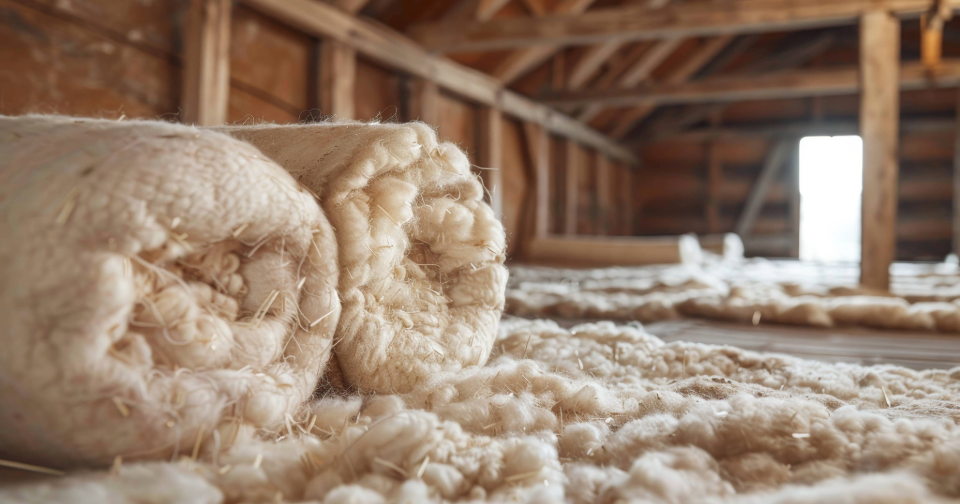
Tyres are huge. Globally over 2.2 billion tyres are produced a year – and this is expected to rise to nearly 2.7 billion by 2022. Since tyres are disposable, this comes with a continuous build-up of used tyres.
In the UK alone, over 400 million kg of used tyres are generated annually. For comparison, at the peak of plastic bag usage the UK only generated 15 % of that weight in plastic bags.
However, where the real difference lies is the propensity for this usage to be reduced. Since the peak in plastic bag usage, the UK has reduced its consumption by over 95% - mainly due to a nominal 5p charge being introduced. However, unlike single use items like plastic bags or coffee cups, tyres cannot be so easily done-without, replaced, or designed around. Although “reusable” tyres do exist (i.e. tyres which can be re-treaded) the physical demands placed on a tyre means that its life span is ultimately capped.
Of course, a reduction in distances driven, and innovations in tyre longevity and construction efficiency, will go some way to reduce the mass of tyre materials used each year - but not on the same scale as is being seen in these other ‘single use’ industries which have traditionally been the focus of the circular economy.
Tyres are sticking around, so they should be a prime candidate for being made circular.
The circular economy aims to break the back of the traditional, linear “take, make, waste” product life cycle, such that we only “take” what we “waste” (as explained in Paul Dunne’s introductory blog "Circular economy: the solution to plastic pollution?").
This is easier said than done, as bridging the gap between the waste product and a useable raw material requires at least some interim processing. Eleanor Maciver’s recent blog "Circular economy: new technologies rise to the challenge" looked at how new technologies are optimising this interim processing step, such that waste from one product can be used to make the same product - a truly circular process. This contrasts to the majority of traditional recycling, where the waste from a high quality product is only suitable for making lower quality products - more of a downward spiral, than a circle.
Tyres are complex, composite products, containing the sum of 175 years of innovation (as explored my recent blog "Patents driving tyre innovation"). Although strides are being made to overcome the challenges associated with recycling composites, some of which are discussed in Thomas Lonsdale's blog "Recycling polymer composites (mixed material complicates)", tyres are still notoriously difficult to recycle.
As a first step the ‘rubber’ components (usually a mix of rubber, carbon black and other additives) need to be separated from the woven metal fibers embedded in the rubber.
The simplest way is by incineration, i.e. literally burning the rubber off the metal. Although this sounds primitive, the heat produced is often used to generate electricity or fire kilns for industry and the metal can still be recycled. Nonetheless, the valuable rubber is lost, and aside from the carbon dioxide released, burning the sulphur in the vulcanised rubber produces acid rain precursors, just like a coal fired power station. Thankfully, like coal fired power stations, this practice is now dwindling.
Nowadays, granulation is the most common type of separation process. Whole tyres are ground up, resulting in a coarse ground rubber which is separable from the un-grindable metal fibers. As before, the metal can be easily reused by melting and recasting, but the rubber, like most polymers, is more challenging to reuse directly due to its vulcanised structure.
The most common use of this ground rubber is in road surfaces, although it also finds its way into cement, tiles, housing and acoustic insulation as a cheap and versatile filler.
For road surfacing, mixing the rubber granules with bitumen produces a more resilient and cheaper “asphalt” material. However, differences in viscosity and density between the bitumen and rubber can lead to separation, as the proportion of rubber in the asphalt composition is increased. Recent research at Iowa State University sought to overcome this, by introducing a trans-isoprene or polybutadiene in a 3:1 ratio with the rubber, to reduce the rubber’s effective density. This allows more rubber to be introduced into the asphalt, thereby improving rutting and cracking resistance, while also reducing the cost of the asphalt by up to 10%.
Nonetheless, moving the tyre rubber from “on the road” to “in the road” is down-cycling (rather than recycling) this valuable material.
As eluded to above, vulcanised rubber is hard to reuse directly. The vulcanisation process, which introduces S-S bridges between the polymer chains, is essential to make tyres hard wearing but in turn makes them impossible to melt down and reform. The key to this, is devulcanisation.
Various methods of devulcanisation are known, including using microwaves, ultrasound, chemical oxidising agents, and biological agents - although the most prevalent method is thermochemical. The latter uses a combination of heat and supercritical CO2 to selectively break apart the inter-polymer S-S and C-S bonds, while retaining the slightly stronger C-C bonds from which the polymer backbone is made. However, if the rubber reaches too high a temperature the C-C bonds can break, resulting in irreversible degradation of the rubber’s quality.
This is particularly problematic in industrial sized batches, where hot and cold spots mean some parts of the batch are degraded due to overheating, while other parts are not fully devulcanised due to underheating. This can be somewhat guarded against by granulising the rubber and using extrusion ovens, where the rubber granules are constantly agitated and drawn through the oven by screw drives, thus distributing the heat evenly.
Supercritical CO2 also has an important role to play. The fluid helps to “stretch”, and thus weaken, the inter-polymer S-S and C-S bonds, but has comparatively little effect on the C-C bonds making up the polymer backbone. Differentiating the S-S and C-C bonds in this way encourages devulcanisation (at even lower temperatures), while keeping degradation of the polymer backbone out of reach.
The resulting devulcanised rubber can then be melted, reformed, and revulcanised as virgin rubber would be, without any discernible drop in quality - a fully circular process.
Nonetheless, the energy cost of this fully circular lifecycle is substantial, as the rubber needs to be heated twice, for de- and re- vulcanisation. This circular lifecycle may therefore be less attractive commercially than the traditional linear lifecycle of virgin rubber, since virgin rubber only needs to be heated once.
However, recent advances in the devulcanisation methods have started to make reuse more commercially attractive. In particular, mechanochemical devulcanisation, which uses a combination of shear stress and tetraethylenepentamine (TEPA) to break the S-S bonds, without the need for heating, is proving increasingly popular.
Moreover, as the shear stress and TEPA can only be applied to the surface of rubber granules, it is only the surface which is devulcanised. Somewhat surprisingly this is actually advantageous, because many applications only need the surface to be devulcanised. This means that the surface layers can be melted and stuck together, to form a new product. It doesn’t matter that the core of the particles are still vulcanised and so cannot be melted, as the surface adhesion is enough to form the new product.
Not only does this avoid heating in the devulcanisation step, but only the surface fraction of the granulated rubber needs to be revulcanised in the new product - thus reducing costs at both ends of the process.
This is only a snapshot of the giant leaps being made throughout the tyre life cycle in order to make tyre production and recycling more circular. Innovation in design and manufacturing, getting a greater depth of understanding of how tyres are used in the real world through smart tyres, and improvements in the sustainable reuse and recycling of tyre materials are all making this goal achievable.
Look out for more blogs on how each stage of the tyre’s life cycle are making the tyres of tomorrow truly circular.
Niles is a Patent Attorney working in the chemistry field. Niles has an MChem degree in chemistry from the University of Oxford. His undergraduate research project was on the synthesis of novel perylene diimide containing macrocycles for anion recognition and sensing applications.
Email: niles.beadman@mewburn.com
Our IP specialists work at all stage of the IP life cycle and provide strategic advice about patent, trade mark and registered designs, as well as any IP-related disputes and legal and commercial requirements.
Our peopleWe have an easily-accessible office in central London, as well as a number of regional offices throughout the UK and an office in Munich, Germany. We’d love to hear from you, so please get in touch.
Get in touch