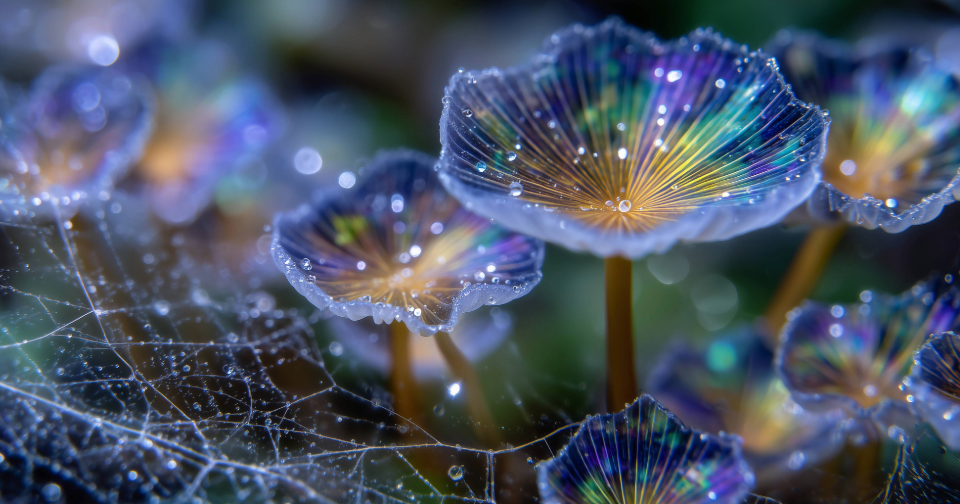
Storage of electrical energy is now an essential part of our lives. Charging and discharging batteries in phones, laptops, toothbrushes, and increasingly cars and bikes is commonplace for the majority of the world’s population. Even the trains and ships we use to move goods and people around the world are turning to batteries in a bid to reduce their carbon footprint.
With us more reliant on batteries than ever, improving their efficiency is becoming a necessary and increasingly valuable area for research.
Currently, lithium-ion batteries offer an unmatched combination of energy efficiency and power density, making them the go-to for portable applications. However, while lithium-ion batteries might be common, their ubiquity does not mean that there is no space for innovation.
For example, Callum McGuinn's recent blog "Lithium-ion batteries - powering the EVs of the future" explored the potential of new cathode and anode materials to store more energy and increase the discharge efficiency of lithium-ion batteries. The cathode and anode are ‘boxes’, joined by an electrolyte. Charged ions move between the cathode and anode via the electrolyte to charge and discharge the battery. Callum explains, “[a]s a helpful analogy, imagine a small box (a cathode) at the bottom of a hill, crammed with tennis balls (lithium ions). To charge the battery, you take the balls out of the box and roll them up the hill into a second, larger box (an anode). Once all the balls are in the upper box, you can release them to roll down the hill, back into the smaller box, and electrical energy released as they roll can be harnessed…”.
To expand on this analogy, the electrolyte is the surface of the hill which the balls roll up and down. So, increasing the ease with which the balls can roll up and down the hill, by modifying the electrolyte, represents a potential gain in efficiency.
Traditional batteries use a liquid electrolyte: a solution of a lithium salt in an organic solvent. The lithium ions flow through the solution, thereby ferrying charge between the cathode and anode. However, for liquid electrolytes, there is an inherent resistance to the flow of ions, as the disordered molecular structure of the liquid disrupts the ions’ movement.
Returning to the analogy above, imagine the hill which the tennis balls roll over being covered in long, unkempt grass, inhibiting the smooth rolling of the balls up or down the hill. The balls are slower to roll down the hill, and thus reluctant to release their stored energy. Moreover, a portion of the stored energy is actually released into the grass as heat. In terms of a battery, this release of heat into the electrolyte reduces the electrical efficiency of the battery. This also puts a ceiling on the maximum rate of discharge possible with a liquid electrolyte, as the heat released into the electrolyte needs to be dissipated so as not to overheat the battery.
To add to the mix, the organic component of the electrolyte is often highly flammable, which poses an obvious safety risk as temperatures increase.
Another artefact of using a liquid electrolytes is that micro-filaments of lithium metal can deposit inside the electrolyte solution, especially during faster rates of discharge. These deposited lithium filaments can interrupt the path of the ions between the anode and the cathode reducing the capacity of the battery. They can also have a more destructive effect if they grow to bridge between the anode and cathode causing a short circuit - uncontrolled discharge of the battery, rapid heating, and possibly fire.
In order to mitigate these risks, a relatively large gap needs to be maintained between the anode and cathode, filled with an equally large volume of liquid electrolyte. However, this larger gap and volume increases the electrolyte’s resistance (thereby reducing efficiency) and also increases the size of the battery (thereby reducing energy density).
One potential solution to these problems lies in the use of solid electrolytes.
Solid electrolytes afford higher energy density and allow for faster discharge rates. The ordered crystalline structure of a solid is easier to arrange so that the lithium-ions can navigate and pass through than that of a liquid. So, rather than the hill being covered in long grass, the balls have a smooth, flat ramp to quickly and efficiently roll down. As a result, less energy is dissipated into the electrolyte as heat, allowing for faster discharge rates and greater efficiency.
In addition, the solid material inhibits the formation of lithium filaments, as it is simply not thermodynamically viable for the filaments to form inside the solid structure. This all but eliminates the risk of short circuits in the battery, so the solid electrolyte layer can be made thinner and the energy density increased alongside reduction in the physical size of our batteries.
However, it is not all plain sailing. The crux of an electrolyte is that it must be selectively conductive, enabling the transport of lithium ions, but not electrons, to maintain the charge separation needed for electrical energy storage. This property is inherent to the salt solutions used for liquid electrolytes, but is much less common in solids.
One family of materials which do afford this property is ceramics. Their porous structure allows lithium ions to be shuttled through the solid, but the lack of free electrons avoids parallel electron transport.
However, as anyone who has dropped their favourite mug on the floor will tell you, ceramic’s mechanical properties are not always suited to withstand the physical demands placed on modern day batteries.
In the early 2000s, the aerospace industry sought to improve the mechanical properties of ceramics, so that their excellent thermal properties could be leveraged for spacecraft and the like. They went about this by incorporating nanomaterials throughout the ceramic matrix (as discussed in the Royal Society article "Micromechanics of fracturing in nanoceramics") to increase the fracture toughness.
Recently, a group at Brown University have explored the potential of this technique in ceramic battery electrolytes (as explained in their Matter article "High-Toughness Inorganic Solid Electrolytes via the Use of Reduced Graphene Oxide"). The group use graphene platelets, evenly dispersed throughout a lithium aluminium titanium phosphate (LATP) ceramic, to provide reinforcement. The composite material is made by mixing the platelets of graphene and powdered LATP, before heating to around 1000 ºC to form a more resilient ceramic electrolyte. In fact, a more than two-fold increase in mechanical toughness is achieved.
Both the ratio of ceramic to graphene and the size of the graphene platelets needs to be carefully controlled. Graphene is highly conductive, so increasing the ratio of graphene or the size of the platelets risks increasing the electron conductivity of the ceramic, which would render the material useless as an electrolyte.
The group found that keeping the graphene content at around 1% by volume was the sweet spot - enhancing the fracture resistance such that the electrolyte is usable in normal applications, while not increasing conductivity to the detriment of battery performance.
Meanwhile, a group from the University of California have taken a different approach to solving this brittleness issue - by looking at the way batteries are manufactured.
Traditional manufacturing techniques stack electrolyte sheets between cathode and anode layers. Once the electrolyte is firmly sandwiched between these outer layers, the cathode and anode can reinforce the delicate electrolyte, but pre-sandwiching, the electrolyte sheet is prone to cracking. As a result, manufactures are forced to use thicker, more durable layers of electrolyte to guard against these cracks. Of course, this has a knock-on effect for the energy density and efficiency of the resulting batteries, meaning the full potential of the solid electrolyte material cannot be realised.
However, a pioneering new approach to battery manufacturing completely circumvents the need to handle the solid electrolyte, and instead forms the solid electrolyte from a solution directly on the cathode (as described in the Royal Society of Chemistry article "Designing solution chemistries for the low-temperature synthesis of sulfide-based solid electrolytes").
The cathode is covered in a solution of P2S5, which is then ‘cured’ by treatment with a LiSEt nucleophile. The LiS- anion breaks the phosphorous-sulfur bonds of the P2S5 to form a β-Li3PS4 ceramic. This reaction can also take place at low temperatures, opposed to the 1000 ºC required for traditional solid state syntheses, so the technique is compatible in-situ with standard cathode and anode materials.
Using this technique, the solid electrolyte is never formed without its cathode reinforcement, meaning the layers can be made thinner without having to worry about the handling requirements. The interface between the cathode and electrolyte surfaces is also more seamless - improving the efficiency of the ion flow between the two materials.
In a similar vein to the graphite reinforcing discussed above, these liquid formed ceramics can also be infused with additional reinforcing materials. Helpfully, the low temperature synthesis allows ‘standard’ reinforcing materials to be used, which would otherwise decompose during a 1000 ºC solid state synthesis. For example, Kevlar fibres have now been used in tandem with this β-Li3PS4 liquid synthesis to provide an ultra-thin reinforced electrolyte layer (as explained in the American Chemical Society article "Cathode-Supported All-Solid-State Lithium–Sulfur Batteries with High Cell-Level Energy Density"). Using the Kevlar scaffold, researchers managed to produce a usable electrolyte layer only 100 µm thick - around a 50 % reduction over the latest solid formed electrolytes.
Looking forward, it is expected that exploring new nano-reinforcements, in combination with these innovative synthesis and manufacturing techniques will be needed to realise the full potential of solid state lithium ion batteries. These advances should help to move solid state battery technologies out of the lab and into the hands of the masses with the result that the batteries we use in our everyday devices could be smaller, go for longer between charges, and charge up more rapidly when needed.
Niles is a Patent Attorney working in the chemistry field. Niles has an MChem degree in chemistry from the University of Oxford. His undergraduate research project was on the synthesis of novel perylene diimide containing macrocycles for anion recognition and sensing applications.
Email: niles.beadman@mewburn.com
Our IP specialists work at all stage of the IP life cycle and provide strategic advice about patent, trade mark and registered designs, as well as any IP-related disputes and legal and commercial requirements.
Our peopleWe have an easily-accessible office in central London, as well as a number of regional offices throughout the UK and an office in Munich, Germany. We’d love to hear from you, so please get in touch.
Get in touch