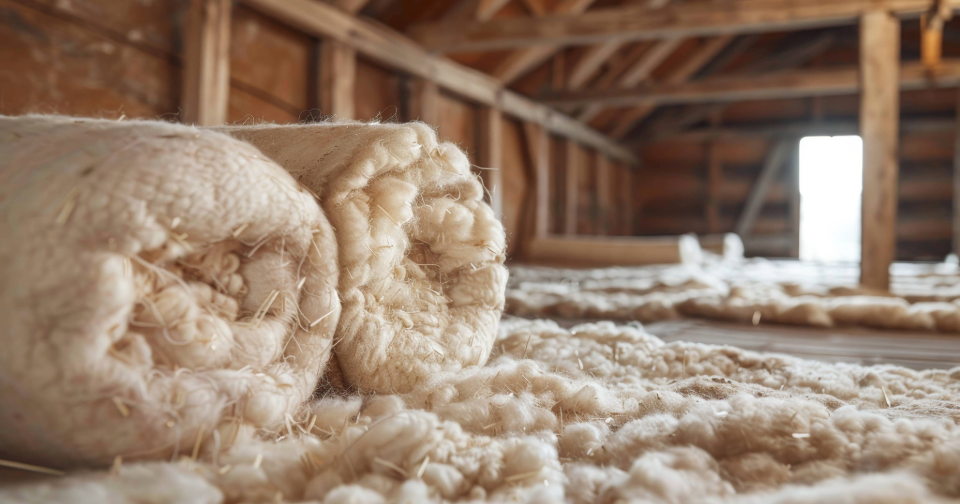
Fibre-reinforced polymer composites are lightweight yet strong materials and are currently a key player in a range of industries including aerospace, automotive and civil engineering.
The idea of combining synthetic polymers with fibres is almost as old as the polymers themselves. For example, in the same year that he developed Bakelite - the first viable synthetic thermoplastic polymer - Leo Baekeland filed a patent to the idea of using the plastic to impregnate natural fibrous materials, such as wood and cotton (see US 949,671, and later patents to paper-based composites such as US 1,160,365 and US 1,233,298). The moulded products which established Bakelite’s position as a household name in the 1920’s incorporated a range of natural fillers.
It did not take long, however, for attention to turn away from natural fibres to new reinforcement materials, with the refinement of glass fibres by Owens-Corning in the 1930’s, and the later development of carbon fibre-reinforced composites. Since then, glass fibre and carbon fibre reinforced materials have become the mainstay of modern composite technology, allowing the production of high performance materials, with exquisitely tuneable properties.
However, the robustness that makes glass fibre and carbon fibre composites so attractive in industrial settings also presents significant challenges for their disposal, as discussed in our earlier blog “Recycling Polymer Composites (Mixed Material Complicates)”. More broadly, there is an increased interest in developing “green” composite materials, with sustainably-sourced materials which can be disposed of in an environmentally-friendly manner after use. As a result, composites in which natural fibres replace the synthetic fibres are the focus of renewed attention, particularly in the automotive industry.
Each year up to 8 million tonnes of waste is generated from end-of-life vehicles in the European Union. To address this issue, the European Commission introduced the end-of-life vehicle directive, with the aim to reduce the environmental impact of the automotive industry. Since 2006 new vehicles in the EU are required to be reusable or recoverable to a minimum of 85%, with this target further increased to 95% in 2015.
In response, the automotive industry has been turning to natural fibre composites. An estimated 30,000 tonnes of natural fibres and a further 30,000 tonnes of wood fibres were used in the 15.7 million passenger cars manufactured in the EU in 2011 (see study).
Applications of natural fibre composites in vehicles have predominantly focused on interior parts such as dashboards, seating and door panels. A range of different plant fibres have been used for a variety of components, with examples including door inner panels made using kenaf fibre composites, seat cushioning made from coconut fibre composites, as well as the use of cotton fibre composites in insulation (see article). In addition to improved recyclability, the replacement of traditional materials with natural fibre composites can reduce weight by up to 30% and be more cost effective.
However applications of natural fibre composite materials is not limited interior components – they are also spreading to other, exterior and structural components. For example, the Mercedes-Benz E-class launched in 2017 incorporates a non-woven natural fibre sunroof frame developed by IAC Group, which is said to be 50% lighter than the conventional steel equivalent (as reported here). On a larger scale, Swiss company Bcomp (discussed in more detail below) have developed natural fibre composite materials currently being used for the bodywork of racing cars.
Plant fibres are seen as a particularly attractive alternative to glass fibres or carbon fibres. A key advantage of using plant fibres is the reduction in carbon emissions during production. For example, the carbon footprint produced in the manufacture of one tonne of natural fibres such as flax or jute is reported to be 50-80% less than that of glass fibres (see article). Furthermore, plants are a sustainable source of fibres as they are rapidly renewable in contrast to petroleum-based carbon fibres.
The increasing interest in plant fibre composites is evident from the growing body of research published on this topic. Composite materials derived from pineapple, bamboo and flax fibres rank amongst the most highly published natural fibre composites in 2017 (see article), and a selection of innovative applications for each of these plant fibres is discussed below.
Bamboo fibres
Bamboo-reinforced polymer composites have hit the mainstream in the past decade, marketed for their “eco-friendly” credentials. Many high street shops offer a range of crockery made from the material, from plates, to cups, to bowls. Indeed, the interest in bamboo-based products as viable alternatives to conventional plastics has led to the appearance of high street shops selling exclusively bamboo products.
Fibres extracted from bamboo exhibit excellent mechanical properties. As the fastest growing woody plant in the world, bamboo is readily available and the fibres are strong whilst having a low density. Composites made from bamboo fibres can be stronger than steel and are much more cost effective. Bamboo fibres are also up to 100 times cheaper than carbon fibre (see article), making their use highly attractive to a range of industries.
As well as the “low-end” applications, such as crockery, discussed above, composites derived from bamboo fibres have been gaining popularity for high-performance applications. Recently, a consortium of companies have joined together to develop new bamboo long-fibre reinforced biobased matrix composites (BAMCO), particularly for applications in the aerospace industry. The project aims to create new sustainable materials for use in aircraft components, including cabin interiors, cover panels and fuselage cladding panels. Bamboo was chosen over other natural fibres in this collaborative effort to reduce the environmental impact of the aerospace industry due to the rapid growth of bamboo plants with low water consumption and low soil usage. The research will focus on identifying species of bamboo suitable for extracting fibres from, the development of bio-sourced polymers, and testing and modelling of the resultant composite materials. Developmental work on this project has launched recently and the first prototypes are scheduled for 2021.
Whilst the bamboo portion of composite materials is generally capable of biodegrading, it is not necessarily the case that the overall composite is fully biodegradable. However, a recent study has shown that the biodegradability of composite materials increases with increasing bamboo fibre content. The composites containing bamboo fibres were also found to be more susceptible to degradation by microbes, suggesting that these new materials may have a smaller long-term environmental impact compared to traditional composites.
Another method for the production of biodegradable composites is to modify the polymer component. For example, ‘bioplastics’ are bio-sourced polymers derived from renewable sources instead of petroleum, which are often biodegradable. In bamboo-polylactic acid composites, biodegradable bamboo fibres are combined with polylactic acid, a bioplastic sourced from corn sugar or sugar beets. A study suggests that the mechanical properties of a bamboo-polylactic acid composite is comparable to fibreglass as well as aluminium alloys. The new composite was also confirmed to be fully biodegradable (see research article), thus opening a new avenue for novel materials that meet performance requirements with a greatly reduced environment impact.
Flax fibres
Flax fibres have traditionally been used in the manufacture of twine, linen and paper. More recently there has been renewed interest in alternative uses of this material. For example, Swiss company Bcomp has developed powerRibs technology which uses flax fibre-reinforced polymers to make high-performance composite materials. Flax fibres have a stiffness that is comparable to glass fibres, but, at only half the density are particularly suitable for making strong, lightweight materials.
The team at Bcomp have recently announced a collaboration with Volvo Cars aiming to replace primary plastics in vehicles with natural fibre composites, which have the additional advantage of reduced weight. In particular, this project is focused on using recycled ocean plastic in combination with the powerRibs technology. As the quality of plastic waste from oceans is often low due to degradation, the reuse of these materials in high-performance applications presents a challenge. Natural fibres therefore provide a necessary boost to the mechanical properties of recycled ocean plastic. In the global crisis of mounting plastic waste in oceans, the upcycling of ocean plastic to make new, lightweight materials is a promising development.
Pineapple leaf fibres
An innovative solution to the vast amounts of waste generated through pineapple cultivation is the use of pineapple leaf fibres in composite materials. It is estimated that 40,000 tonnes of pineapple leaf waste is generated globally each year, the majority of which is either burned or discarded. Fibres extracted from pineapple leaves have high tensile strength and also absorb and maintain colour well, making them suitable for a range of applications.
An example is the development of Piñatex as a pineapple-based alternative to leather by UK company Ananas Anam. This composite is made from fibres extracted from pineapple leaves, which are dried and purified and then combined with polylactic acid, after which a resin top coat is applied (see EP 2576881). Although the Piñatex material is not fully biodegradable, the innovative use of waste material as well as a bioplastic from renewable sources offers a more sustainable alternative to other leather replacements which rely heavily on petroleum. In the era of fast fashion, brands are increasingly looking for sustainable alternatives. A number of these brands are now using Piñatex material in their designs including Hugo Boss and H&M, in a move towards more sustainable fashion.
The potential for technical, commercial and environmental innovation in the field of natural fibre composites is huge. Renewed interest in the area is seeing a range of exciting new developments, which it is hoped will infiltrate into more widespread use. It will be fascinating to see how far these materials can be pushed in the future.
Jane is a patent attorney in our chemistry team. She has a MSci degree in Natural Sciences and a PhD in Chemical Biology from the University of Cambridge. Her doctoral research focused on developing novel methods to detect sites of DNA damage by next-generation sequencing. She joined Mewburn Ellis in 2019.
Email: jane.liu@mewburn.com
Our IP specialists work at all stage of the IP life cycle and provide strategic advice about patent, trade mark and registered designs, as well as any IP-related disputes and legal and commercial requirements.
Our peopleWe have an easily-accessible office in central London, as well as a number of regional offices throughout the UK and an office in Munich, Germany. We’d love to hear from you, so please get in touch.
Get in touch