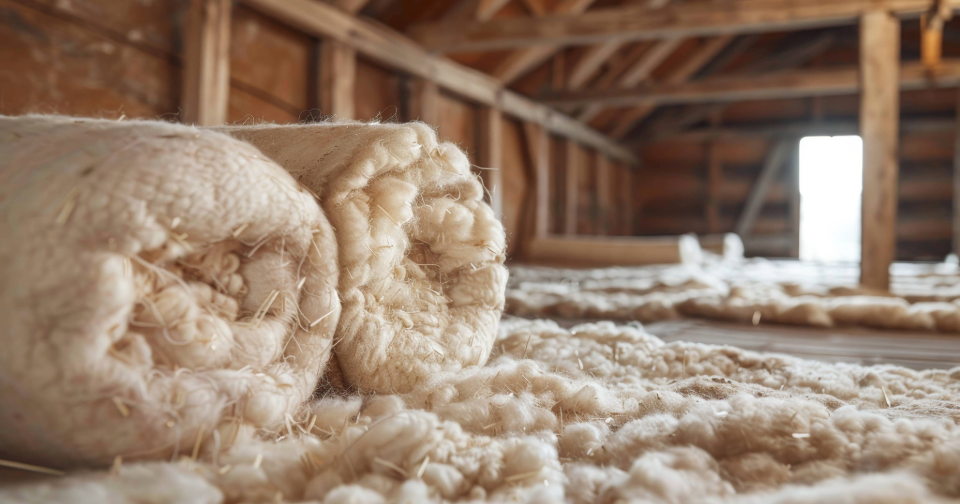
The importance of lithium ion (Li-ion) batteries in modern society is no secret. They dominate the rechargeable battery market due to their high power density and cycling stability, making them suitable for a vast range of applications, from mobile phones to electric vehicles.
However, there are a number of drawbacks to Li-ion batteries, including potentially catastrophic cathode phase changes when overcharged or physically damaged. Additionally, there are serious concerns over the ecological impact of the mining of lithium and cobalt (cobalt often being a key component of the cathode material), the latter also resulting in stark reports of human rights violations in its mining practices.
Here at Mewburn, we have discussed many innovations in the lithium battery industry. Some of the promising advances include finding alternatives to cobalt-containing cathodes, developing new separators to facilitate the use of lithium metal cathodes, adapting the electrolyte used, and optimising the anode material. However, one thing remains in common in these developments: lithium.
Some innovators are looking to provide batteries which overcome the problems with Li-ion batteries by replacing lithium entirely: enter sodium-ion.
Lithium is the most popular metal ion for use in rechargeable batteries because it is the lightest metal element, thus allowing for the highest theoretical charge density. But some companies in the industry are realising that, by using sodium instead, batteries with different and advantageous properties can be made.
For example, Faradion, a UK-based world leader in non-aqueous sodium-ion cell technology, boasts that its proprietary batteries can provide lithium-ion performance at lead-acid prices. Faradion foresees the technology being ideal for stationary storage applications due to the high energy density, improved safety, and lower cost. It is not limited to stationary storage though, with Faradion demonstrating the world’s first sodium-ion battery-powered vehicle in the form of an e-bike back in 2015.
Li-ion batteries have occasionally conjured up horror stories of mobile phones exploding or electric cars catching fire. This can be caused by short-circuiting due to the formation of metallic dendrites growing through the separator during charge/discharge cycles. One type of dendrite that forms in a typical Li-ion cell is copper dendrites. These form when the battery is severely over-discharged, causing the copper current collector to be dissolved. The Cu-ions are then deposited on the cathode during charging which results in the dendrites. Because of these safety concerns, Li-ion batteries contain mechanisms to prevent them from being discharged below 30% of their storage capacity. This means that a large amount of the stored energy cannot be utilised.
On the other hand, sodium-ion (Na-ion) batteries are able to use only aluminium current collectors, because sodium does not alloy with aluminium as readily as lithium. This means that there is no risk of dangerous copper dendrites forming, thus allowing the batteries to be fully discharged safely to 0 V. As a bonus, aluminium is lighter than copper, which helps to offset the lower charge density of sodium ions.
Additionally, the Na-ion cells can use propylene carbonate (PC) as a thermally and oxidatively stable solvent. PC cannot be used in most Li-ion cells because it degrades the graphite electrodes, hence a more flammable solvent is used.
The raw materials for Na-ion batteries can be obtained from abundant sources which are not limited to specific regions. Sodium is one of the most abundant elements in the Earth’s crust and the oceans covering our planet, while hard carbon (which can be used as an anode material) can be extracted from waste biomass. This could help ease international tensions over resources for battery materials, and reduce the greenhouse gas emissions associated with transporting the materials around the world.
No benchmark cathode material has yet been set for Na-ion batteries, but some frontrunners include Prussian white analogues, layered oxides, and polyanion structures. These can be made using metals such as iron, nickel, manganese and vanadium, which could reduce our dependence on cobalt.
The sodium technology can also be implemented into existing lithium cell production lines, meaning that much of the necessary infrastructure to adopt a sodium economy is already in place across the globe.
Clearly, for us to give up our precious lithium-ion batteries, the sodium-ion alternative will need to perform comparatively well. Luckily, recent Na-ion batteries have shown similar capabilities to Li-ion ones whilst being cheaper to mass-produce – and this is only likely to improve in years to come.
Current leading Na-ion cells tend to have a cycle life of around 2000 cycles and an energy density of between 100 and 150 Wh/kg, compared to Li-ion’s typical cycle life of about 3000 cycles (e.g. for lithium iron phosphate cells) and typical energy density of 120 to 180 Wh/kg. That said, Faradion’s prototype Na-ion pouch cells boast a cycle life of 4000 cycles to 80% capacity and an energy density of 190 Wh/kg, which certainly rivals typical Li-ion cells. Similarly, Swedish company Northvolt has recently unveiled a new Na-ion battery with an energy density of 160 Wh/kg, with claims that it can raise this number to 200 Wh/kg in its next generation of batteries.
The Na-ion battery market is at a critical point of rapid commercialisation. At the tail-end of 2023, two Chinese companies unveiled two of the world’s first Li-free, Na-ion battery-powered cars. The first was developed by JAC, backed by Volkswagen, and the second originates from JMEV, majority-owned by Renault. JAC’s vehicles incorporate an Na-ion cell from CATL, a Chinese battery firm who are the leading global EV battery manufacturer (securing a global market share of nearly 37% in 2023), and who are making substantial investment into Na-ion technology. Meanwhile, JMEV’s vehicle uses a battery from Farasis Energy and has a range of 251 km, which is only slightly less than the 301km range of its Li-ion sister. Clearly, this presents a promising alternative for EVs, especially as more research goes into Na-ion technology.
With such potential in this market, it is vital that innovators take the necessary steps to protect their inventions, especially at this early stage of market growth. Therefore, it is no surprise that we have seen a clear increase in patent applications in this field over the past 15 years.
The number of international (PCT) patent applications published since 2008 related to Na-ion batteries1
The graph above shows the number of international (PCT) patent applications published since 2008 directed towards sodium-ion battery technology. Apart from a couple of notable dips in 2018-19 and 2021-22, with Covid-19 possibly being responsible for the latter, there has been a steady increase, with a marked recent rise in 2023. These numbers are far lower than the number of patent applications related to Li-ion cells, but the Na-ion industry is still in its adolescence, and a 2023 market study predicts the market will grow to be worth USD 4.8 billion by 2032 (up from USD 0.86 billion in 2022).
Clearly, there is a plethora of opportunity to innovate and develop sodium-ion technologies to the point where they are commonplace in everyday life. We can expect to see them much more over the next decade.
1Search conducted for WO publications on Espacenet with (“sodium-ion” OR “Na-ion” OR “sodium ion” OR “Na ion”) AND (“battery” OR “secondary cell” OR “batteries”) in the title or abstract, and categorised as IPC main group H01M10 (“Secondary cells; Manufacture thereof”).
Matt is a trainee patent attorney in our chemistry team. Matt has a BSc and MChem in Chemistry and Mathematics (Joint Honours) from the University of Leeds. His Master’s research project involved the synthesis and characterisation of metal-organic frameworks incorporated into polymer films which have potential for use in hydrogen fuel cells. Matt also carried out a summer research project funded by the Royal Society of Chemistry which utilised computational chemistry to model reactions in the interstellar medium.
Email: matthew.barton@mewburn.com
Our IP specialists work at all stage of the IP life cycle and provide strategic advice about patent, trade mark and registered designs, as well as any IP-related disputes and legal and commercial requirements.
Our peopleWe have an easily-accessible office in central London, as well as a number of regional offices throughout the UK and an office in Munich, Germany. We’d love to hear from you, so please get in touch.
Get in touch