternative strategies are required.
A pragmatic approach taken by many is to simply burn away the plastic matrix material so as to recover the filler materials, which are generally the most valuable component. This process has been around for many years, but innovators continue to refine the methodology.
For example, ELG Carbon Fibre have developed a process for recovering carbon fibres from waste composite materials by heating the composite in a furnace with controlled oxygen levels (see for example EP 2152487 B1). In 2018 Boeing announced a five-year agreement with ELG to send its composite waste to ELG for carbon fibre recovery (see Composites World article Composites recycling - no more excuses). The carbon fibre recovered can then be used to reinforce new composite materials.
UK company Avon Polymer Products Ltd have developed a patented process for recovering silica filler material from tyres through pyrolysis of the rubber matrix. The inventors found that the recovered silica actually displays improved performance when reincorporated in tyre compositions.
Burning away the plastic matrix is not ideal from a waste and environmental standpoint, which has resulted in innovators exploring alternative matrix materials or cross-linking agents that allow these materials to be recycled more easily.
Some innovators have focussed on adapting conventional thermoset matrix materials in order to make them recyclable at the end of their life.
For example, Adesso Advanced Materials and Connora Composites have focussed their efforts on epoxy systems – one of the most commonly used resins for FRP. Both companies have developed acid-degradable amine-based hardeners (the cross-linking agents which are used to cure the resin system), which allows a thermoset epoxy to be broken apart upon addition of a suitable acid (see, for example, EP 2646410 and EP2986590). A similar strategy has been developed by Jinwen Zhang and coworkers at Washington State University, but instead using anhydride hardeners that can be broken down by an acidic solution in the presence of zinc chloride catalyst (see article in Green Chemistry).
Other approaches rethink the matrix materials entirely, developing new polymers which can be recycled or reused more easily.
For example, Zhang and coworkers at Washington State University have developed a eugenol-derived epoxy vitrimer whose cross-links can be broken down at elevated temperature, allowing remoulding (see article in Macromolecules). The Guan group at the University of California, Irvine have designed a number of recyclable polymeric materials with monomers reversibly linked via boroxine rings (see article in J. Am. Chem. Soc). These materials behave like classical thermoset materials showing good mechanical properties and solvent resistance, but can be broken down in boiling water and re-shaped and reformed.
Perhaps most appealing from an environmental perspective is the idea of developing a polymer matrix that can be easily recycled back to its monomer components, for making into new polymer matrix (see our earlier article “Polymers Unzipped”). Various proposals have been made for such polymers, including polyhexahydrotriazine (explored by IBM, see for example US 9228034), polymers formed from ring opening of the γ-butyrolactone derivative 3,4-T6GBL (see c&en article Strong, stable polymer can be recycled again and again), and self-immolative polymers (see WO 2008/053479). However, the barrier to such materials displacing conventional tried-and-tested matrix materials is high, particularly given the high-levels of performance generally demanded for products incorporating composites.
Finally, another possibility for the future of recycling composite materials could be the use of enzymes, as discussed in an earlier blogpost A Taste for Waste – Plastic Recycling with Enzymes. Enzymes are already able to degrade ester-based polyurethanes (thermosetting polymers). So far these enzymes have only demonstrated relatively moderate rates of catalysis (see ASM Journal Plastics: Environmental and Biotechnological Perspectives on Microbial Degradation), this means further innovation will be required if this is to become a commercially viable alternative.
As the use of plastic composites continues to expand, the societal and commercial pressure for innovators to develop new recycling processes will also grow. Given the diverse nature and uses of plastic composites, a variety of new recycling technologies will be necessary for society to avoid sending such material to landfill.
We explore the EPO report "Patents for tomorrow's plastics" in Intellectual Property Magazine.
Thomas is an associate patent attorney with experience in drafting and prosecution of patent applications for a range of European and international clients in the fields of chemistry, biochemistry, pharmaceuticals and materials. He has also worked on FTOs and attended proceedings before the EPO. Thomas holds a Masters (MChem) and doctorate (DPhil) from the University of Oxford in which he specialised in biocatalysis.
Email: thomas.lonsdale@mewburn.com
Our IP specialists work at all stage of the IP life cycle and provide strategic advice about patent, trade mark and registered designs, as well as any IP-related disputes and legal and commercial requirements.
Our peopleWe have an easily-accessible office in central London, as well as a number of regional offices throughout the UK and an office in Munich, Germany. We’d love to hear from you, so please get in touch.
Get in touch