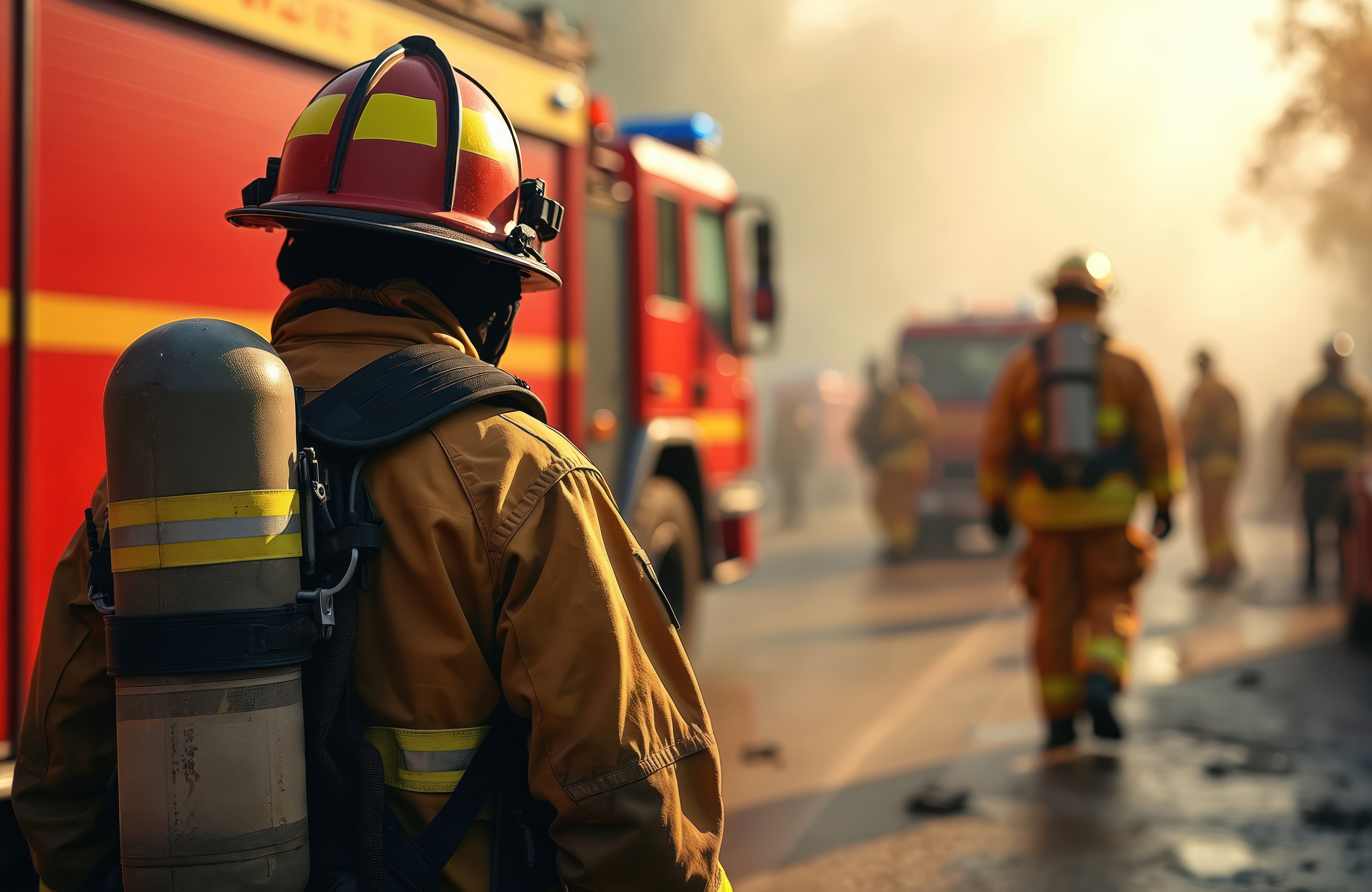
For years, we have been aware of the need to reduce our reliance on plastic. But there is a reason plastic is so ubiquitous in modern life. It is cheap, with tried and tested properties, and it has a huge variety of effective uses. For instance, plastic keeps food and drinks fresh during long transportation and on shop shelves. This is why plastic is so useful in packaging and why packaging is one of the most important areas to improve our sustainability by looking at plastic alternatives. In fact, the industry of “green packaging” alternatives is predicted to be worth between USD 353.2 billion to USD 451.7 billion by 2028.
Two main problems arise with the overuse of plastics. First, the use of unrenewable sources of crude oil and gas in plastic production, and second, the pervasiveness of plastic waste in the environment once it has been discarded.
Wood is a much more sustainable and renewable source of material than oil and gas, as trees can be replanted and used to capture carbon dioxide. Furthermore, wood products, such as paper are easily biodegradable and recyclable.
In view of these advantages, there has been a huge increase in its use in both e-commerce and on the shelves of the supermarkets. Part of this has been stimulated by government policy, such as the UK’s recently introduced plastic packaging tax. But the conscientious consumer is also making their preferences known, preferring brands that make an effort to reduce plastic packaging.
One of the reasons plastics are so ubiquitous is that it can be moulded into any shape for seemingly infinite different uses. Finding sustainable replacements which can be shaped in the same way whilst still being robust enough for utility is challenging.
However, new ways of cutting and folding classic paper and cardboard can replace some common plastics. For example, specially perforated paper results in a honeycomb textured sheet when stretched which acts as a replacement for bubble wrap or packing peanuts to protect fragile contents. A thoughtfully designed cardboard product holds cans, replacing the plastic rings which are notorious for causing harm in the environment. Cardboard can even provide child proof packaging, for instance for laundry detergent boxes. This new cardboard packaging provides all the functionality of plastic but is lightweight for transportation and, importantly, 100% recyclable.
However, replacing plastic in packaging with cardboard is not always straightforward. Finding a more sustainable material which can keep produce fresh and is moisture resistant is difficult.
Unilever recently announced that plastic ice cream packaging will be replaced with paper tubs. The tubs and lids should be recyclable, although they do contain a thin plastic lining which is necessary for freshness.
Wood-based fibre bottles are poised to enter the global market. Both Pulpex, and Pabaco have created usable prototypes which are currently being tested for use with laundry detergent, sauces, soft drinks, and beer. However, Pabaco’s bottles use a thin plastic lining. Although the bottle reduces plastic usage by 65%, this obviously means the plastic must be separated from the paper before recycling. Further work is focussing on a bottle with a paper cap to reduce the amount of plastic even further. Pulpex’s bottle uses a specialised coating to provide liquid stability, which they say does not affect biodegradation or recyclability.
Although paper/cardboard straws and cups are common, consumers are often put off by the lack of liquid stability resulting in soggy, unusable products. A recent study found that paper straws absorbed enough liquid to compromise the strength of the straw within 30 minutes of use.
Therefore, rather than trying to replace plastic with a more sustainable material, such as cardboard, in some areas a more realistic option may be to create more sustainable materials, including more sustainable plastics.
One such new material has been developed by Sulapac who, in collaboration with Stora Enso, have developed a new straw using wood and plant-based binders. This straw does not become soggy and is industrially compostable. Sulapac’s other wood-based materials can be used for packaging in the cosmetics and food industries.
Wood provides a number of components which might be used to make new materials. For instance, a team at Yale have developed a new processing method to make plastic from lignin and cellulose in wood. The process uses wood powder, a waste product from lumber mills, and the resulting material has high strength and stability when holding liquids. The authors of this work hope the material will be useful in packaging, as the resulting plastic can be moulded into a film. Importantly, the material completely degrades after 3 months buried in soil, or alternatively can be recycled.
New research from the École Polytechnique Fédérale de Lausanne (EPFL) takes lignocellulosic sugars, obtained from birch wood, and processes them into useable plastic precursors for materials with high tensile strength. These plastics can be chemically recycled back into sugars and likely biodegrade into the same sugars (biodegradation testing is ongoing). As this material acts as a good barrier to oxygen, it is a promising candidate for more sustainable food packaging.
An attractive source or plastic precursors is waste products from large industries. Tall oil is produced as result of pulp and paper production, and can be used to create “renewable naphtha” which in turn is used for production of plastics. These plastics are chemically identical to plastics which can be produced form fossil fuels and therefore have all the characteristics and functionalities of known plastics. Elopak already uses tall oil in the production of a 100% renewable carton, which enables use of renewable sources whilst maintaining the required liquid stability for the product.
Many of these recent innovations require the components from wood to be isolated cleanly in a reliable process. Ideally, this process is sustainable to achieve packaging that is truly as environmentally friendly as possible. In the UK, Bio-Sep have developed a process that breaks down woody biomass (such as sawdust) using a low energy, ultrasonic process. This process uses lower temperatures than conventional techniques, no corrosive chemicals and organic solvents which can be recovered and re-used. The result is isolation of pure, low molecular weight lignin, as well as cellulose, and sugars, with 95% product efficiency. One issue with current lignin isolation methods is the presence of sulfur which alters the physical and chemical properties of the lignin. Lignin produced from Bio-Sep’s ultrasonic method is of a low molecular weight and sulfur free which means that it is water insoluble whilst being highly soluble in other solvents such as ethanol. This unlocks an exciting new range of potential uses for lignin. Bio-Sep are exploring these uses, such as films and coatings in packaging, in collaboration with various companies and research groups.
Future of Packaging
There are many wood-based packaging products currently in development. Many new innovations are already available for us to cut back on plastic use. Others are just beginning to be tested in the marketplace, and a few are at early stages of research. New processing methods enable the extraction of better, more chemically useful materials from wood in cleaner processes, leading to more products which are more sustainable from the very beginning of production. Time will tell whether these new products stand up to commercialisation, but the research behind them is very promising and shows a willingness throughout the industry to improve our packaging sustainability.
Alison is a patent attorney working in our chemistry team. Alison has an MChem from the University of St Andrews with an industrial placement year at GSK, Stevenage. Her DPhil is from the University of Oxford, focussing on developing new methods of synthesising asymmetric molecules with axial chirality.
Email: alison.fugard@mewburn.com
Our IP specialists work at all stage of the IP life cycle and provide strategic advice about patent, trade mark and registered designs, as well as any IP-related disputes and legal and commercial requirements.
Our peopleWe have an easily-accessible office in central London, as well as a number of regional offices throughout the UK and an office in Munich, Germany. We’d love to hear from you, so please get in touch.
Get in touch