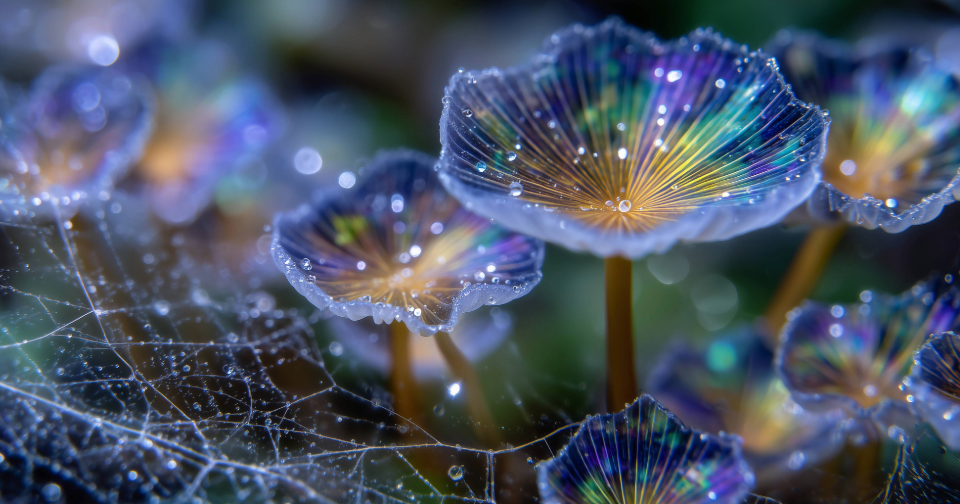
Not only are textiles the biggest source of microplastics globally, supplying the world’s clothing is also responsible for more carbon emissions than the aviation and marine shipping sectors combined.
The UK currently leads fashion sales in Europe, and in fact, we are the third most valuable apparel market globally. Inevitably, with high sales comes a lot of waste – as a country we send over 300,000 tonnes of clothing to landfill every year despite an estimated 95% of that being suitable for re-sale or recycling.
There is a massive opportunity for improvement here, and innovators are following a number of strategies to mitigate the environmental impact of the fashion industry. These strategies include: promising to utilise waste streams, engineering new bio-degradable textiles, reducing microplastic emissions, boosting the second hand market, and developing new recycling technology.
Evolution has already provided humanity with a range of versatile, biodegradable and renewable clothing materials. Natural materials like wool and leather can be used to make durable clothing that can withstand years, if not decades, of use. Is the answer, therefore, to rely on natural materials?
Whilst it is true that natural materials do not shed persistent micro-pollutants, or rely on toxic starting materials, their intensive production on a massive scale still poses significant environmental challenges. Take cotton, the most widely produced natural fiber: although entirely renewable, its cultivation requires substantial amounts of water and arable land. The heavy use of fertilizers and pesticides in cotton production threatens the very land it grows on, contributing to soil degradation and water pollution. Despite accounting for 16% of the total global insecticide use, cotton is only responsible for 26% of the global textile production. The current growth in cotton production is simply not sustainable.
So what are the alternatives?
Some natural materials could be lab-grown, such as the synthetic spider silk made by Bolt Threads. Although still in the R&D phase, a dress for the Museum of Modern Art was produced through a collaboration with Stella McCartney, demonstrating the credibility of their technology.
However, while many natural textiles have properties that synthetic fibers cannot match, the same is true in reverse. Sportswear without elastic materials like Lycra would be uncomfortably tight without stretching as you moved; and many synthetic fibers can be engineered to wick away sweat while you exercise, instead of absorbing it like cotton. There is a balance needed – both synthetic and natural materials have unique properties suited to different items of clothing. Therefore, technology needs to step up to the challenge and produce naturally-based textiles, improve upon the biodegradability of existing materials, and reduce the amount of waste going to landfill.
Many synthetic textiles are made from virgin petrochemical feedstocks. However, there is now increasing interest in making use of waste streams to produce textiles with a lower environmental impact.
Bioplastics are those made from renewable biomass resources. These starting materials trap carbon from the atmosphere, meaning that many bioplastics can have negative carbon footprints and thereby offering a valuable option for reducing emissions.
Cellulose is by far the most abundant polymer on the planet and is found in all terrestrial plants, the most accessible source of which is waste produced from crop farming. This agricultural waste represents a huge pool from which to draw feedstocks for producing bioplastics - the European Union alone is expected to produce 139 million tonnes of cellulosic crop residues in 2030. Cellulose is already used as feedstock for fabrics. For example, Viscose (Rayon) is purified cellulose spun into fibers, often being made from wood pulp or recycled paper. However, cellulosic fibers only makes up only 6% of all garments, a small proportion of the global clothing supply.
A new, surprising use for cellulose has been developed by Sparxell – sequins.
Garments made from sequined fabrics present a unique challenge for sustainability: they are fragile and difficult to repair, often resulting in short product lifetimes. Sequins are also shed during wear, and once shed, these sequins persist in the environment without biodegrading. Typically, sequins are made of metallicized plastic (often PVC or PET); Sparxell have developed a process to recreate metallic effects using pure cellulose – no metal film or plastic needed.
‘Green’ textiles are growing rapidly. This is partly due to a significant consumer demand for plant based, biodegradable textiles where production methods avoid toxic dyes/pigments and/or excessive water requirements. Another factor is increased regulation for companies to look into their supply chain and address adverse environmental impacts along their value chain (e.g., EU corporate due diligence directive) – this appears to be influencing clothing brands, who are looking for green alternatives with better traceability than their existing supply chain.
Benjamin Droguet, Founder & CEO – Sparxell
Taking inspiration from the vivid metallic blue fruits of Viburnum tinus, an evergreen shrub widely used in hedges across the UK, Sparxell developed structurally-coloured films formed entirely from cellulose nanoparticles that come in a variety of metallic colours. Not only could this replace sequins but other materials in garment design such as metallic threads and glitters, as well as finding use in beauty products and cosmetics.
Elastomers (such as Lycra) are another ubiquitous yet difficult-to-replace group of materials. These fibers add stretch to a material, making typically stiff fabrics such as nylon suitable for sportswear. Often these are made using petroleum-based rubbers. However, Borealis has recently introduced the Bornewables™ line of Queo™ plastomers and elastomers formed through chemically recycling waste vegetable oils. Bornewables have the potential to be carbon-negative materials, totally offsetting emissions from manufacture by the carbon capture of the initial crop used to produce the oil.
In fact, even high-performance materials can be made from vegetable oils: Arkema produces Rilsan, a type of nylon, from castor bean oil. While typically used for high-performance cabling and optics for automotive and aerospace applications, this material offers durability unseen in natural textiles. Excitingly, Rilsan has now been used in ski socks and luggage.
Another key challenge in reducing the environmental effects of the textile industry is addressing the non-biodegradable waste resulting from synthetic textiles. In particular, there is a drive to reduce the shedding of microparticles which often end up in the world’s oceans.
Soleic produces fully biodegradable polymer foams that can be used to replace typical polyurethane foam in surfboards and footwear: Blueview shoes (which use Soleic’s foam) will fully degrade under composting conditions. By introducing polyester groups in the polyurethane polymer, it can be degraded by bacteria and fungi. Currently, Soleic uses oils derived from algae to reduce the amount of petrochemical-sourced starting materials by half.
It is also possible to produce biodegradable materials from petrochemicals. While not carbon neutral, they promise to significantly reduce the microplastic burden on the oceans when compared to typical oil-based polymers. They could also be significantly cheaper than biopolymers, which is key for expanding green textiles to developing countries which are often highly price-sensitive, as well as making these green textiles suitable for use in fast fashion where they might have their highest impact.
Polybutylene succinate (PBS) is one such polymer and is gaining traction as it shares many properties with typical (non-biodegradable) polymers such as polypropylene used in textiles and food packaging. PBS is more durable than bioplastics such as polylactic acid. Mitsubishi Chemical produces BioPBS, which uses naturally sourced succinic acid to reduce the amount of petrochemical materials uses in PBS manufacture, and promises to be a valuable compromise between traditional synthetics and bioplastics.
Currently, synthetic polymer textiles – primarily polyester – account for the majority of clothing items produced. Synthetic fibers can be engineered to be stretchy, durable, lightweight and waterproof. Yet for all their benefits, almost all synthetics do not biodegrade and are easily shed from clothing during use and washing, producing masses of microplastic particles that ultimately collect in the oceans.
Textiles are responsible for the majority of microplastic pollution, with an estimated 6,870 to 17,847 tonnes of polymer microfibers are released from laundry every year in the UK alone. Worryingly, these microplastics appear everywhere we look: from the top of Mount Everest to the bottom of the Mariana Trench, and even inside our own bodies.
While replacing existing polymers with biodegradable alternatives will go some way to reduce the microplastic pollution caused from laundry, there is also significant development in technology acting to reduce the amounts of microplastics reaching the ocean, as discussed in our previous blog: Microplastics: tiny particles causing huge problems
As most microplastics originating from textiles are released during laundry, it is possible to catch them before they reach the environment. Washing machines with in-built filters are currently offered by Grundig, Bek and AEG, or filters can easily be retrofitted to older machines. Planetcare offers filters than can be retrofitted to older machines – the filters are even closed-loop, with all used filters being refurbished for reuse.
France has passed legislation that will require these filters on washing machines by 2025. Similar legislation has passed in Australia and has been proposed in the UK.
Textiles themselves can be engineered to reduce the amount of microplastic shedding. By coating polyester in an environmentally friendly silicone, shedding of microplastics can be reduced by 90%. Italy’s Institute of Polymers Composites and Biomaterials has found that similar reductions in shedding can be achieved with pectin, a starch found in fruits.
As lockdown came to an end, the UK saw a surge in fashion sales. This has been made all the easier by “buy now, pay later” creditors such as Klarna, which has appeared as an option at almost every retailer. SHIEN overtook Amazon in app downloads, showing the continued rise in fast fashion. Asos has even noted that delivery is no longer a cost of sales but rather an operating expense, as people expect to be able to be able to return delivered clothing free of charge.
While technology is fuelling the rise of the online fashion industry, it is also offering innovations that reduce waste from e-commerce. Virtual try-on-and-see fitting, which is allowing customers to test garments at home, is helping to reduce the growing number of mailed returns. Powered by generative AI, Google search is allowing users to simulate how clothing will drape, fold, cling, and stretch; showing wrinkles and shadows on a diverse selection of models – all from a single image of the garment.
Despite an increase in first-hand sales, we also see that the second-hand market is booming, and rental is becoming a more accessible option. Even the Duchess of Cambridge has rented instead of buying: the dress she wore when attending the 2022 Earthshot prizes was rented for £74 from Hurr. Hurr offers both peer-to-peer rentals, allowing individuals to lease items without the logistical hassle, and also hosts retail giants such as Selfridges, allowing customers to rent pieces from Prada, Saint Laurent, Bottega Veneta, Burberry and Off-White, all for a fraction of the price of buying. And, through a partnership with the sustainable dry-cleaning service Oxwash, Hurr makes a compelling argument that renting is the eco-friendly way of accessing high-end fashion.
There is also a move towards verification technologies for high fashion. As platforms such as Depop and Vinted continue to grow, the threat of receiving counterfeit goods is rising – almost $50 billion is lost to counterfeits a year. In view of this, retailers are launching authentication services to improve the second-hand market. Ebay is offering in-person sneaker authentication while companies such as Authentique are again using AI to provide a non-invasive at-home service. MCQ, by Alexander McQueen, is going a step further and has partnered with Everledger to link items of clothing to the blockchain to ensure that the authenticity of the item can be verified. Authentication can even be built into a product itself: AlpVision is able to introduce digitally encoded microscopic surface textures to product finishes that can be easily authenticated with a smartphone camera, without affecting the quality of the item. Their process can even be configured retroactively to use microscopic irregularities present from existing manufacturing processes.
As discussed in our previous blog, Circular economy: new technologies rise to the challenge, there is a growing push away from the typical “take, make and waste” model and towards a circular economy, where the end of a product’s life is considered during manufacture. The EU is accelerating this shift and is proposing rules to make producers responsible for the full lifecycle of textile products.
Ultimately, whether rented or resold, if a garment is not suitable for resale, the item will have to be disposed of. Unfortunately, landfill is by far the most common destination for these items: currently only 12% of clothing is recycled, with just 1% going to create new garments.
Typically, fibers are mechanically recycled (e.g. cotton being teased apart, back into loose fibers) or thermally recycled (e.g. PET being melted down and re-spun into fibers); both of these methods create a limit on how many times a fiber can be recycled. Mechanical recycling shortens fiber lengths, making recycled thread weaker, and thermal recycling degrades polymer molecules, making colouring textiles more difficult.
However there is growing work in the chemical recycling space – where textiles are broken down and reformed through chemical reactions, making the recycled product indistinguishable from virgin materials.
Renewcell offers Circulose®, a viscose material made entirely from textile waste instead of the typical wood pulp. Infinited Fiber has developed Infinna™, an alternative to viscose that does not use toxic carbon disulfide to produce new fibers. New polymers are also being developed, such as PDK (polydiketoenamine), which has been engineered to have a simple and efficient recycling process that uses acid and heat to break down fibers back into starting materials. Reforming the material is even easier – mechanical mixing is all that’s needed, no solvents, catalysts or additives required.
Currently complex items, such as shoes and bags, or textiles with multiple fiber types like polycotton or elastane blends, are often destined for landfill as separating components is too costly. Interest in this area is rapidly growing and technology is being developed that promises to close the loop on even the most complex fashion items.
Valvan’s Fibersort™ uses AI and near-infrared scanning to effectively sort items by material (and even by fiber blends) and colour. Their Trimclean™ process then uses similar technology to remove trims, buttons and zips from garments to produce material suitable for recycling without requiring expensive manual labour.
Even when separated from other materials, polycotton represents a unique difficulty for the recycling process. The reason is that individually, both cotton and polyester are easily recycled but by very different recycling processes. Blending the two makes a material that neither recycling process can deal with. Circ has developed an innovative recycling technique that allows the separation of the polymer and cotton from polycotton. By using a hydrothermal process, polyester can be broken down into its constituent parts leaving the cotton ‘skeleton’ unharmed. The components of the polyester can then be used to make virgin polyester for new garments. Having secured $30 million in funding from the Bill Gates-lead Breakthrough Energy Ventures and additional funding from Inditex (the parent company of Zara and Pull&Bear), Circ hopes to complete a plant capable of recycling 65,000 tonnes of polycotton by 2025.
Leather goods are some of the most durable fashion items: with a bit of TLC, a leather jacket can easily last 30 years or more. Imitation leather, on the other hand, is notoriously fragile and difficult to care for. Wear and tear will often destine a faux-leather item for landfill in just a few years.
While having long lifetimes, leather goods come with a considerable carbon footprint. Raising livestock for leather releases significant amounts of greenhouse gases. In fact, the production of a pair of cow-skin leather shoes contributes over 40 kg of carbon emissions from the hide alone, nearly seven times that of an equivalent polyurethane synthetic alternative.
Yet most synthetic leathers, while avoiding materials derived from animals, rely on petrochemical products such as polyvinyl chloride and polyurethane. Often branded as vegan and eco-friendly, due to producing lower emissions compared to cow-hide leather, the polymer-based leather replacements used by many vegan leather manufacturers may be even more environmentally damaging than natural leather. While steps have been taken to replace harmful solvents such as dimethyl formamide (DMF) with water to produce “eco-friendly polyurethane”, the resulting plastic is still non-biodegradable and is a persistent pollutant in the environment.
A number of innovators are looking to produce leather alternatives that reduce the reliance on petrochemicals, and produce biodegradable alternatives.
Toray has been a key player in the artificial leather space for over 50 years. Introduced in 1970, Ultrasuede® is made of ultra-fine PET fibers layered on a durable backing. This results in a material that is lighter and more uniform than leather while providing a soft suede-like texture, ideal for replacing animal leather in fashion items and interiors.
In 2015, Toray began producing Ultrasuede using PET with 30% plant-based starting materials. With sights set on 100%, Toray has recently developed entirely plant-based PET using ethylene glycol from molasses and dimethyl terephthalate from corn starch. The durable backing is now made using recycled materials and partly plant-based polyurethanes and polyesters.
As discussed in a previous blog post, Polymer composites using natural fibres – growing reinforcements, growing in popularity, leather products can be made with a wide variety of waste materials, reducing the reliance on petroleum derived polymers. Vegea uses waste products from the wine industry in the manufacture of polyurethane leather, using grape seed oil in polyurethane production and including reinforcing fibres derived from grape skins and stalks. Ananas Anam’s Piñatex® uses discarded pineapple leaves to produce a durable base layer, which then only needs a thin coating of polymer to produce a leather replacement. Not only does Piñatex offer an environmentally friendly alternative to leather, its production also provides an additional income stream to pineapple farming communities.
Ecovative goes a step further - Forager™ hides are fully biodegradable and made with entirely natural, renewable materials. This leather replacement is made from 100% mycelium (the ‘roots’ of mushrooms), without any oil-derived products, fillers or plastics. Grown in just 9 days, the mycelium hides can be tanned and finished just like regular leather.
Another company working in this space are Cambond, who have used their expertise in resin technology to develop leather replacements from a number of different waste streams. At the high-end Cambond have developed “Beer Leather” made from beer waste sludge, which has been used to make belts and dog collars. They have also produced hemp-based “leather”, which is glossy to the touch and is envisaged for usage in car interiors. Cambond have even made “leathers” from carrots and tomatoes which retain the bright colours of their vegetable feedstocks. Amazingly, the carrot based “leather” is even biodegradable at the end of its useful lifespan.
There is even development in the recycling sector: while not typically thought of as a recyclable material, even discarded or scrap animal leather can be made into sustainable alternatives to whole-hide leather. Recyc Leather™ uses recovered leather fibers along with natural rubber to produce a durable base layer, with a thin synthetic coating to provide the surface finish. This surface coating makes up just 10% of the total weight of the product, a significant improvement over typical synthetic leathers.
Even in just the leather replacement space, we are seeing many innovators taking different approaches to reducing the impact of the fashion industry. We look forward to exploring more areas of development in the textile field in future blogs.
These innovations show that significant steps are being made to weave sustainable technologies into the fashion industry, with a circular economy for clothing seemingly within reach.
With London Fashion Week underway, we hope to see sustainability taking more of the limelight. Some designers are already focussing on sustainability however other events have gone further, with Copenhagen fashion week setting out 18 requirements for sustainability for designers to enter.
This blog was originally co-authored by Thomas Lonsdale and Sam Haggerty.
Thomas is an associate patent attorney with experience in drafting and prosecution of patent applications for a range of European and international clients in the fields of chemistry, biochemistry, pharmaceuticals and materials. He has also worked on FTOs and attended proceedings before the EPO. Thomas holds a Masters (MChem) and doctorate (DPhil) from the University of Oxford in which he specialised in biocatalysis.
Email: thomas.lonsdale@mewburn.com
Our IP specialists work at all stage of the IP life cycle and provide strategic advice about patent, trade mark and registered designs, as well as any IP-related disputes and legal and commercial requirements.
Our peopleWe have an easily-accessible office in central London, as well as a number of regional offices throughout the UK and an office in Munich, Germany. We’d love to hear from you, so please get in touch.
Get in touch