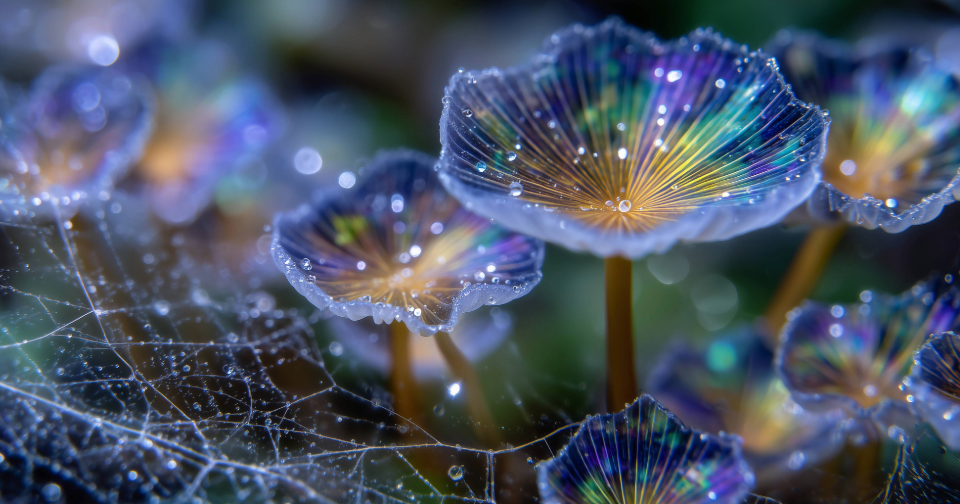
The UK government has recently vowed to cut 68% of CO2 emissions by 2030 in a bid to tackle climate change. To meet this goal, there will be a ban on new petrol and diesel cars and almost half of the UK’s vehicles must be electric by the same year. This means replacing 16.1 million cars with electric vehicles (EVs) – currently there are only around 200,000 EVs registered in the UK.
The UK is not the only one driving the transition towards EVs – we are one of 189 countries party to the Paris Agreement, pledging to reduce our greenhouse gas emissions to limit the global temperature increase to only 2°C in the next century. EVs are one of the main ways to meet this pledge. And with the US re-joining this year, it is only a matter of time before we are all driving EVs in an effort to reduce our carbon emissions.
So why have we not adopted more EVs? The main concern with consumers is that EVs have a limited driving range due to the capacity of the battery, also known as “range anxiety”. Increasing the battery capacity is one way to increase the driving range (see our blogs on battery technology). Alternatively, improving the efficiency of vehicles will mean their batteries can last for longer and they can travel further. The three main sources of resistance vehicles experience (and therefore limit an EV’s range) are aerodynamic drag, rolling resistance and weight. Composites, offering a lower weight and much greater flexibility in terms of body panel shape than metal, can help to reduce all three.
Composites are made from a combination of two or more materials with different physical and chemical properties. The individual materials are distinct within the structure of the finished composite, so they are not classified as mixtures or solutions. Composites frequently exhibit properties that are not attainable from the individual components in isolation.
Engineered composites can be classified by their matrix material: polymer-, metal-, and ceramic-matrix composites. Of these three, polymer composites are by far the most ubiquitous thanks to their lower cost and (comparatively) simple fabrication; they accounted for a 75.3% share of the global automotive composite revenue in 2019.
Polymer composites contain reinforcing agents, typically fibres, within a polymer matrix – these are often called fibre-reinforced polymers. Conventional fibre-reinforced composites typically incorporate synthetic fibres, such as glass or carbon fibres. The polymer matrix is usually of a thermoset resin, such as epoxy or polyester resin, which irreversibly hardens during thermal or chemical curing.
In the automotive sector, polymer composites have long been touted as a replacement for heavier metal components, promising a weight reduction whilst maintaining other useful properties such as mechanical strength. The most widespread and well-known composite for such applications is carbon fibre reinforced polymer (CFRP), more simply known as “carbon fibre”, which, within the automotive sector, has most commonly been used in high performance race cars.
Despite the advantages they offer, one of the major challenges in replacing steel structural elements with composites is that the cost of materials and manufacture can be significantly higher, even with optimised processing technology. This issue is particularly pertinent when seeking to introduce composites into mass-production vehicles; here cost is of a much greater concern than with the few high-performance, low-production volume road vehicles where widespread use of composites has been seen so far.
For this reason, many in the industry are of the opinion that starting from a part originally designed to be manufactured from metal and seeking to simply replace the metal with a composite (a so-called ‘black steel’ conversion) is the wrong way to approach the challenge. They suggest that attractive use-cases for composites can instead be found when starting from a blank sheet and designing the part in such a way that it makes best use of the beneficial properties that composites bring to the table. These include flexibility in design, corrosion resistance, and functional integration (like Porsche’s recent patent for a composite vehicle component with integrated electronics), and will facilitate the industry in moving beyond mere light-weighting of existing parts. Gordon Murray’s IStream and IStream Superlight have already shown the benefits of radically rethinking the design and manufacture of cars when looking to incorporate composites, so mainstream manufacturers should have confidence in ripping up the rulebook.
Autonomous and electric vehicles represent an excellent focal point for efforts to develop cost-competitive composite solutions: the number of parts that have fundamentally different design requirements and constrains to their equivalents in internal combustion engine (ICE) vehicles, or are completely new, is significant. It is therefore back to the drawing board that engineers will go, freed from the inertia and dogmas that exist in designing ICE vehicles. Some obvious examples spring to mind, including components for battery integration and protection (which we have previously covered Tesla’s progress on in our blog Batteries are no longer just passengers in electric vehicles) and changes to drivetrain components for use with electric motors. However, more radically, the rise of autonomous vehicles will hopefully also see us move away from the idea of vehicles being steel boxes with rows of forward-facing seats – new unibody frame shapes will surely arise to take advantage of occupants of the vehicle not needing to face the road or control the vehicle.
It’s on this last point that composites have another distinct advantage over metals: the ease of forming structures with shapes far disconnected from the box-like structures of most cars. There are already cases of this proving a significant advantage with EVs. Aptera Motors’ futuristic-looking solar-powered electric vehicle that recently took in $250 million worth of pre-orders has a composite monocoque chassis and uses a raft of other composite structures in order to provide a vehicle with an highly aerodynamic shape and incredibly low weight. The result is a range of over 1000 miles - around four times that of vehicles with similar sized battery packs! An elegant solution to consumers’ range anxiety courtesy of composites.
Nevertheless, material cost is not the only hurdle for composites to clear before their use becomes widespread. Another difficulty is integration into existing supply chains and production lines for vehicles. Even once a use-case for composites has been identified, it can be a major challenge for the component to achieve the required speed-to-market time when it is to be manufactured from composites. This is in part because composites have lots of options when it comes to fibre selection, resin selection, and how the selected fibres and resin are combined; whereas metals are relatively simple. Whilst automotive manufacturers have years of experience of computationally modelling how metal structures react to real-world forces, their know-how in optimising composites is comparatively still in its infancy.
Having arrived at an optimised design, manufacture is not straightforward either. Resin transfer moulding (RTM), where a dry fibre preform (an assembly of dry fibre layers pre-shaped into the desired form) is positioned in a mould that is subsequently injected with resin, is the technology leading the way for mass-manufacture of composites. This is thanks to the short time the process takes to go from a dry preform to a cured part, the consistency of output and the absence of an autoclave step (where the composite is raised to high temperatures and pressures). However, manufacture of the preform, where fabric sheets and filaments are cut and stacked or wound to provide the required shape and fibre orientations before going into the mould, is a complex process. Fortunately, there has been ongoing development in automation of the traditionally manual processes of preform manufacture using very impressive automated machines for fibre placement and braiding, allowing the preform to be assembled even more accurately and quickly than with expert human hands. Existing solutions currently come with high tooling costs and engineering expertise in using them is not widespread outside the aerospace industry, but both these barriers should diminish as use of composites in the automotive sector grows.
Ford is pushing towards using more composites within their cars, and has recently joined Composites UK, a trade association that encourages growth and development for the UK composites industry. They have also filed several patent applications recently using composites for a new engine cylinder head and a cooling assembly for under the bonnet of future vehicles.
At the other end of a vehicle’s life, lies another challenge: the disposal and recycling of polymer composite materials. This is particularly pressing given the EU directive on end-of-life vehicles that requires 85% of the vehicle (by mass) to be re-used or recycled, but is made difficult by the mixture of components present in composites (see our recent blog Recycling polymer composites (mixed material complicates)). Furthermore, polymer composites are often made from non-renewable resources like petroleum, and fabrication of the synthetic fibres is often energy intensive. Therefore, there has been a considerable push towards minimising the environmental impact of polymer composites by using sustainable “green composites”.
Green composites, or biocomposites, are derived from renewable resources, including low-value agricultural waste, and can be biodegradable. They use natural fibres as the reinforcing agents (see our recent blog Polymer composites using natural fibres – growing reinforcements, growing in popularity) or bio-resins as the polymer matrix, such as poly(lactic acid) (PLA), polyhydroxybutyrate (PHB), and polysaccharides. The energy involved in production of the green composites can be far less than that of traditional polymer composites, so not only are green composites sustainable but may also have a lower environmental impact overall.
Using natural fibre composites in cars is not new. Henry Ford, the founder of the Ford Motor Company, unveiled the “Soybean Car” in 1941, using composites made of soybean fibres in a phenolic resin for the panels of the car. The car was 1000 lbs (454 kg) lighter than a steel car, but the prototype was never mass-produced due to WWII.
Innovation within the automotive sector is often led by motorsport, where the weight of a car is crucial in maximising speed. Four Motors is replacing carbon fibre panels with lighter, greener composites in their long running project: the Bioconcept car. In collaboration with Porsche Motorsport and Fraunhofer WKI, the latest generation of the Bioconcept car uses body panels made from 100% natural fibre composites of hemp, flax and jute. It was successfully tested on the racetrack by the Four Motors racing team under extreme conditions, showing the durability of the green composite panels. Additionally, the composite has a lesser tendency to splinter than fully synthetic composites, reducing the risk of injury in an accident. Next, they intend on utilising bio-resins to develop a door with a biogenic content of 85% in collaboration with HOBUM Oleochemicals GmbH.
Japan’s answer to the Bioconcept car is the NanoCellulose Vehicle (NCV), first exhibited at the Tokyo Motor Show 2019 by the Japanese Ministry of Environment. This two-door sports car is almost entirely made from composites containing wood fibres, more precisely cellulose nano fibres (CNFs) from recycled agricultural waste. These fibres are up to five times as strong, but only one-fifth of the weight of conventional steel panels. The CNFs are combined with polypropylene (PP), polycarbonate (PC), nylon 6 (PA6) and epoxy resins to produce almost all of the body parts and panels, which can be further recycled when decommissioned. The NCV is 10% lighter than a conventional vehicle, improving fuel efficiency and reducing CO2 emissions. In fact, the CO2 emissions for the entire lifecycle of the NCV, from manufacturing to disposal, is reduced by approximately 10% as compared to a conventional car. Unfortunately, it only has a top speed of 12 mph due to its hydrogen fuel cell (as opposed a fuel tank or battery), making it a prime candidate for the slowest supercar in the world!
However, the use of green composites, like other polymer composites, has typically been limited to low-production-volume vehicles, or for interior applications of mass-produced vehicles. Companies are now focusing on mass-producing these greener composites for use in all aspects of the next-generation vehicles.
In fact, Aptera’s solar panelled car mentioned above is made from resin-infused sandwich-core plastic composites made of carbon, Kevlar, and hemp fibres. Hemp is a variety of the Cannabis sativa plant and is one of the fastest growing plants in the world. The composite is lighter than steel or aluminium and provides Aptera with the ability to cost-effectively scale annual production from single digits to tens of thousands of vehicles as demand requires.
Bcomp Ltd. is a Swiss company focusing on producing natural fibre composites on a large scale. The natural fibres used are derived from flax to form a composite made of layers of reinforcement fabrics ampliTex™ and fibre reinforcement grids called powerRibs™. The composite can be compression-moulded to form automotive interior panels with up to 70% less plastic and a 50% reduction in weight compared to other composites. The composite also matches the performance of more traditional carbon fibre parts, with a 75% lower CO2 footprint. Bcomp is driving the use of their composites in next generation vehicles by collaborating with many large car manufacturers, including Porsche on their Cayman 718 GT4 CS MR, Electric GT on their Tesla Model S P100DL racecar (shown below), Volvo on their XC60 hybrid SUV, and Polestar, a Swedish premium electric performance car brand jointly owned by Volvo and Geely, in the Polestar Precept.
Bcomp's composite ampliTex™ (left) has been used in next generation vehicles such as Electric GT's Tesla Model S P100DL racecar (right)
(Images: © Bcomp)
Conventional body panels are not the only car components being replaced by green composites. Batteries are a key component to EVs but are often large and far heavier than those in petrol or diesel cars, reducing the distance the EV can travel. TRB Lightweight Structures have developed lightweight EV battery enclosures made from a sugar-based resin that is 100% derived from agricultural waste biomass, which can be produced at a similar cost to the same part made in heavier aluminium. They recently announced a £19 million deal to export their EV battery enclosures to America in a joint venture with Toyota Tsusho America, Inc.
Larger car manufacturers are also moving towards greener composite materials. GM have recently filed several patent applications for use of natural fibre composites in interior components of vehicles. Daimler uses bast fibres (from the phloem, or the “inner bark”, of the plant) embedded in an Acrodur (acrylate water-based) resin, sourced from BASF, for the roof frames of their Mercedes-Benz E Class vehicles. Ford is collaborating with Heinz (of ketchup fame) to develop composites made of tomato skins that can be used in components of future vehicles. Finally, Toyota is backing the use of composites made from kenaf (a member of the hibiscus family) fibres for future cars in collaboration with Covestro.
Nevertheless, most of the green composites used are a hybrid of natural fibres with petroleum-based resins, or synthetic fibres with bio-resins – all-green composites made from 100% biomaterial have achieved limited success so far. A lot of plant material is required to produce bio-resins, which means they typically cost about 10% more than petroleum-based resins. Furthermore, the adhesion between the hydrophilic (“water-loving”) natural fibres and hydrophobic (“water-fearing”) resins is often weaker than with synthetic fibres, so the natural fibres must be treated to remove the hydrophilic layer to create stronger, durable, bonds. Additionally, green composites often degrade under thermal treatment or upon moisture absorption, deteriorating the desirable mechanical properties. The cost and durability limitations all-green composites still have a way to go before finding widespread use in automotive applications. More research is needed to develop durable and cost-effective all-green composites for the vehicles of the future, whose long-term benefits outweigh challenges with their manufacture.
The beneficial properties of composites can be exploited to provide vehicles that far exceed the capabilities of their steel-centric siblings (and look striking whilst doing it), especially when it comes to electric vehicles. However, the road ahead is not completely clear. Speed-to-market and manufacturing will continue to present challenges until the inertia of an industry built on metal-based manufacturing is overcome. Further innovation and development in the field of sustainable composites, particularly towards all-green composites, is also essential if the automotive industry is to meet their ambitious sustainability targets.
The next few years will likely bring a sea change to the vehicles that zip along our streets, and we, at Mewburn Ellis, look forward to playing our part in it.
Rob Walker also discusses automotive composites in Automotive World. View the article.
This blog was co-authored by Melodie Richardson and Rob Walker.
Melodie is a trainee patent attorney in our chemistry team. She has Master’s degree in Chemistry and a DPhil in Organic Chemistry, both from the University of Oxford. Her undergraduate research focused on synthesising drug candidates for the treatment of ERF-related craniosynostosis. Her doctoral research focused upon developing a novel method to synthesise the bicyclic ketal D ring in the total synthesis of the marine macrolactone pectenotoxin-4.
Rob is a patent attorney in our engineering and ICT team. Rob has an MEng degree in Chemical Engineering from the University of Cambridge. His masters research project focussed on three-dimensional analysis of particle-size segregation within granular avalanches using magnetic resonance imaging. During his undergraduate studies, Rob spent time working for Proctor & Gamble within their Baby-Care R&D Group.
Email: rob.walker@mewburn.com
Our IP specialists work at all stage of the IP life cycle and provide strategic advice about patent, trade mark and registered designs, as well as any IP-related disputes and legal and commercial requirements.
Our peopleWe have an easily-accessible office in central London, as well as a number of regional offices throughout the UK and an office in Munich, Germany. We’d love to hear from you, so please get in touch.
Get in touch