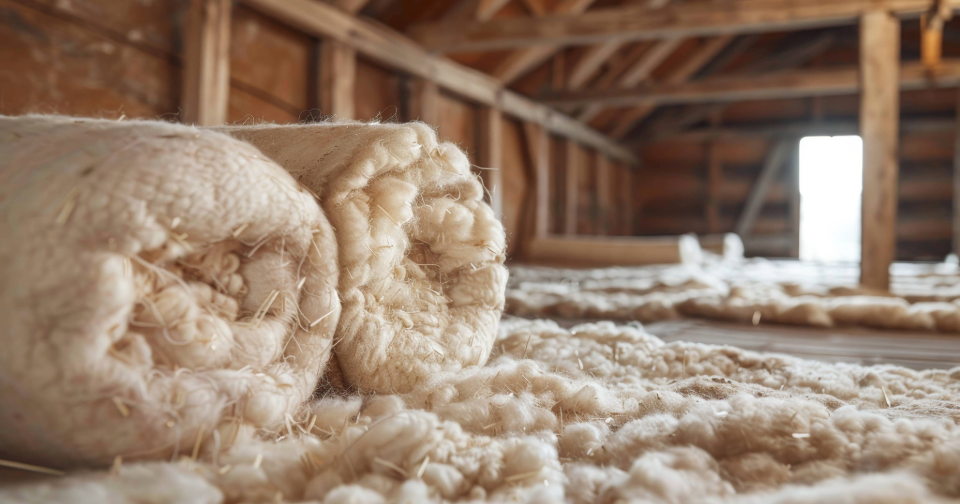
In an earlier blog, we focussed on the chemistry aspects of the Tesla innovations from their Battery Day event on 22 September 2020 that are applicable across the battery sector, but there were more specific announcements that will undoubtedly get the Electric Vehicle (EV) community talking.
First up was the confirmation from the Tesla team that they have developed their own battery manufacturing capability based around a new size of basic cell. The new cells have a larger diameter and length than those currently sourced by Tesla from Panasonic. What may seem like a relatively small increase in absolute size (25mm increase in diameter to 46mm and length up 10mm to 80mm) gives them a surprising fivefold increase in power per cell and also means that for the same number of physical units manufactured they get a large increase in the storage capacity for installation in new EVs.
The new batteries are formed using Tesla’s dry electrode coating technology bought in with their acquisition of Maxwell Technologies in 2019, merged with their innovative tabless cells which remove the standard electrode “tabs” connecting the “swiss roll” cell structure to the battery terminals. The tabless technology, being patented by Tesla, significantly reduces the resistive heating hurdles that are typically associated with increasing cell size, making the 46mm diameter viable and making the battery core much easier to manufacture. The developments in EV cell design apparently give Tesla a 16% range increase on their vehicles and, perhaps more importantly, a 14% decrease in the cost per KWh in battery production.
These new, larger cells also form the basis of what Musk touted as becoming the standard way everyone will embed batteries in vehicles in the future. The Tesla engineers have removed most of the supporting architecture from the existing battery packs and are using the individual cell casings as structural elements to increase the rigidity and shear strength of the units installed in their cars. This allows them not only to do away with some 370 components from their cars but it also reduces weight and size and makes the battery pack a viable structural part of the vehicle.
The overall weight saving is apparently greater than the total weight of the non-cell parts of the battery pack. According to Musk the result is a noticeable improvement in vehicle handling due largely to the weight of the battery pack being lower and concentrated in a smaller region in the middle of the vehicle. The weight reduction also provides a welcome range increase of 14%. The new smaller battery packs are also said to be safer because they can sit hidden away in the centre of the vehicle reducing the chances of damage in an impact.
Musk used an analogy with the historic change from aeroplanes carrying the weight of separate fuel tanks to storage of fuel in the structure of aircraft wings, and made the bold claim that “in the long term, any cars that do not take this architecture will not be competitive”.
Although these announcements come in the context of the Tesla company, their open source IP policy means that the innovations could easily see much wider applicability across the industry on a shorter timescale than usual.
Sam is an accomplished UK and European patent attorney specialising in chemistry and materials science, with a particular interest in battery technology and pharmaceutical chemistry. He has extensive experience and a proven track record of success in securing and defending IP rights for his clients.
Email: sam.bailey@mewburn.com
Our IP specialists work at all stage of the IP life cycle and provide strategic advice about patent, trade mark and registered designs, as well as any IP-related disputes and legal and commercial requirements.
Our peopleWe have an easily-accessible office in central London, as well as a number of regional offices throughout the UK and an office in Munich, Germany. We’d love to hear from you, so please get in touch.
Get in touch