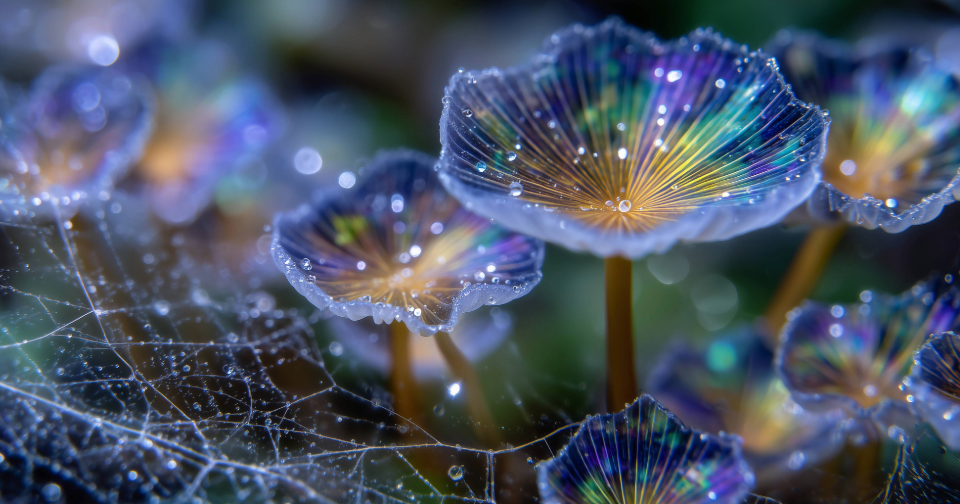
As described in our recent blog article Energy storage: batteries and beyond, lithium-ion batteries are the gold standard for storing energy as they are compact, efficient and powerful enough to run anything from mobile phones to electric vehicles. However, conventional production of this type of battery is expensive, energy intensive and often requires toxic organic solvents.
3D printing refers to the production of a three-dimensional object under computer control in which material is deposited, then joined or solidified, usually in a layer-by-layer manner. Typically, in 3D printing a nozzle moves back and forth to lay down a liquid material, such as a polymer, in a similar way to 2D inkjet printing. Multiple further layers are then deposited onto this 2D layer to gradually build the 3D object.
3D printing has advantages in terms of flexible design and rapid prototyping. In addition, 3D printing can allow products with complex geometries to be manufactured without the need for specialised and expensive tooling equipment, see our recent blog article 3D printing and its layers of legal complexity.
According to a recent EPO study European patent applications for 3D printing increased at an average annual rate of 36% from 2015 to 2018, which is ten times greater than the average yearly growth of all applications at the Office combined in the same period.
With the global demand for batteries expected to increase from 184 GWh in 2018 to over 2600 GWh by 2030 mainly due to electrification of transport, there is a need to develop ways of efficiently producing batteries at low cost.
Recently, Swiss/German company Blackstone Technology have successfully 3D-printed and tested its first working solid-state battery cell. The company is now exploring how to adapt this prototype for mass production, with their first factory for 3D printing batteries having opened in east Germany in November 2020.
Currently, Blackstone’s 3D printing process involves printing each of the different layers of the battery (e.g. anode, cathode, collector and separator) separately and subsequently assembling them into the battery cell. However, the ultimate aim is to be able to print complete batteries, with each of the layers being built up on top of each other. It is envisaged that eventually the battery casing could also be printed as part of this process on a single 3D printer.
Blackstone’s 3D printing process for batteries offers substantial advantages over conventional production methods including the use of more environmentally friendly water-based solvents. The pastes used in each of the printing steps actually contain very little solvent and therefore require much shorter drying times leading to a reduction in the energy required to produce these batteries.
Additionally, the 3D printing method is more flexible and means that the amount of materials which do not store energy in the battery can be reduced by up to 10%. The 3D printing process also allows for a 20% increase in energy density in the battery and is lower cost than conventional battery manufacturing processes. In particular, 3D printing could save up to 70% in terms of initial capital expenditure required to set up the production line for producing the batteries.
Customers can decide what shape the battery should be, which could be useful in applications such as for commercial drones where batteries have to fit into the space within the wings.
The 3D printing process also allows Blackstone to make use of LFP (lithium iron phosphate) as a cathode material. This material is usually considered to have low energy density. However, use of the 3D printing process has significantly improved this.
Blackstone have received investment from the European union to support further research into their process for 3D printing batteries. The eventual aim of this project is to be able to produce enough batteries for 100 Million electric vehicles in Europe.
With the number of electric vehicles sold in the UK expected to increase from 6.6 % of the overall market in 2020 to 64 % by 2030, there is clearly a huge demand for flexible processes for the production of batteries, particularly if those processes can reduce the overall cost and increase storage efficiency. Blackstone’s 3D printed batteries could be a game changer for delivering the huge number of batteries required to power the electric vehicles of the future.
Thomas is an associate patent attorney with experience in drafting and prosecution of patent applications for a range of European and international clients in the fields of chemistry, biochemistry, pharmaceuticals and materials. He has also worked on FTOs and attended proceedings before the EPO. Thomas holds a Masters (MChem) and doctorate (DPhil) from the University of Oxford in which he specialised in biocatalysis.
Email: thomas.lonsdale@mewburn.com
Our IP specialists work at all stage of the IP life cycle and provide strategic advice about patent, trade mark and registered designs, as well as any IP-related disputes and legal and commercial requirements.
Our peopleWe have an easily-accessible office in central London, as well as a number of regional offices throughout the UK and an office in Munich, Germany. We’d love to hear from you, so please get in touch.
Get in touch