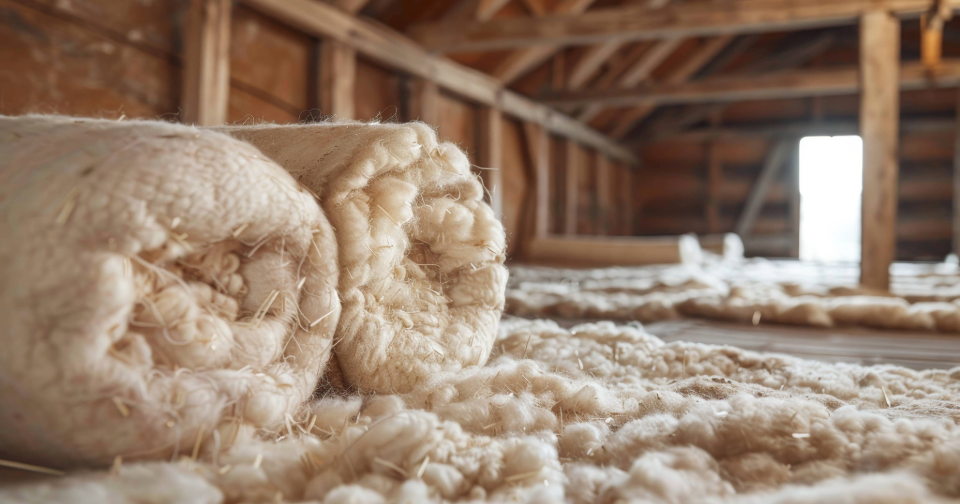
Global demand for clean, renewable energy is now higher than ever before. With climate change becoming ever more important, there has been a concerted worldwide effort to prevent global temperatures from rising more than two degrees this century.
Renewable alternatives to fossil fuels, like solar and wind, are promising but such sources are heavily dependent on the weather. Clearly there is a need for harnessing stored energy when the sun isn’t shining or when the wind isn’t blowing.
Batteries are widely considered to be the most efficient form of energy storage, finding use in electricity grids and being ubiquitous in portable electronics and electric vehicles. In the last few decades, there has been tremendous progress in improving battery technology. Overall attention on its significance perhaps reached its peak in 2019 when “the development of lithium ion batteries” was recognised as being worthy of the Nobel Prize in Chemistry.
While exploring new battery electrode materials continues to be a hot research topic, in this blog we discuss some of the most prominent hurdles facing advanced battery technology, and how Toray Industries, Inc. have provided one such solution in a form of a new separator.
Batteries are multi-component electrochemical systems. Their main components are the cathode, anode, electrolyte, separator and current collector, which must be compatible together for high-performance batteries.
Cathodes generally have a smaller capacity (the ability to store charge) than anodes. There have been relatively fewer successive improvements in the performance of cathode materials than for anodes in the recent decades. For example, lithium cobalt oxide (LiCoO2), the material which kickstarted the energy storage revolution, has a theoretical capacity of 274 mAh/g. Despite its invention by John Goodenough in the 1980s and commercialisation by Sony Corporation in 1991, LiCoO2 remains the dominating cathode material in the batteries of many portable devices to this day.
In contrast, graphite, by far the most commercially used anode material, has a theoretical capacity of 372 mAh/g. While graphite anodes work well, batteries could nevertheless be massively improved with alternative anode materials.
We recently explored silicon as a more advanced anode material (see our blog Increasing battery capacity: going Si high), which allows for a specific capacity around ten times that of graphite. However, pure silicon anodes expand significantly upon absorbing lithium ions during charging. This produces cracks which reduce the energy storage capacity, prompting more research into silicon composite anode materials.
However, no material is as widely believed to be the ultimate anode material as lithium metal (see our blog Batteries for the future: the sky may not be the limit!), which has the highest specific theoretical capacity of 3860 mAh/g and the lowest redox potential (-3.04 V vs. standard hydrogen electrode) of all known anode materials. Whilst capacity plays a key role, the redox potential is also important in quantifying the battery performance: the lower this is for the anode, the higher the voltage becomes for the battery. Unlike silicon, lithium also has negligible issue in volume expansion.
When a lithium metal anode is coupled with a high-capacity cathode material such as the well-known LiCoO2, energy densities of up to 500 Wh/kg may be obtained, which is around double the capacity of conventional Li-ion batteries.
Despite such impressive properties, practical use of lithium anodes has its limitations, the most notable issue being the formation of lithium dendrites during battery charging.
This problem was realised as early as the 1970 when Stanley Whittingham demonstrated the very first battery with lithium metal as the anode. Upon charging the battery, lithium ions from the electrolyte would deposit onto the anode surface. Due to the non-uniformity of the anode surface, lithium ions would prefer to deposit at specific sites. This produces small spiky structures of lithium commonly having branched morphologies, known as dendrites.
Repeated charge/discharge cycles may eventually lead to growth of dendrites that penetrate the separator, resulting in short-circuiting and potentially fire and explosion of the battery. Furthermore, the formation of dendrites reduces the amount of active lithium ions available, leading to degradation of the battery capacity.
Both the safety hazard and the capacity degradation pose serious problems for both academia and industry. Hence, a way to suppress dendrite formation is one of the key challenges to overcome in lithium-metal battery technology.
To tackle these problems, Toray Industries, Inc., a Tokyo-based company specialising in industrial products including battery separator materials, now produce a non-porous separator for use in lithium-metal batteries.
A separator allows lithium ions to permeate through to complete the circuit of the electrochemical cell, whilst also keeping the two electrodes electrically insulated to prevent short circuits. Conventional separators are often made of porous structures such as porous polymeric membranes for permeability. However, porous structures generally have poor mechanical strength and often degrade at high temperatures. This makes it easier for lithium dendrites to penetrate through the porous separator, leading to the aforementioned short-circuiting issue.
Toray’s separator is made of an aramid, an aromatic polyamide exhibiting outstanding heat resistance and mechanical rigidity which is typically employed in aerospace and military applications. It is also worth mentioning that Toray has long been developing aramid-based materials for uses in many thermal resistance and electrical insulation applications, under the commercial trade name ARAWIN. Such properties of the aramid make the separator more mechanically, thermally and chemically stable throughout the operation of the battery.
In addition to exceptional thermal and mechanical properties, the aramid also exhibits tuneable properties for the affinity to lithium ions. Toray is able to adjust the molecular gaps in the polymeric chains such that the aramid material can suppress dendrite growth. This means that the aramid becomes sufficiently non-porous such that any dendrite growth may be stopped as it becomes harder to pierce through the separator. Additionally, its high affinity for lithium ions allows the deposition of dendritic lithium to be more uniformly distributed across the separator film, rather than penetrating through in a concentrated region. High ion conductivity is also maintained to allow for continued transport of lithium ions.
Toray implemented their aramid material as the non-porous separator comprising a pore-free layer onto a microporous separator in lithium metal anode batteries. They demonstrated that short circuiting arising from dendrites was suppressed and more than 80% of the capacity was maintained after 100 charge/discharge cycles.
For consumers of electronics, the lifespan and capacity of a battery are very important factors in deciding on a product purchase. Preventing dendrite formation is therefore paramount when it comes to fulfilling these features and any improvement in doing so is beneficial towards the battery’s performance. With such an implementation of Toray’s aramid-based separator, some of the long-standing problems associated with using lithium metal anodes may finally be solved.
This will no doubt pave the way for many manufacturers of battery separators to develop new materials for more energy-dense and safer batteries. With the need to satisfy the ever-growing demand for electric vehicles and portable electronic devices, it is very possible that lithium-metal battery technology will soon be seen much more in the mainstream commercial world.
Nathan is a patent attorney working in our chemistry team. Nathan has a Masters degree in chemistry (MChem) from the University of Oxford. His undergraduate research project focused on the synthesis of zirconium complexes for polymerisation catalysis. During his undergraduate studies at Oxford, Nathan developed an electrochemical method of surface-initiated polymerisation as part of a summer project. He also completed a short internship studying hydrogen thermal batteries at Stanford University in California, USA.
Email: nathan.zhang@mewburn.com
Our IP specialists work at all stage of the IP life cycle and provide strategic advice about patent, trade mark and registered designs, as well as any IP-related disputes and legal and commercial requirements.
Our peopleWe have an easily-accessible office in central London, as well as a number of regional offices throughout the UK and an office in Munich, Germany. We’d love to hear from you, so please get in touch.
Get in touch