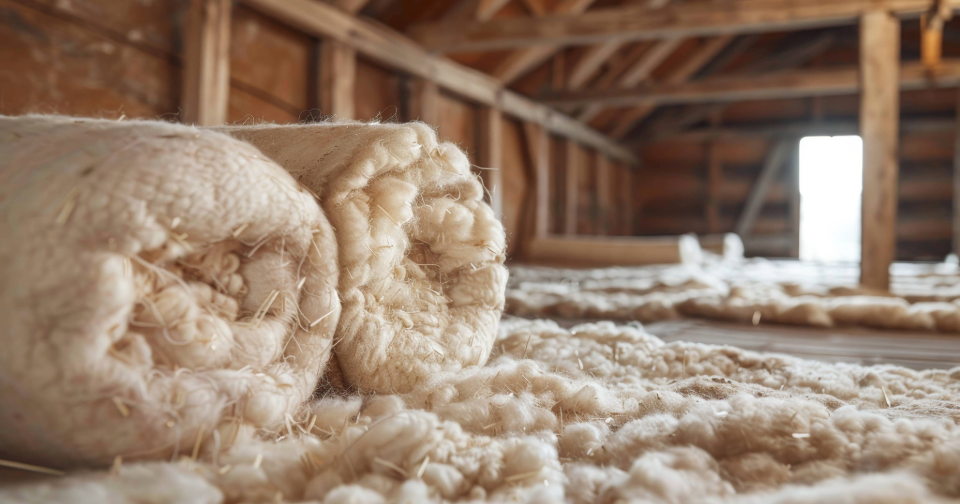
In recent months there has been a rapid increase in publicity and public awareness of sustainability and the effects we have on the environment. A significant amount of the discussion focusses on the unsustainable use of materials such as plastic, in particular its use for food and drinks packaging, and clothing.
The solutions to the issue of sustainability will involve many, complex competing factors. For example in food packaging, plastic is often used to increase the shelf life of a food and can contribute to significant reductions in food waste. In many cases using plastic (compared to a conventional alternative such as glass) also reduces the weight of the product significantly leading to a reduced carbon footprint for transport. Any alternative material or packaging method needs to maintain the advantageous properties of the existing packaging whilst improving the sustainability of the packaging overall. These are high demands for any technology to meet.
Whatever the exact answer, the increase in awareness is driving consumer habits and inspiring innovators to develop technologies that will help address these problems, and lead us towards a “circular economy”.
The “circular economy” is often described as the opposite of the “take, make and waste” model in which materials are taken from a natural resource, made into a product which is used once and then thrown away.
More specifically, the circular economy refers to an industrial model based on the principles of: designing out waste and pollution where possible; keeping products and materials in use where their use is necessary; and regenerating natural systems. It is generally considered that this model is a key way to address the issue of sustainability, particularly for plastics. For example, to facilitate the move to a more circular economy, in December 2015 the EU Commission put forward a first Circular Economy Package.
Discussion of the circular economy distinguishes between technical cycles in which materials are not consumed and are recovered through reuse, repair or recycling (e.g. packaging for food and clothing) and biological cycles in which materials are consumed and designed to feed back in to the system through processes like composting (e.g. food and wood).
The technical cycle in the circular economy will require recycling of at least some products (i.e. those that cannot be reused or repaired or products at the end of their reusable or repairable life). Prominent among the materials that will ultimately require recycling are plastic packaging products which are valuable for their varied properties and other environmental benefits such as the potential to reduce food waste.
Although recycling of materials like plastic has been well known for many years, it is estimated that nearly 79 % of all plastic ever produced has ended up in landfill or the natural environment. Even the plastic that is recycled is often not recycled into the same product and is down‑cycled to other items due to the reduced quality of recycled plastic feedstock compared to new or virgin plastic.
Some of the issues associated with down-cycling arise from use of mixed recycling streams in producing new products such as new polymer resins. Therefore, a growing number of companies are trying to avoid this “down-cycling” by developing their own recycling streams. For example, Rapanui a clothing company and their open platform TeeMill, has designed all of their products to be sent back to them when they are worn out and new products are made from the recovered material in a process designed to be repeated over and over again. Loop Ventures is a company which aims to bring together businesses to develop circular models for their products. One example of Loop’s work is a Unilever partnership with data, logistics and recycling companies to achieve a circular model for laundry detergent amongst other products.
Alongside these bespoke recycling systems, a number of new plastic recycling processes have been developed to improve on existing general purpose plastic recycling. These new approaches include new mechanical recycling processes which improve the quality of recycled plastics, chemical recycling methods and entirely new plastics which are designed for recyclability.
In terms of new mechanical recycling methods, EREMA Group have developed a Counter Current technology which allows more types of plastic waste to be converted into high-quality pellets for industrial reuse as new products, with greater efficiency. The Counter Current technology refers to a process in which waste material enters an extruder and is rotated in the opposing direction to the flow of the extruder screw. More waste material can be processed using this method at faster rates than previously possible and at lower temperatures with improved the quality of the material produced. The inventors of the Counter Current technology, Klaus Feichtinger and Manfred Hackl, won the European Inventor Award in 2019.
Chemical recycling is a term used to refer to recycling processes in which polymers are broken down into their constituent building blocks. Chemical recycling, or transformational technologies, actually refers to a diverse field of recycling and can provide a variety of outputs from conversion of plastics to syngas or tar oil to the conversion of specific plastics to their constituent monomers which can then be re-polymerised for a new use. One important advantage of chemical recycling is that it can be applied to lower-quality, more contaminated mixed loads, which can lead to a reduction in waste. Loop Industries have developed a method for breaking down PET from many sources (including traditionally hard to recycle PET in carpets and marine waste). The PET is broken down by hydrolysis and the monomers obtained are then re-processed into high quality PET that can be used, for example, in food grade packaging. Indeed, many large chemical companies such as BASF and Neste, have recently made moves to incorporate chemical recycling technologies into their manufacturing and supply chains as well as commitments to developing chemical recycling technologies.
New polymers are also being developed with the aim of increasing their chemical recyclability. One such chemically recyclable plastic is PDK (polydiketoenamine) developed by Lawrence Berkeley National Laboratory in California. The inventors indicate that PDK can be broken down into monomers in an acidic solution allowing the plastic to be rebuilt from scratch without any loss of performance, as discussed in Alex Cavell’s recent blog post Plastics recycling: polymers unzipped.
Other innovations aim to tackle the problems associated with existing plastic recycling methods by developing plastic processing machines which can effectively utilise the lower quality recycled plastic feedstock from more traditional recycling methods. For example, Engel have developed a plastic processing machine which automatically adjusts for variations in the recycled plastic feedstock (i.e. variations in melt viscosity) in real-time during processing. This opens the door for recycled plastics to be used in a far broader range of applications.
Alternative materials are another key technology area aiming to address the issue of sustainability particularly in packaging. PDK, discussed above, is an example of an alternative material that sits in the technical cycle of the circular economy as PDK is designed to be recyclable and not compostable. However, many established alternative materials fall within the biological cycle of the circular economy because the materials are biodegradable or compostable (e.g. paper based packaging).
Some of the established alternative materials are not a suitable replacement for all situations, particularly in the case of plastic. Add this to the desire for ever more sustainable replacements and innovation in this area abounds.
Ecovative, founded by Eben Bayer and Gavin McIntyre, have developed a series of materials employing mycelium, the root structure of mushrooms, which can be grown in only 9 days and is fully compostable. The materials range from: textile and cosmetic products made from pure mycelium; packaging materials employing mycelium and a hemp by-product to provide fully compostable packaging; to meat alternatives. The idea behind the materials came from Eben Bayer’s childhood on his family’s farm in Vermont, where he noticed that fungi had glued together piles of wood chips. Fast forward and Ecovative’s packaging material made from mycelium has a claimed strength-to-weight ratio comparable to many plastic-based products, and is fully degradable in 45 to 180 days. Toxicity studies also suggest that the material can enrich the soil. All of the energy for growth of the mycelium packaging comes from the hemp by-product so there is no need for accelerated heating. This means that manufacturing the packaging material also requires between one-fifth and one-eighth of the energy used for foamed plastics.
Skipping Rocks Lab is a London-based start-up developing natural packaging made from seaweed and plants, Notpla, that is designed to be eaten or home compostable. Notpla will biodegrade under home compositing conditions within weeks and is made from seaweed that can grow up to 1m per day, doesn’t need to be watered and doesn’t take up agricultural land. Notpla provides a viable alternatives to standard single-use packaging that is particularly suitable for liquid products such as drinks and some foods, as discussed in Niles Beadman’s recent blogpost Consumable consumables: the edible water bottle. Skipping Rocks are proud, and rightly so, to have contributed to the first 100% plastic free half marathon and provided over 30,000 edible rehydration capsules to the 2019 Virgin Money London Marathon.
It is certain that a large amount of effort is needed to address the issue of sustainability which will involve many different parties. It is clear (and encouraging) that innovators are working hard to develop exciting new technologies to help tackle sustainability and realise a circular economy.
This blog has also been published in Chemistry and Industry.
Eleanor is a Partner and Patent Attorney at Mewburn Ellis. She is also our Sustainability Champion and is responsible for leading the firm’s environmental strategy and our sustainability collaboration group, ensuring this remains an important focus for the firm. Eleanor is passionate about the role technology can play in a more sustainable future and enjoys working in close partnership to use her expertise to advance the commercial goals of her clients in this important area with a particular focus on sustainable chemical and material inventions.
Email: eleanor.maciver@mewburn.com
Our IP specialists work at all stage of the IP life cycle and provide strategic advice about patent, trade mark and registered designs, as well as any IP-related disputes and legal and commercial requirements.
Our peopleWe have an easily-accessible office in central London, as well as a number of regional offices throughout the UK and an office in Munich, Germany. We’d love to hear from you, so please get in touch.
Get in touch