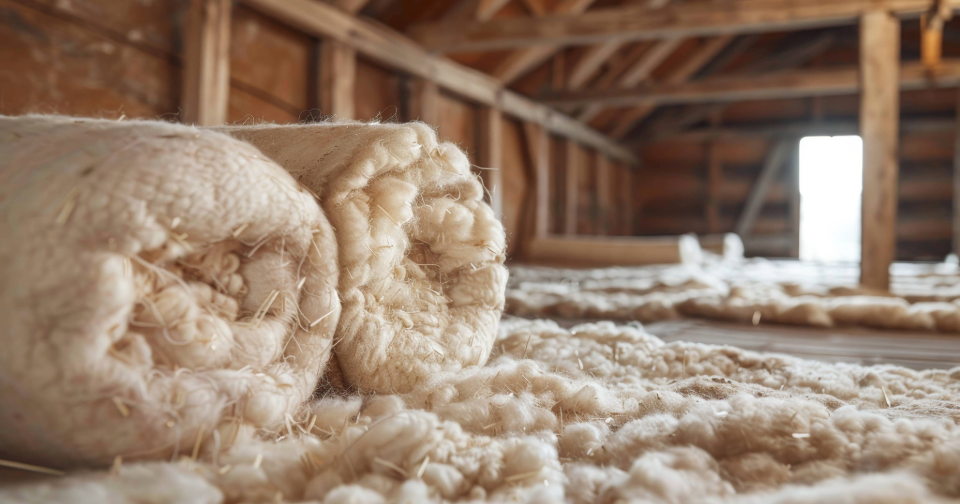
Rubber is a crucial component of the tyre, with most tyres typically containing a complex blend of both natural and synthetic rubber.
Nearly all of the natural rubber produced in the world is harvested from the milky sap (latex) of the “Rubber Tree” (Hevea Brasiliensis). The Rubber Tree is a notoriously picky species that requires specific climatic conditions for growth, to the extent that its cultivation is restricted to tropical regions close to the equator. This is exemplified by the fact that 90% of Rubber Tree plantations are located in South East Asia.
Unarguably, the tyre industry is the biggest consumer of natural rubber, with 70% of all the natural rubber harvested in the world used for tyre production. And this number is set to increase further as global demand for tyres continues to grow.
It follows that the combination of (i) a primary source of natural rubber that is limited to a specific corner of the world and (ii) increasing tyre demand, makes sustainability of sourcing natural rubber a critical issue for tyre manufacturers.
And the issue of sustainability isn’t exclusive to natural rubber. Synthetic rubber, for instance, is typically manufactured from non-renewable petrochemical sources utilising high-energy production processes.
Consequently, many leading tyre manufacturers are seeking innovative new ways to meet the growing demand for natural and synthetic rubber in a green and sustainable manner.
Employing a circular economy is an excellent way of reducing consumption of the rubber raw material to achieve sustainable tyre production (as explored in our earlier blog “Circular tyres: a new challenge for the circular economy”).
And, in line with the old adage “you get out what you put in”, deploying greener, sustainable rubber alternatives at the start of the tyre lifecycle is key to unlocking the green tyres of the future.
Dandelions – infamous for relentlessly invading the pristine lawns of keen gardeners – are often regarded as a nuisance. And yet, this pesky weed is undergoing a transformation from a garden blight to commercial might.
Specifically, the Russian Dandelion (Taraxacum kok-saghyz, or TKS for short) – by virtue of its roots containing natural rubber latex – is finding particular utility as an alternative source of natural rubber for several reasons.
Firstly, TKS is an easy-going plant. It can grow in most climates including temperate regions, such as Northern Europe. This allows tyre manufacturers to grow TKS close to their factories mitigating the lengthy shipping of natural rubber from tropical regions, thereby reducing carbon footprint and avoiding the potential for further rainforest destruction.
Secondly, TKS is very fast growing, only taking about one year to reach maturity. In comparison, the Rubber Tree takes seven years to grow. Consequently, TKS crops are far more adaptable to spikes in rubber demand. And the ability of TKS to grow in poor soil means that it doesn’t compete for land with crops intended for food.
Continental are one of the major players that have tapped the potential of TKS. And – in partnership with The Fraunhofer Institute for Molecular Biology and Applied Ecology, Julius Kuehn-Institute, and EKUSA – they have made significant advances in utilising TKS for tyre production.
For instance, in 2016 Continental unveiled the Taraxagum Conti EcoPlus HD3 prototype, the first truck tyre made from dandelion rubber. And, more recently, the award-winning Taraxagum bicycle tyre is the first tyre made using dandelion rubber to hit the commercial market.
Continental is not alone in their exploration of dandelion rubber. Other leading tyre manufacturers, such as Sumitomo Rubber, have initiated research programmes to investigate the commercial viability of TKS as an alternative natural rubber source.
In a similar vein, a rival to dandelion rubber is “Guayule” – a desert shrub with branches and stems rich in natural rubber latex. Guayule, being hardier and faster growing compared to the Rubber Tree, provides similar advantages as dandelion rubber. And since Guayule is native to the Chihuahuan Desert (a region encompassing Northern Mexico and Southwestern US), it can also tolerate arid regions with very little water. This makes it ideal for growing across large regions of North America.
It’s of no surprise then that Guayule has also caught the eye of the tyre industry. For example, in 2015 Bridgestone produced the first tyre made from guayule-derived natural rubber.
And recently Bridgestone have established a strategic partnership with Versalis, a major producer in polymers and elastomers, to “develop and deploy a comprehensive technology package to commercialize guayule” at Bridgestone’s Biorubber Process Research Center (BPRC) in Mesa, Arizona. This collaboration being conducive to Bridgestone’s vision of using raw materials that are fully renewable and sustainable by 2050.
Advances are also being made in the realms of synthetic rubber production. As explored in our recent blog “Patents driving tyre innovation”, synthetic rubber is an artificial polymer that is built-up from divinyl building blocks such as butadiene and isoprene.
Historically, butadiene and isoprene are obtained by the chemical process of “cracking” petroleum, whereby large hydrocarbon molecules are broken down into smaller, more useful hydrocarbons by the application of high temperatures and pressure. Self-evidently, this approach relies upon a non-renewable source of raw material and is highly energy intensive.
Accordingly, a number of tyre manufacturers have turned their attention to utilising renewable sugar-based feedstocks to produce butadiene and isoprene.
One example, resulting from a collaboration between Goodyear and DuPont Industrial Biosciences, is BioIsoprene™. This patented technology utilises the biosynthetic action of microorganisms feeding on a renewable carbohydrate source (such as sugar beet, corn or wood pulp) to produce isoprene in high purity.
Another example is Michelin’s BioButterfly project. Launched in 2012 this project aims to provide an economically viable alternative to petrochemical-derived butadiene. Namely, by making butadiene from ethanol obtained by the fermentation of renewable carbohydrate-rich biomass (such as beets, corn, straw and woodchips).
Construction of the first industrial scale prototype plant is already underway at Michelin’s site in Bassens, France. Which, when complete, will enable production of between 20-30 tonnes/year of bio-butadiene. And, if successful, industrial implementation of the process (producing 100,000 tonnes/year) will follow.
Ostensibly, the BioButterfly project represents a key component of Michelin’s sustainable mobility strategy as Florent Menegaux, CEO of Michelin states that “By 2050, 80% of raw material used in our tyres will be sustainable. We expect bio-butadiene to represent approximately 20% of this objective”.
Increasing demand for tyres, coupled with a finite amount of conventional raw materials, means that a fully sustainable tyre lifecycle is a crucial element of sustainable mobility.
In response many leading tyre manufacturers are pledging their commitment to sustainable sourcing of raw materials such as rubber. The examples above provide just a glimpse of some of the pioneering innovations that are paving the way towards the green tyres of the future.
Watch this space for more blogs on improving the sustainability of the tyre lifecycle.
Rebecca is a UK & European patent attorney specialising in the chemistry and materials fields. She works at all stages of the patent lifecycle including invention capture, drafting, prosecution, and opposition proceedings. Rebecca is passionate about advancements in green chemistry, in particular green polymer materials. She has written several articles on this topic, reflecting her keen interest in emerging technologies.
Email: rebecca.blundell@mewburn.com
Our IP specialists work at all stage of the IP life cycle and provide strategic advice about patent, trade mark and registered designs, as well as any IP-related disputes and legal and commercial requirements.
Our peopleWe have an easily-accessible office in central London, as well as a number of regional offices throughout the UK and an office in Munich, Germany. We’d love to hear from you, so please get in touch.
Get in touch