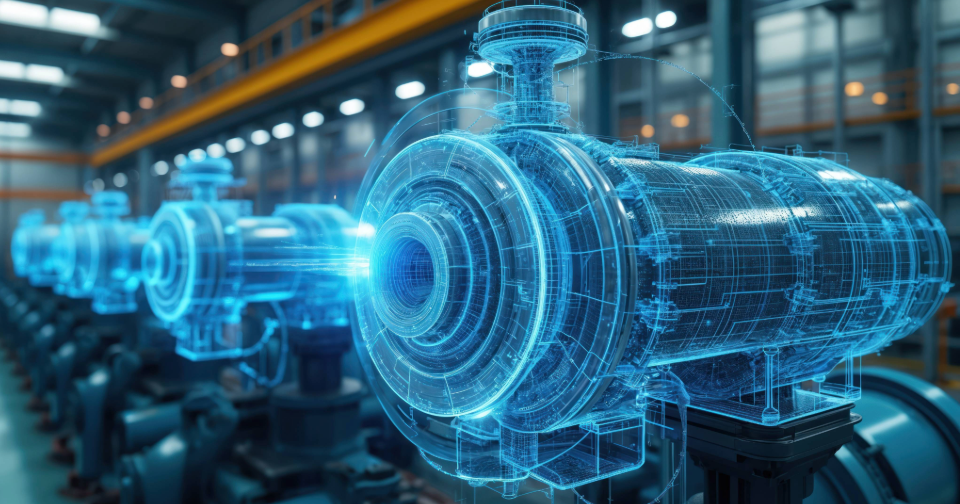
Air conditioning accounts for approximately 10% of all electricity demand worldwide. By 2050 that figure is predicted to increase to 16% (nearly 1/6th of the world’s power usage), largely due to air conditioning system uptake in India and China. India, in particular, is predicted to see a 15-fold increase in air conditioning power consumption. Meeting this increased demand will, of course, require a significant increase in power generation capacity. Where that increased capacity comes from non-renewable sources – in many instances it is likely to do so – there will be an associated impact on the environment.
Other than making use of renewable energy sources, one way to minimise this environmental impact is to reduce the power usage of the billions of cooling systems that will be manufactured, purchased and installed over the coming decades. Below we briefly look at three technologies that aim to do this.
Most cooling systems are based on the vapour compression cycle. The broad idea behind any cooling system is that heat is absorbed from a space that is to be cooled and is then dissipated to an external space. In vapour compression based systems, a fluid (refrigerant) is manipulated via pressure and phase changes so that it is cold when it passes through the cooled space (to absorb heat from the cooled space), and hot when it passes through the external space (to dissipate heat to the external space). Researchers at Saarland University have proposed a somewhat radical approach – manipulating a smart alloy (Nitinol), instead of a refrigerant, to achieve the same absorption and dissipation of heat (see their patent here).
Nitinol is generally known for its ability to be deformed (e.g. bent) into a particular shape and then return to its original shape when heated above a particular temperature. Additionally, however, deformation of Nitinol causes it to increase in temperature, and subsequent relaxation causes it to reduce in temperature. The researchers exploit this property by alternating between deforming and relaxing Nitinol wires to heat and then cool the wires. At the same time, the wires are rotated so that the wires are cold (due to relaxation) when they pass through a space to be cooled, and hot (due to deformation) when they pass through an external space. In this way, like the vapour compression systems described above, this smart alloy system is able to absorb heat from the space to be cooled and subsequently release it to the external space.
Of course, there is no such thing as a free lunch - power is required to rotate and deform the wires. The researchers, however, suggest that this technology is still far more efficient than existing vapour compression cycle systems. Of course, there are a range of factors such as longevity, cost, maintenance, size, etc. that will determine whether the technology will be commercially viable (or whether it will be limited to very specific applications).
As mentioned above, vapour compression systems involve the flow of refrigerant through a vapour compression cycle. Refrigerants have seen significant change over the last 30 years, largely driven by policy. For many years the predominant refrigerant used in cooling systems were CFCs – the same CFCs that were commonly used in aerosol spray cans (for hairspray, deodorant, etc.) and that were largely responsible for the creation of the hole in the ozone layer. The use of CFCs was phased out by the Montreal Protocol, and the successors to CFCs (HCFCs and HFCs) are now also being phased out due to their ozone depletion potential (HCFCs) and global warming potential (HFCs).
One replacement to these synthetic refrigerants is natural refrigerants, such as carbon dioxide, ammonia and hydrocarbons (e.g. propane). These have zero ozone depletion potential (ODP) and low global warming potential (GWP). Natural refrigerants are not new technology – patents for ammonia refrigeration were filed as early as the late 1800s (see US 69955), and ammonia was commonly used in domestic refrigerators in the early 1900s. These systems were, however, subsequently replaced by synthetic alternatives due to safety concerns (ammonia is toxic and flammable). These concerns have not entirely disappeared, but advances in technology mean they are far more manageable in modern day systems, and due to an increased emphasis on environmentally friendly solutions, natural refrigerants have once again become desirable.
Other than the safety concerns, there are other problems to overcome. For example, CO2 has a low supercritical temperature (approximately 31°C), above which it enters a supercritical state that results in significant efficiency losses. This means CO2 is not particularly suited for use as a refrigerant in warmer climates (i.e. the type of climates where cooling is particularly attractive!). However, modern cascade systems mitigate this issue, to an extent, by combining a CO2 cycle with a secondary cycle of another refrigerant (such as ammonia). Instead of cooling a space, the secondary cycle acts to cool the CO2 cycle, so it is as if the CO2 is operating in cooler conditions (i.e. the CO2 does not enter a supercritical state).
In some applications, CO2 cascade systems can provide higher efficiency than systems based on synthetic refrigerants, and with the benefit of low ODP and GWP. As an example, cascade systems are now commonly used for refrigeration in supermarkets, and are finding other niche such as the ice venues at the Beijing 2022 Winter Olympics.
Rather than replace existing cooling systems, one alternative approach is to reduce the work those systems have to do in order to cool a space. Everything on Earth – buildings, people, soil, etc. – radiates heat. In most cases, that heat is absorbed by the surrounding atmosphere, and is radiated back. There is, however, a range of infrared wavelengths (8-13µm) that are not absorbed, and are therefore not radiated back by the atmosphere. In other words, infrared rays within that wavelength range (sometimes referred to as the transparency window) simply pass through the atmosphere and into outer space.
Passive radiative cooling exploits this phenomenon by using materials that radiate heat through the transparency window. This allows those materials to use outer space as a heat sink by continuously radiating heat to outer space where there is no risk of it returning. This property is combined with an ability to reflect sunlight in a highly effective manner, which results in materials that can maintain a temperature of 5°C (and often more) below that of the surrounding environment.
There are a number of ways these materials have been produced, for example: embedding glass spheres in a plastic (polymethylpentene) film with a reflective silver backing; removing lignin from, and compressing, timber to align the cellulose fibres; and forming microscopic pores in a polymer coating. By applying these materials to the envelope of a building (e.g. in the form of paint or panels) the energy requirements for maintaining that building at a particular temperature are significantly reduced.
The relationship between cooling technologies and global warming is, to an extent, a vicious cycle; global warming results in extreme temperatures, which result in a greater need for cooling (and heating), which in turn increases the types of emissions that contribute to global warming. It would be naive to think that the above technologies alone will break this cycle. However, by combining these technologies with more conventional approaches (such as e.g. hybrid VRF systems), and with continued innovation driven by policy, the hope is that we get to a point where the environmental impact of those billions of newly installed cooling systems is largely mitigated.
Ben is a Partner and Patent Attorney at Mewburn Ellis. Ben is experienced in patent drafting, prosecution and Freedom to Operate within the mechanical engineering, medical device and consumer products sectors. He also deals with filing and infringement issues relating to registered and unregistered designs.
Email: ben.boyd@mewburn.com
Our IP specialists work at all stage of the IP life cycle and provide strategic advice about patent, trade mark and registered designs, as well as any IP-related disputes and legal and commercial requirements.
Our peopleWe have an easily-accessible office in central London, as well as a number of regional offices throughout the UK and an office in Munich, Germany. We’d love to hear from you, so please get in touch.
Get in touch